Medical Device Metal-To-Plastic Conversion In 6 Steps
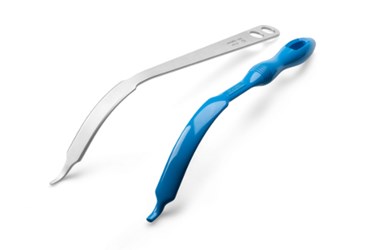
By Nathaniel W. Van Vliet and Dane Waund, Solvay Specialty Polymers
With quickly increasing healthcare costs and improving technology, designers across the medical device industry are being tasked to increase performance and decrease costs associated with their products. One of the most effective methods for performance enhancement and cost cutting is metal-to-plastic conversion. Plastics can be used to replace even the strongest and stiffest steel devices by incorporating simple design modifications.
High-performance polymers offer the same level of strength and rigidity as some metals at ambient temperature, along with added advantages. They deliver cost benefits, enhanced aesthetics, and ergonomic improvements such as a range of grip options. High-performance polymers can also be colored, thus enabling the production of devices in a variety of sizes that can be easily and quickly identified in the operating room.
Hip Retractor Showcases Benefits
An active participant in the metal replacement market for over 25 years, Solvay Specialty Polymers undertook an innovative commercial approach by applying its knowledge and expertise to develop case studies that help OEMs see the cost and performance advantages of high-performance polymers in medical devices. This article provides a foundation for polymer selection and documents a complete metal-to-plastic conversion of a retractor used in total hip replacement (THR) surgical procedures. The case study focuses on both single-use and reusable retractors.
Surgical retractors made of Ixef polyarylamide (PARA) and AvaSpire polyaryletherketone (PAEK) showcase the advantages of high-performance polymers over metals in medical devices (see image above). Designing in plastic leads to drastic cost reductions and also enables the OEM to sell single-use instrumentation, which is rarely economical using metal.
A hip retractor was chosen to demonstrate metal-to-plastic conversion for two reasons. First, retractors used in orthopedics are largely composed of metal, and second, the primary requirements of a retractor are high strength and stiffness. The Hohmann retractor, a popular device used in THR surgical procedures, presents challenging requirements including high mechanical loads. In single-use applications, Ixef PARA is used due to its strength and stiffness, excellent surface finish, and compatibility with gamma radiation sterilization. Because Ixef PARA compounds contain 50% glass fiber reinforcement, their strength surpasses that of known competitive thermoplastics, including carbon fiber-reinforced polyetheretherketone (PEEK). This enables instrument designs that offer comparable performance to their stainless steel counterparts. The material is injection molded, thus eliminating machining and reducing cost over stainless steel.
For reusable devices, AvaSpire PAEK delivers a range of advantages including a high stiffness-to-weight ratio, hydrolytic stability at elevated temperatures, excellent chemical resistance, and excellent aesthetics and colorability.
Stiffness, strength, and compatibility with repeated exposure to disinfectants and steam sterilization are critical requirements for reusable retractors, making AvaSpire PAEK ideal for these applications. The material is also easy to process, allowing designs incorporating long, thin geometries to be produced via injection molding.
Specifying plastics for medical devices can be a major challenge for those who have been used to working with and designing with metals. To help customers make this transition, Solvay conducted an in-depth study on end-use performance, biological safety, and economics. This report breaks down the metal-to-plastic conversion of the hip retractor into six steps: classification of polymers, material selection, improving strength and stiffness, prototyping, manufacturing, and validation.
Classification Of Polymers
With the many plastic materials available today, proper material selection for a given application can be a difficult task. It is highly recommended that you work with a knowledgeable materials supplier to help you select the best material based on end-use requirements, design, application, processing, and so forth.
Gaining an understanding of polymer type (amorphous or semi-crystalline) and performance tier (commodity, mid-range, high-performance, and ultra-performance) will help designers to identify a short list of potential materials that are suitable for their application.
Medical Performance Requirements
Medical devices often require high performance across multiple performance categories. The most challenging requirement for many polymers includes strong chemical resistance (due to exposure to aggressive cleaners) and the ability to withstand specific sterilization technologies (such as steam autoclaving or large doses of gamma radiation). Table 1 presents a graded performance overview for a selection of Solvay medical-grade polymers that are suited for a wide variety of medical devices.
Material Selection
Boundary conditions can be used to narrow the selection of appropriate materials for a given application. Table 2 presents a list of boundary conditions for both single-use and reuseable versions of the retractor.
Single-Use Device Material Selection
A single-use scenario assumes that the medical device will be sterilized with a gamma dosage between 40 and 100 kGy. Steam sterilization is not a requirement, though a single flash steam sterilization cycle or a wipe-down with a chemical cleaner in the operating theatre is not uncommon. As shown in Table 1, Ixef PARA meets or exceeds all requirements, in addition to being low-cost. As indicated in Table 3, the addition of glass-fiber reinforcement further reinforces desired properties. The specific grade of Ixef PARA that meets these requirements is GS-1022, which contains 50% glass-fiber reinforcement and is available in several gamma- stable (GS) colors.
Reuseable Device Material Selection
A reuseable scenario assumes up to 1,000 cycles of steam sterilization and repeat exposure to cleaning agents. Additionally, resistance to creep and fatigue is necessary to maintain long-term mechanical properties. Note that when designing a reusable medical device, it is important to use data generated after the material is exposed to the specified usage scenario (such as after 100 kGy gamma dosage or 1,000 cycles of steam sterilization). A reputable material supplier should be able to provide such data. Tables 1 and 3 show that AvaSpire PAEK is the lowest cost material that meets or exceeds all requirements and the addition of glass fiber improved required properties. The specific grade of AvaSpire that meets these requirements is AV-651 GF30, which contains 30% glass-fiber reinforcement.
