Plastics Selection For Medical Wearables: Getting Personal
By Eric Larson, Art of Mass Production
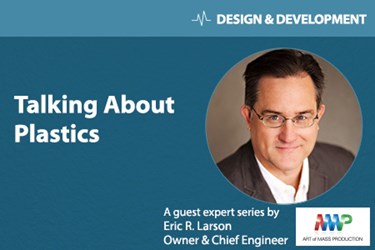
This article is the second in a three-part series. You can read part one here. Finish up with part three here.
One of the unique aspects of wearable devices is that they are personal. Just as our attitude and sense of fashion define who we are as individuals, a wearable device becomes an extension of our identity. As such, the appearance of a device, and its size, weight, and overall feel are just as important as the communication requirements.
Appearance Requirements
Often, the appearance of a molded plastic part is a critical design concern. While this often involves color, it also involves gloss and texture.
Color is a complex subject, involving physical, physiological, and psychological factors, and a thorough discussion is beyond the scope of this article. Color obviously involves visible light (including the wavelengths of the light source, how they are reflected by the object being viewed, and how they are perceived by the viewer), but it is just a part of appearance, along with the gloss level and texture of the surface reflecting the light.
In the world of plastics, gloss and texture are poorly understood phenomena, yet both play an important role in the appearance of a molded plastic part.
Gloss is used to describe the manner in which a surface reflects light. The surface can reflect light in a pure mirror-like fashion (known as a specular reflection), it can scatter the light in a number of different directions (known as diffuse reflection), or it can absorb the light. There also can be a combination of specular reflection, diffuse reflection, and absorption. Many people confuse the term gloss with the concept of smoothness. However, gloss is not a description of surface smoothness (or roughness), it is a property of the material itself. As an example, a marble surface, even when polished perfectly smooth, will not provide a pure specular reflection like a common mirror, which usually is made by taking a piece of polished glass and coating it with a thin layer of aluminum or silver. Both aluminum and silver are high-gloss materials, whereas marble is a lower-gloss material.
The concept of gloss can be explained by the sheen (the shininess) that is offered in various paint finishes, ranging from very dull (also known as flat or matte) to very shiny as the gloss level increases, from flat through eggshell, satin, silk, semi-gloss, and high gloss. [Note: These terms are not standardized, and while the color or surface smoothness of the paint does not change, the final appearance most definitely does.]
Texture also plays a critical role in appearance. In plastic parts, the term texture refers to surface texture, and it is used to describe the part surface’s physical condition.
When we describe a molded part’s surface texture, we typically think of the textures (plural) that were on the surface of the mold, which have been transferred to the part’s surface. We often forget that the textured surfaces in the molded part are NOT a perfect replica of the textured surfaces that were in the mold. The molded part will have surface imperfections, minor deviations here and there, etc. Even if the mold surface is smooth – that is, a mold that was highly polished - the molded plastic part will NOT have the same level of smoothness as the tool. Furthermore, I would postulate that every thermoplastic material will have its own unique signature in how it replicates the mold surface. I think of this as the material texture.
In addition, unlike fabricated metal parts, molded plastic parts rarely undergo any secondary finishing processes (buffing, polishing, etc.). So, the surface texture on a plastic part typically is an “as fabricated” texture, and will be dependent on the specific plastic material as much as the mold texture (as well as the processing conditions). Unfortunately, there is no published data on material texture for molded plastics, as far as I know.
Finally, there is material color. Every thermoplastic material has its own innate color. Some are clear, while others are a milky white, brown, or black (a thermoplastic material in its innate color state is referred to as natural, regardless of the exact color). Furthermore, every thermoplastic material responds to pigments in a different way. These pigments — whether they are dyes, solids, powders, or flakes — are what determine the final color of the molded part. However, how the material responds to the pigment is a critical aspect of overall appearance. Is the final color rich and vibrant? Or is it dull and muted? Does the pigment affect the gloss level of the material? Does it affect the surface texture? Selecting a thermoplastic material for optimal appearance should include considerations for all of these issues.
Wireless Connectivity
A major requirement of modern wearable devices is wireless connectivity, which can be achieved through various means. The most common connection methods are via wireless networks, which often are described in terms of the frequency in which the network operates. Common cellular networks include GSM (380 – 1900 MHz) and 3G (700 – 3500 MHz), while area networks include Bluetooth (2.4 GHz) and Wi-Fi (2.4 and/or 5 GHz).
For a wearable device, we typically want a material that is radio frequency (RF) transparent, that is, we want it to transmit RF signals clearly, with no loss of signal. This is especially true for materials that are used to enclose the electronics, or any material that is near a sensor or an antenna. In the world of physics, signal loss often is described as a dissipation factor.
Ironically, one of the characteristics of thermoplastics is that they have good electrical insulating abilities (especially when compared to metals). In other words, they resist an electrical signal very effectively. Now, we want to maintain that insulating capability, but also have RF transparency. Unfortunately, while data on electrical resistance is readily available for most thermoplastic materials, there is very little data available on RF effects (dissipation factor). While signal loss can be assumed to be low for most thermoplastic materials, end-use testing for critical cases should be conducted to verify the material’s suitability.
