Rapid Manufacturing Of Metal Components For Medtech Applications
By Rob Bodor, VP and GM of the Americas, Proto Labs
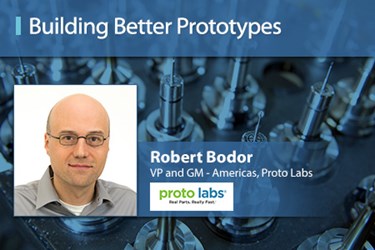
In my previous post, I talked about the benefits of using thermoplastic injection molding for medical device development. Now, I’d like to transition to metal manufacturing. As rapid prototyping has evolved, so have the ways in which metal is fabricated. You not only have traditional methods like CNC machining and die casting, but advanced processes like metal injection molding (MIM), magnesium thixomolding, and an additive manufacturing (3D printing) process called direct metal laser sintering (DMLS) that is increasingly being used to produce parts for medical applications.
To start, let’s look at some of the frequently used metals. From harder to softer, this range of metals includes steel, stainless steel, aluminum, brass, and copper.
Aluminum And Magnesium
Another popular lightweight material is magnesium, which is the fourth most abundant element in the earth’s crust. Two-thirds the weight of aluminum and nearly as strong, it is the lightest of all structural metals. Magnesium is a preferred material wherever good strength and low weight is important. It has excellent dampening characteristics, is very machinable, and is readily molded or die cast.
Brass And Copper
Rounding out the soft metal lineup are brass and copper and, of the two, brass is by far the most versatile. With the exception of environments high in ammonia and some acids, it is extremely weather and corrosion resistant. To a machinist, brass is as easy as it comes: coolant is optional, tool life exceptional, and feed rates quite high. Don’t let its easygoing nature fool you, though — brass is sturdy stuff, offering tensile strength rivaling that of mild steel.
Copper is second only to silver in electrical conductivity, a factor that makes it one of the most important metals in use today. Copper is easy to braze but difficult to weld. Its extreme ductility makes it both strong and flexible, a rare occurrence among metals. It’s used in semiconductor manufacturing, in glass-to-metal seals — such as those needed for vacuum tubes — and it has even been approved by the United States Environmental Protection Agency (EPA) for use in hospitals and public places as an antimicrobial surface.
Steel And Stainless Steel
The world needs hard metals, as well. Regardless of alloy type, steel is mostly composed of iron. As with the soft metals, a small quantity of alloying elements can have a dramatic effect on steel’s properties — the addition of less than 1 percent carbon and manganese, along with a little metallurgical legerdemain, is what makes brittle iron into tough 1018 steel. And 4140 alloy steel, suitable for aircraft use, is made by combining an equally small amount of chromium, along with a dusting of molybdenum.
Since rust never sleeps, metallurgists developed stainless steel. By increasing the amount of chromium to at least 10.5 percent, corrosion resistance is greatly enhanced. Many stainless steels are temperature resistant as well, and are able to withstand temperatures upwards of 2700˚F, hot enough to turn aluminum, brass, and copper molten. It’s commonly used in the medical industry where a combination of high strength and good corrosion resistance is needed.
Metal Injection Molding (MIM) And Thixomolding
For increased metal part production, machined components are often transitioned to casting or molding processes. But when you’re developing and testing a device, it is advantageous to have a few low-volume manufacturing options available. Proto Labs offers metal injection molding and magnesium injection molding (aka, thixomolding) that serve those applications well, for parts quantities of 100 to 10,000 or so.
Direct Metal Laser Sintering (DMLS)
For parts impossible to manufacture through any of the methods previously discussed, there’s the additive manufacturing process of direct metal laser sintering. DMLS boldly goes where other manufacturing processes can’t. Like its plastic counterpart, selective laser sintering (SLS), which uses a laser to fuse nylon-based powder into almost any shape imaginable, DMLS achieves similar results in metals such as aluminum, cobalt chrome, Inconel, stainless steel, and titanium.
Tolerances to +/- 0.003 in. are typically possible with DMLS, along with part features smaller than the period at the end of this sentence. Because of this, DMLS works great for very small, precise metal components for surgical instruments and other medical applications.
Material And Process Selection
As with plastics, identifying the right metal and process to manufacture your parts with is not only a balance of design considerations — like part size, complexity, application and material properties — but supplier capabilities, such as cost, turnaround time, and part quantity. Regardless of which process is initially chosen, there’s a good chance that you may need more than one during the development of your device, its launch to market, and throughout its life cycle.
Proto Labs is quick-turn manufacturer of custom prototypes and low-volume production parts. From 3D printing to machining to molding, it offers various metals across all of the manufacturing processes discussed, which can be leveraged in each stage of the design process.
About The Author
Rob Bodor is currently VP and GM of the Americas at Proto Labs, a leading online and technology-enabled quick-turn manufacturer of custom prototypes and low-volume production. At Proto Labs, he has also held roles as CTO and director of business development. Prior to joining Proto Labs, Bodor held leadership roles at Honeywell and McKinsey & Company, and has been on the executive team of two early-stage software companies in the Twin Cities. Robert holds B.S., M.S., and Ph.D. degrees in engineering and computer science.