Magnetized 3D Printing Technique Yields More Individualized Devices
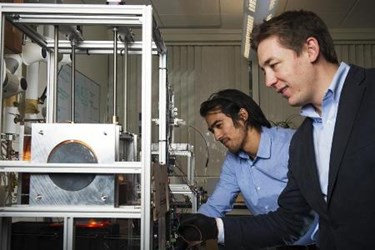
A new approach to 3D printing, developed at Northeastern University, could pave the way toward medical devices that are more individualized than is currently possible. Where previous methods have pre-designed a material, and then used it to print a device, this new method uses magnets to control the architecture of the composite, reinforcing its mechanical strength to suit the needs of the individual device — an advance researchers claim is particularly useful for pediatric medicine.
Because of the variance in size requirements, clinical enrollment issues, and a relatively small market, device manufacturers have shied away from addressing the medical device needs of children — so much so that the FDA recently released a guidance stipulating how much adult data could go into a clinical trial seeking pediatric labeling, hoping to “enhance and encourage pediatric device development programs.”
According to a keynote address by former FDA commissioner Margaret Hamburg last year, designing medical devices for children represents a particular challenge to medical device developers because of differences in size and physiology, development and growth rate, and activity levels. It’s not enough to take an adult-sized device and make it smaller.
“Scaling down an adult-size device for use in children brings potential mechanical challenges because thinner or shorter devices could change the product’s compositional properties,” said Hamburg.
Current 3D printing methods are using advanced medical imaging to precisely design and print devices that are tailored for individual patients, and they have achieved particular success with young children. Airway splints have been custom-fitted to the windpipes of newborns with tracheobronchomalacia, and 3D heart models can be printed to assist surgeons in planning complex cardiovascular surgeries. But, as Hamburg pointed out, there’s more to a perfectly fitted medical device than size and shape.
Randall Erb, an engineering professor at Northeastern, together with graduate student Joshua Martin, has developed a way to individualize the architecture of the material for each device printed. The pair works with composites of liquid polymers and ceramics, magnetized with a coating of biocompatible iron oxide. By passing a magnetic field over the liquid, Erb and Martin are able to precisely orient the fibers of the ceramics before using a laser to harden them, layer by layer, into a solid form.
Composites “are very strong and very lightweight,” Erb told The Boston Globe. “We’re replacing a lot of our planes and trains and cars with them. But if we don’t orient [the fibers], they go from strong to weak.”
A specific application of the technology — according to Erb — is patient-specific catheters for newborns, whose veins and tissue are far too delicate to accommodate an inappropriately sized device. “If you can print a catheter whose geometry is specific to the individual patient, you can insert it up to a certain critical spot, you can avoid puncturing veins, and you can expedite delivery of the contents,” said Erb in a press release.
“We are following nature’s lead,” said Martin, “by taking really simple building blocks but organizing them in a fashion that results in really impressive mechanical properties.”
The scientists and their team, who published their findings in Nature Communications, say their next goal will be to use calcium phosphate fibers and biocompatible plastics to design and print surgical implants.