Medical Plastics: Material Selection Based On Feel
By Eric Larson, Art of Mass Production
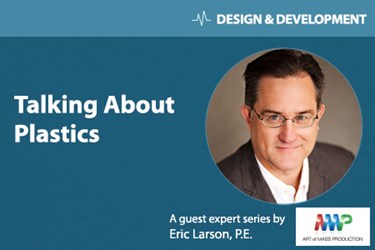
In our previous article, we talked about plastic material selection and some of the unique challenges of medical device design, from performance and safety requirements to environmental effects and cost considerations.
Primarily, though, we discussed the importance of feel in medical device design, referring not just to tactile perception, but to the entire user experience — all of the sensory input we receive when interacting with a device, all of the sensations (physical, mental, psychological) we experience from that input, and all of the memories and emotions that experience evokes. In this article, we explore some of the ways to evaluate plastic materials to achieve the desired feel for a given device.
Plastics And Feel
The notion of using a plastic material to influence the feel of a medical device may seem, for lack of a better word, ridiculous. We all know that plastics are cheap, flimsy — practically worthless. Furthermore, the word plastic often is synonymous with fake: plastic flowers, plastic people, plastic surgery. So how does one use a cheap, flimsy, practically worthless material — one that is basically fake — in the design of a medical device? It’s actually quite simple — you use plastic materials the same way you would use any other material, with the added advantage that plastic materials offer a unique opportunity to customize every aspect of feel.
For example, consider medical device safety. However, set aside clinical measurements of safety and consider instead the human experience of feeling safe. This is not an emotion per se, though emotions may be involved. Instead, this feeling is a complex combination of thoughts, memories, and experiences that — combined with sensory input (sight, smell, sound, touch, and taste) and various body sensations (warmth, comfort, etc.), as well as the absence of other body sensations (nausea, dizziness, etc.) — result in the comfort of feeling safe.
This experience of feeling safe can be enhanced not only by the design of medical products involved, but also by their materials. Consider, for example, safety glasses with lenses made of impact-resistant polycarbonate, seat belts made of nylon (polyamide), bullet-proof vests made of aramid fiber (aromatic polyamide), or barrier films used to prevent the transfer of pathogens. We know that these materials keep us safe, not just on an intellectual level, but also on a deeper level. All of the available sensory input tells us that everything working exactly as it should, and that we are safe.
Evaluating Feel
One great challenge in selecting plastic materials based on feel is establishing the proper evaluation criteria. What material properties should we be concerned with, and what are the desired values for each property? How do each of these properties contribute to the feel of the material, as well as to user response to the device? Stated simply, feel is a complicated phenomenon.
For most people, feel is synonymous with touch. A person saying, “Here, feel this,” most often means, “Here, touch this.” While our sense of touch plays a critical role in feel, defining feel based solely on touch overlooks a number of important factors.
For example, consider six samples of different materials, each one with a physical surface identical to the next — the exact same surface roughness, waviness, etc. Included in this sample set is a piece of concrete, a piece of fabric, a piece of fine sandpaper, a machined mold surface, a molded plastic part, and an iPad. To further refine the experiment, put the samples in a climate-controlled room until they all are the same temperature.
As you lightly touch each sample with your fingertips, an interesting thing happens: Each sample feels different. Six identical surfaces, yet six different responses. Why? Your fingertips’ capability to evaluate sensory input extends beyond surface roughness. There is thermal conductivity, electrical conductivity, the sensation of hardness, and more. And, if you were to pick each sample up, there would be an assessment of weight and density, how vibration travels through the sample, and more. Again, each sample would feel completely different. In addition, we might have emotional and physiological reactions as we held each sample, depending on our life experiences.
Understanding the complexity of sensory input is the first layer in the process of material selection based on feel. The basic mechanism of stimulus and response is similar for all of the senses, and the process of material selection is the same, regardless of which senses are involved. Rather than describe this process as plastic material selection based on a comprehensive evaluation of sensory input, I prefer the simpler phrase, material selection based on feel.
Evaluation Based On Sensory Input
Sense of touch often is synonymous with feel and is highly developed, especially in our hands, feet, and face. When it comes to medical devices, especially hand-held medical devices, sense of touch can be critical.
The increasing popularity of wearable medical devices — carried or attached to our bodies most frequently about the arms, chest, or neck, but sometimes to our clothes — has further bolstered the importance of sense of touch. Thus, we are dealing with material issues (thermal conductivity, electrical conductivity, material hardness, density, etc.) and, if wireless connectivity is involved, we have to consider RF transmission (or absorption) rates, and perhaps even optical clarity and light transmission rates at various wavelengths.
So how does one effectively evaluate these properties to determine the “best” material for a wearable device? The simple answer is, you can’t: The evaluation matrix is too complicated. Instead, it is preferable to undergo a de-selection process, where key performance variables are used to disqualify materials. The goal of this process of elimination is to identify two or three chemical families that are suitable — for example, polycarbonate, high temperature nylon, and polysulfone. From there, the evaluation of feel can proceed.
As you evaluate a material, it is helpful to consider the what, rather than the how. In other words, instead of asking someone, “How does this material make you feel?” ask “What do you feel?” Is it cold, hard, rough, wet, slippery, silky, stiff? This question often is easier to answer, and the nuances in its answers can be explored later.
There also is a movement toward the use of “soft touch” plastic materials, and not just in wearable devices. A common perception is that “soft touch” materials are soft — that is, the material hardness is low. But, a hard material — with the right texture and the right combination of smoothness/slipperiness/stickiness — can also provide a sense of feeling “soft.” This is especially true for thermoplastic elastomers. These flexible materials (elastomer = elastic + polymer) are thermoplastic in nature, meaning they can be melted and re-melted, unlike natural rubber (or silicone), which cures to a solid state and cannot be re-melted.
