RFID-Enabled Breast Implants And The Future Of Medical Device Tracking
By Jim Pomager, Executive Editor
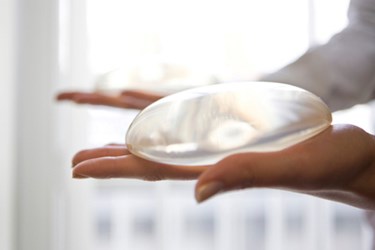
Poly Implant Prothèse (PIP) was once one of the largest manufacturers of breast implants in the world. Founded in 1991, the French company produced up to 100,000 breast implants per year, and an estimated 300,000 women in 65 countries were recipients of its products. In 2009, however, surgeons began reporting unusually high rupture rates among PIP implants. Not long after, it was revealed that PIP had been using industrial-grade silicon in its implants, rather than approved medical grade material.
French regulators quickly yanked PIP implants off the market in 2010 and incited worldwide panic in 2011, when they recommended that 30,000 women in France with PIP implants have them immediately removed. In the weeks and months that followed, women across the globe rushed to determine whether their implants were manufactured by PIP. Many had lost or misplaced their product or warranty cards, so they turned to their physicians for guidance. Some endured anxious days waiting for responses from surgeons, and for others word never came —not all surgeons still had files on hand indicating what type of implant was used in each procedure.
Fast forward to October 2013, when a company called Establishment Labs received CE Mark approval for a product that sure would have come in handy during the PIP scandal of 2011 — a breast implant with an RFID (radio frequency identification) microchip embedded in it. Hailed by its creators as the “world’s first externally identifiable breast implant,” the Motiva Implant Matrix Ergonomix allows physicians to immediately ascertain manufacturer name, serial number, lot number, batch number, and other implant-specific data in vivo by merely scanning the area outside the body with a handheld reader.
The RFID technology behind the Ergonomix implant was provided by VeriTeQ Corporation. Known as Q Inside Safety Technology, the system consists of an FDA-approved implantable transponder chip, a proprietary handheld reader, and a secure online database. Each microchip contains a unique alphanumeric code, which can be retrieved by the reader and then used to access accurate device information from the database via the Internet.
The Q Inside microchip is a nifty little piece of hardware. It measures only 7 mm x 1.25 mm in size, making it easy to integrate into implantable device designs. (It free-floats inside the Ergonomix implant.) As a passive chip, it requires no internal battery; rather, it is powered by signals from VeriTeQ’s reader when it comes into range (within 6 inches). It operates in the 134 kHz frequency band, is compatible with a range of polymers and materials, and is write-protected (i.e. it could potentially be used for read/write capabilities). It also can withstand temperatures of up to 195° C for a duration of 4 hours, making it capable of enduring sterilization during the manufacture of breast implants and other implantable medical devices.
VeriTeQ's Q Inside microchip
Speaking of other implantables, VeriTeQ’s microchip has also been designed into a Medcomp vascular port, where it will ensure accurate device identification and chemotherapy dosage prior to treatment. (Medcomp is currently seeking FDA approval for the device.) Scott Silverman, chairman and CEO of VeriTeQ, told me that the company currently has working relationships with a total of 16 different medical device manufacturers and sees great opportunity for eventually embedding Q Inside in artificial joints, pacemakers, and other implantable technologies.
RFID technology like VeriTeQ’s (and others that will inevitably come along) could play a significant role in helping manufacturers achieve compliance with the recently issued FDA unique device identification (UDI) final rule. Among the rule’s many requirements is one mandating direct part marking (DPM) for all reusable devices that are reprocessed before each use. This means that both a device identifier (designating the version/model number and name of manufacturer/labeler) and production identifier (lot/batch number, manufacture date, expiration date, etc.) must be affixed to the device itself, not just on the device packaging. This DPM identification may be provided in either plain text (e.g. etched) or in a form that uses automatic identification and data capture (AIDC) technology. There are many AIDC methods, but the two most prominent are bar codes and — you guessed it — RFID.
For this reason, VeriTeQ has targeted reusable/reprocessable devices as a primary application area for its Q Inside technology. For example, the company is working with a breast implant partner to evaluate the use of VeriTeQ’s RFID chip in breast implant sizers, which are temporarily inserted in the body during surgery to determine the appropriate implant size for a patient. Sizers are also used in surgeries involving facial implants, heart valves, and other implants.
As an identification technique for sizers and other surgical tools, RFID holds some significant advantages over plain-text marking and even other types of AIDC. “Simply waving an RFID scanner over a device is a lot easier than cleaning biological product off of it to find out exactly what the model number is,” Silverman explained. VeriTeQ is also exploring the possibility of using its chips in gastroenterology products like colonoscopes and endoscopes.
While the final UDI rule (somewhat surprisingly) didn’t require DPM of implantables, there are still compelling reasons to implement RFID technology in these devices. The obvious one is to enable rapid, accurate data retrieval without having to remove the implant from the patient, particularly in the event of a safety issue — like a product recall or an adverse event report — as was the case with the PIP implants. Unlike product and warranty cards, implanted identification can never be lost or misplaced.
Silverman also believes that forward-thinking device makers will adopt RFID technology to inoculate themselves from future threats, whether they come in the form of product litigation, patient advocacy group pressure, or even revisions to the UDI rule. “We still believe that direct part marking of implantable medical devices will become a mandate,” he said. “I think the manufacturers and their lobbies all recognize the need for it. It’s just a matter of how and when it comes back to the forefront with their cooperation, as opposed to the FDA forcing it upon them.”
Only time will tell if that prediction comes true, but in the meantime, RFID technology still has a lot to offer the medical device community. One intriguing possibility is preventing the spread of counterfeit medical devices. “The VeriTeQ tool could be used as a way to short-circuit counterfeit devices,” Tom Beatty, senior principal of UDI compliance at QDevice (the medical device consulting division of QPharma), told me. “You could say, ‘Only genuine product will contain this VeriTeQ RFID technology.’ That could be quite valuable to manufacturers of products that are often counterfeited.” VeriTeQ also envisions Q Inside playing an important role in inventory management and workflow management at the manufacturing level and at the physician/hospital level.
Potential applications for RFID technology in implantable medical devices extend well beyond identification. For instance, VeriTeQ is working with a major university and its hospital chain to explore data analytics opportunities. The organizations will look to collect data from devices within the body and then tie that information to everything from personal health records to predictive outcomes for future patients (using information gathered from prior patients using the same device).
The possibilities are almost limitless. Expect to hear a lot more about novel applications for RFID technology in implantable and reusable devices — and other medical technology — in the coming months. Now is the time to consider how you can leverage RFID to improve the traceability, safety, and functionality your own design, if you haven’t done so already.