Improving Strength And Stiffness
The most challenging obstacle of converting the steel retractor to plastic is the large drop in tensile modulus (stiffness). Table 4 presents a comparison of applicable properties for Ixef GS- 1022, AvaSpire AV-651 GF30, and 17-4 steel.
Despite being one of the stiffest medical-grade plastics in the industry, Ixef GS-1022 exhibits a tensile modulus that is one-tenth of that of 17-4 steel. The most effective method for improving a part’s stiffness is manipulation of the area moment of inertia. Two methods for improving stiffness are use of a rectangular geometry and the addition of ribs. As a result, plastics can mimic the stiffness of steel through simple design modifications. These types of modifications will be used in the metal-to-plastic conversion of the hip retractor.
Design Iteration
The design of the plastic hip retractor was largely performed with computer-aided engineering (CAE) to optimize unique design features which were not feasible with stamped metal.
The goal was to design a plastic retractor template from scratch, taking full advantage of the added design options made available by the use of plastic. The steel retractor was stamped from a sheet of steel, which greatly limited design potential. The plastic retractor was injection molded (for reasons discussed later), which provides nearly limitless design options. This allows the plastic retractor design to greatly improve the look and feel of the device, while still being able to imitate the stiffness of the steel retractor. To improve the feel of the plastic hip retractor, a large handle was added to improve the grip. The handle also served to provide a great deal of the required stiffness to the back end of the retractor. This improvement allowed for the front end of the retractor to utilize a smaller, rounder geometry.
Through modification of the cross-sectional areas, it was demonstrated that Ixef GS-1022 could readily achieve a stiffness that is 1.25 times that of the steel retractor. Using AvaSpire AV-651 GF30, a stiffness that is 0.75 times that of the steel retractor could be achieved. The model was also transferred to the real world by 3D printing via selective laser sintering (SLS). The feedback regarding the general form of the hip retractor was positive. Therefore, the second design iteration was successful.
Prototyping
Prototyping is recommended to examine the user’s experience and/or the performance of a design before incurring the full costs of manufacturing. The prototyping process is best started during the design phase, as demonstrated by the plastic hip retractor. More than one prototyping method may be appropriate. In the case of the plastic hip retractor, the primary goal was to evaluate the feel of the retractor.
Additive Manufacturing
3D printing is one of the fastest ways to obtain a physical copy of a design and allow for effective evaluation of the feel of the part. The most common methods include SLS, stereolithography (SLA), and fused filament fabrication (FFF). The disadvantages of additive manufacturing include reduced mechanical performance and the limited number of high-performance and ultrahigh-performance materials available. Therefore, the use of additive manufacturing for verifying the part’s mechanical performance is not recommended. All iterations of the hip retractor were printed out of nylon 6 using the SLS method. The hip retractor prototypes were used to obtain the feedback necessary to optimize the feel of the retractor.
Manufacturing
There are many manufacturing methods for plastic devices, and the most common methods for surgical instruments are machining and injection molding. Because it was estimated that 3,500 hip retractors would be required over the span of three years, injection molding was chosen over machining as the more economical method. Injection molding is a lower-cost process for large volumes due to automation. It also provides design flexibility, fast turnaround, and easy molding of complex geometries.
A medium-sized mold was required for the hip retractor. The size of the tool was doubled to allow for a future project. The mold material requested was H13, which is one of the highest quality mold steels available. Finally, a special feature allowed for the handle portion of the hip retractor to be replaced with an alternative design.
The material and mold cost, combined with the estimated processing costs, was approximately $100,000. Per part, this translated to approximately $10 for each single-use part composed of Ixef GS-1022, and approximately $18 for each reuseable part composed of AvaSpire AV-651 GF30. Since it was one-fifth the cost of machining, injection molding was the chosen manufacturing method.
Validation
Single-use (Ixef GS-1022) and reuseable (AvaSpire AV-651 GF30) versions of the retractor were submitted for testing via the same method utilized to map the steel retractor’s performance during the beginning of the design phase.
The Ixef GS 1022 retractor was demonstrated to be slightly stiffer than the steel retractor. The AvaSpire AV-651 GF30 retractor was demonstrated to be slightly less stiff than the steel retractor. Both versions of the plastic retractor weighed in at approximately 50% less than that of the steel retractor, which would significantly decrease the weight added to a surgical tray.
It was successfully demonstrated that both steel and plastic retractors could exhibit comparable mechanical performance. At the same time, it was determined that the cost of a reuseable hip retractor is cut in half with plastics. Designing a plastic retractor also enables the OEM to sell single-use instrumentation, which is rarely economical using metal.
Resources for designing with plastics are expanding for the healthcare industry. As a result, plastic material suppliers are increasing their focus on this industry, adding resources to aid in adopting plastic and metal-to-plastic conversion. Processors who have worked exclusively with metals are developing expertise with plastic manufacturing methods. OEMs are hiring designers with a backgrounds either partially or fully involving plastics.
With quickly increasing healthcare costs and improving technology, designers across the medical industry are learning to increase performance and decrease costs through the utilization of high-performance plastics.
About The Authors
Nathaniel W. Van Vliet is a technical marketing engineer for Solvay Specialty Polymers. Dane Waund is the global healthcare manager for Solvay Specialty Polymers. For more information, contact Dane Waund at dane.waund@solvay.com.