In the area of feel, thermoplastic elastomers offer a range of options, based on a combination of material hardness, material stiffness (flexibility), the ability to stretch (elasticity), the rate at which a stretched material returns to its original state (dynamic recovery, or “springiness”), and how it reacts against our skin (smooth, silky, sticky, slippery, etc.).
Sight
Our sense of sight also is highly developed, and quite often, what and how we feel is affected by what we see. This is not just the details of what we are seeing, but the sizes, shapes, colors, and textures of the objects around us.
In medical device design, the use of a material often depends on the manufacturing process being used. The size and shape of an object made from plastic depend on whether it is thermoformed, or extruded, or injection molded, and that process also can limit the choice of material. But the color, and to a lesser extent the gloss level, often is inherent to a given material. Some materials, such as ABS, have an inherently high gloss level, which often is desirable. Other materials, such as polypropylene, have a lower gloss level, which may affect how we interact with and respond to the device.
Selecting thermoplastics based on color usually is done using performance-based criteria: A certain color must be within specific color tolerances, and last for a certain period of time under certain environmental conditions. The choice rarely is made using feel-based criteria, specifically, based on human response to color.
To understand how we respond to color, it is necessary to look outside the field of engineering. In psychology exists a field known as color psychology, and one of its best known books is Color and Human Response, penned by color consultant Faber Birren. But I remain unaware of any studies or books that seek to evaluate response to color as it applies to thermoplastics. What colors — and in what materials — can help to elicit the response you want? Should a white aspirin bottle have a red polypropylene cap? Or should it be a blue bottle with a white polycarbonate cap? What color best suits the “Go” button on your Epipen?
Hearing
Our sense of hearing often is overlooked in medical device design. Some devices may beep or buzz or emit a warning tone, but in very few situations are materials selected for specific sound characteristics.
There is a field of study called psychoacoustics that deals with the psychological and physiological response associated with sound. We are familiar with the visceral reaction we experience after hearing the sound of fingernails being dragged across a chalkboard; Why not consider the response a user has after hearing the sound of a medical device in use (e.g., the drone of a dental drill or the steady beep of a heart monitor)?
Evaluation Issues
The process of evaluating materials based on feel is not conducive to a strict protocol, or to using tools and equipment capable of precise measurements. Recalling our earlier example of the concept of safety, how does one measure “feeling safe?” Do you measure resting heart rate? Pupil dialation? Galvanic skin response?
Rather than focusing on precision, it often is easier — and more productive — to make comparative evaluations in a classic “A vs. B, B vs. C” scenario. For those who prefer a mathematical approach, consider the following equation:
Xtl < Xjr < Xtm
Here, X represents the “feel” factor we are evaluating; Xtl represents too little of X; Xtm represents too much of X; and Xjr represents the just right amount of X. Rather than solving for a specific value of feel (X), we are comparing values, and then making a determination of “greater than” or “less than.” This equation is based upon the work of the British author and poet Robert Southey — best known as the author of the classic children’s story, Goldilocks and the Three Bears, a story about making selections based on feel.
The purpose of this evaluation is not to achieve the perfect feel. In fact, human responses to sensory input can vary greatly, depending on the user and on what aspect of feel is under evaluation. But, it almost always is possible to determine a user preference.
The challenges in selecting materials based on feel are not unique to the medical device industry. Feel is overlooked in many industries and, even when there is a direct intent to select a thermoplastic material based on feel, there are few resources available. However, the fact remains that feel is a critical component of any product.
A Final Word About Feel
A few years ago, as I wrote a book on plastic material selection — specifically, a chapter dedicated to the concept of selecting materials based on feel — a close friend of mine suffered a bad accident and ended up in a coma, on life support, with no hope of recovery. His family made the difficult decision to turn off life support, but offered his friends one last chance to see him and say good-bye.
Saying good-bye was one of the hardest things I have ever done. As therapy, I dove back into my writing. I wrote about thermal conductivity and heat sensitivity and human response and product performance. I worked on tables and flow charts and compelling arguments. But I kept thinking about my friend, lying in a quiet room, surrounded by medical technology.
The funny thing is, I could probably name the material and manufacturing process used for every part on every product in that room — from touch screens to tubing, tissues to toilet seats, even the fabrics and fibers used on his hospital gown.
In times of distress, we often rely on habits and rituals that are intended to soothe our senses. We listen to music. We sing, we laugh, we cry, we send flowers — we work. We have food and drink to nurture our bodies, and to comfort us. Chicken soup. Cake. Ice cream. Along with other therapies. Here, take this, it will make you feel better.
All of the devices, implements, and therapies in that quiet room may have been clinically effective for their intended uses, but they didn’t make anyone feel better.
The Language Of Feel
For most of us in the world of science and technology, talking about feel is an unusual concept. It can be a subjective exercise, often filled with ambiguity and confusion. However, if we can find the right language, we usually can describe a subjective experience in a factual, objective manner, and in a way that anyone can understand. I like to call this the language of feel. We will explore the use of this language in greater detail in our next article.
About The Author
Eric R. Larson is a mechanical engineer with over 30 years' experience in plastics. He has helped develop products ranging from boogie boards, water basketball games and SCUBA diving equipment to disposable lighters, cell phones and handheld medical devices. Eric is owner of Art of Mass Production (AMP), an engineering consulting company based in San Diego, CA. AMP provides services to manufacturing companies in the consumer electronics, wireless, and medical device industries. Eric is also moderator of the blog site plasticsguy.com, where he writes about plastics technology and its effect on people and the planet.