The Role Of 3D Scanning In Orthopedic Development And Manufacturing
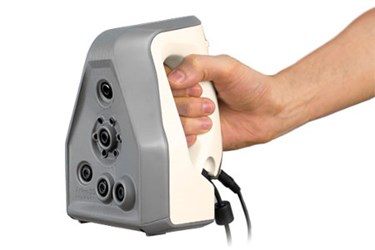
By Andrei Vakulenko, VP of new markets, Artec 3D
To steal from old jokes, what do an orthopedist and a construction worker have in common? The answer is both use plaster. Fortunately, digital technology has helped orthopedics to make great strides and to move away from using plaster for casts and molds. In just a few years, plaster will be as rarely used by doctors as pencil and ruler designs by engineers. Plaster will be back to the construction sites, where it belongs.
In the past, to make a custom brace for a patient, the patient would be covered in plaster and would have to lie motionless until the plaster hardened. It would then be cut off the patient and the mold would be sent via regular mail to a brace manufacturer. There, all measurements would be done manually, and the brace would be sent back to the doctor for a final fitting. If it did not fit, the process restarted from the beginning. Digital technology is making the process of creating prosthetics much faster and simpler.
3D Scanners Increase Accuracy
Creating prosthetics now involves the use of 3D scanners to model the correct size. A full 360 degree scan takes 30 seconds at 15 frames per second (fps). Sizing can be determined in five minutes via a single macro command, which starts an optimized sequence of instructions and parameters. The files are then sent by email to the manufacturer and CAD-directed milling machines that carve out metals and other solids to create a prosthetic device that can be shipped in one day.
In addition to being part of the manufacturing process for body braces and casts, 3D scanning can also be used to diagnose spinal disorders such as scoliosis, kyphosis, lordosis, and rotational spondylolisthesis in early stages. Because scanning is harmless, it can be done much more frequently than X-rays and can quickly diagnose physical variations. Wheelchairs can be correctly sized to a patient by having the patient sit in on a vacuum bag that is scanned. The scanners are also used to create custom back braces by scanning the patient’s body. Some clients use the devices to design protective helmets for babies with head damage. The babies wear a special hat, and the scanner scans the shape in order to create a helmet that fits tightly.
Despite such strides, we are only at the very beginning of the process of digitalization. There can be instances when scanning a person is difficult. For example, when a patient is bed-ridden but needs a full body scan. There is an alternative process, but it is a bit unwieldy. The 3D scanning process remains at an active research stage with open considerations such as:
- What should be the sequence of scanning?
- How should important landmarks be delineated?
- How can one compensate for constant movement and shape change by the patient?
These topics are under frequent discussion in many online professional communities and at universities. There is frequent cooperation between industry and academia with some vendors offering university discounts on 3D scanners and software to promote research endeavors.
Helping 3D Scanners To Reach Full Potential
There has been much progress in digitalization technology, but more initiatives are needed to reach full potential. For example, the use of milling machines is a proven technology, but they do not yet allow for work with the smallest details. The goal needs to be to combine the work of milling machines with 3D printers. Currently 3D printers are used to develop 3D objects from digital designs, while 3D scanning digitizes 3D objects. 3D printers are not yet able to make orthoses or prostheses, and instead the 3D scan is uploaded to a CAD program and then made using a milling machine.
There are still limiting factors in the development of digital technologies. For instance, currently only a limited number of specialized scanners for orthopedics is sold each year, which means that they remain a laboratory instrument. In addition, they are not as reliable as they could be and do not receive adequate support. These kinds of scanners, like any opto-electronic device, will only improve when produced in larger quantities. However, portable 3D scanners, which are similar to video cameras in size and shape, are being manufactured in the thousands, resulting in the most up-to-date technology. These scanners capture the 3D model, which can then be used for the customized manufacture of the product needed.
There still needs to be serious investment in the transition to digital technology. Even taking into account that the milling machine doesn’t usually belong to the clinic and that the manufacturing of orthoses / prostheses is done by specialized companies, a clinic will need to invest $40,000 to $60,000 in professional scanners and software. This investment certainly pays off in one to two years, but it is still a significant barrier.
Specialized CAD for orthopedists already exist, but only 30 percent of orthopedists use them. The other 70 percent still prefer to use the common (generalist) engineering CAD. This means that the market for specialized orthopedic CAD isn't fully formed, and the struggle for leadership in this market is at its very beginning. As the market develops, the technology will also advance , which will, in turn, propel adoption.
As digital technology sees greater deployment, the technological, medical, and user and patient values will accelerate. Although the devices are still expensive, the development of new pricing models will aid deployment. For example, manufacturers of scanners and CAD are looking toward a software-as-a-service (SaaS) deployment model, which suggests that a doctor or clinic will pay $60 to $80 per prosthesis / orthosis to a service provider that owns and maintains the scanners and software. Given that the work time of a doctor is reduced by two to three hours, this "deal" should be profitable for the doctors, scanner manufacturers, and CAD developers.
3D scanning and digital technology bring many benefits for practitioners, manufacturers, and patients. The use of a 3D scanner delivers information on the shape of a person within seconds without any safety risk to the person. Unlike X-rays or MRIs, they do not produce any magnetic radiation, and there is no need for special body markers. As the price decreases and technology advances, doctors will increasingly use 3D scanners, and the reluctance by late adopters will disappear. Just as some people still like to read a newspaper, but are slowly moving to e-readers, in a few years it will be natural for the younger generation of doctors to prefer digital technology.