Other Electromagnetic Requirements (EMR)
RF represents a very small of portion of the electromagnetic spectrum, which also includes microwaves, infrared, visible light, ultraviolet (UV) light, X-rays, and gamma rays.
Electromagnetic (EM) waves are a form of energy that is composed of an electrical field and a magnetic field. The wavelength of a wave decreases as its frequency increases. Microwaves have wavelengths ranging from 1 m down to 1 mm, whereas gamma rays have wavelengths as small as 1 picometer (10-12 m). The amount of energy carried by these waves increases as the frequency increases (and the wavelength decreases). Gamma rays carry the most energy, followed by X-rays, then UV light, etc.
In thermoplastic material selection, we typically are concerned with whether a given thermoplastic, and the additives it contains, will block a given frequency of EM waves, or transmit them without loss. For example, in optical applications, we typically want all light in the visible spectrum to be transmitted, without concern for other wavelengths. In an electronic shielding application, we may want to block transmission of EM waves in a certain band of the RF spectrum.
On occasion, medical wearables may also carry a requirement to allow for some transmission of visible light in certain frequencies (so we can see a flashing LED, for instance), or to provide shielding against a specific EM frequency range.
UV Stability
A typical requirement of wearable devices is that they remain stable when exposed to UV light for long periods of time, not just in terms of color stability (fading, yellowing, etc.), but also in terms of material properties.
The most common source of UV light is sunlight, which also contains EM waves in the visible light and infrared spectrums. Long-term, continuous exposure to direct sunlight means the material will be exposed to a lot of energy, sometimes with detrimental effects. (This occurs in a number of materials, not just thermoplastics.) If the polymer is transparent to specific frequencies, the energy in those waves passes through. If not, the energy in those waves will be absorbed by the material, which can result in a breakdown of the polymer chains, or converted into heat (which may have other consequences).
Each polymer responds to UV light differently (and each polymer responds differently to different EM wavelengths). Some materials, such as Acrylonitrile styrene acrylate (ASA) have inherently good resistance to UV. Other materials, such as Acrylonitrile butadiene styrene (ABS) and polyamide (PA, a.k.a. nylon) easily degrade under long-term exposure to UV. It is common for resin suppliers to offer versions of a resin described as “UV stabliized” – these resins have additives which absorb the UV radiation, and then emit it as low level heat. These UV stabilizers can enhance color stability and ensure long-term performance.
Feel Requirements
Finally, we must consider the various aspects of feel affecting the device. Again, feel refers not just to the size and shape of the device, but all the tactile sensations we experience, plus the sound and the smell (if any). Sound is related to vibration, and there are tactile and auditory components to sound, especially when in contact with the skin. The snap, click, or thump of various device components can be heard and felt, and the materials used will significantly affect that sensation.
Consider also the human experience of feeling safe. This experience involves a complex combination of thoughts, memories, and life events that — combined with sensory input and various body sensations (warmth, comfort, etc.), as well as the absence of other body sensations (nausea, dizziness, etc.) — result in one feeling safe. Effective material selection can enhance this experience, and poor material selection can create feelings of discomfort and unrest.
While many design teams pay attention to how a user interacts with a device (the user interface), it is not as common for teams to evaluate how a user responds to a device.
As an example, many people wear eyeglasses — either for vision correction or eye protection — while others opt to wear contacts or have vision correction surgery. Regardless of the treatment protocol, most people feel good afterward. Beyond the clinical result (i.e., improved vision), they may feel smarter, sexier, younger, or more energized. We have an entire industry that presents eyeglasses as a fashion accessary. Contrast this with hearing impairment. Many people who wear hearing aids prefer to hide their use of the devices, citing as reasons that hearing aids make them feel older, feebler, or more vulnerable. Furthermore, as a society, we respond to people with eyeglasses differently than we respond to people with hearing aids. We often think of people with eyeglasses as smart or well-educated, whereas we may think of people with a hearing aid as feeble. (Related: I have yet to see a hearing aid made of carbon fiber composite. Why not? It would be light and stiff, and it would convey an aura of speed, modernity, and technological sophistication.)
This concept of how a user responds is an important aspect of medical wearables, and I would also postulate that it is a huge factor in patient compliance. Appearance and overall performance may play an important role in what we think of a device, but overall feel is key.
About The Author
Eric R. Larson is a mechanical engineer with over 30 years' experience in plastics. He has helped develop products ranging from boogie boards, water basketball games and SCUBA diving equipment to disposable lighters, cell phones and handheld medical devices. Eric is owner of Art of Mass Production (AMP), an engineering consulting company based in San Diego, CA. AMP provides services to manufacturing companies in the consumer electronics, wireless, and medical device industries. Eric is also moderator of the blog site plasticsguy.com, where he writes about plastics technology and its effect on people and the planet.