Using Additive Manufacturing To Print Glucose Sensors
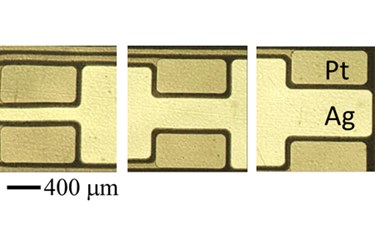
Engineers have developed a technique similar to inkjet printing that hey used to fabricate a new glucose sensor for the management of diabetes. The researchers claim the new system is more precise and efficient, and less costly, than current manufacturing methods and could lead to an artificial pancreas with a single point of bodily entry.
The technology, developed at Oregon State University (OSU) under the supervision of Gregory Herman, uses an electrohydrodynamic jet (e-jet) printer loaded with “ink” made from glucose oxidase, bovine serum albumin, and glutaraldehyde (as a cross-linking agent). The printer deposits the sensor onto a plastic substrate that can be wrapped around a catheter.
In a study published in The Electrochemical Society Journal of Solid State Science and Technology, the researcher team concluded, “the flexible sensor design developed in these studies can ultimately be used within a closed loop artificial pancreas control system thereby reducing the number of components in such a system.”
According to an OSU press release, an artificial pancreas system using this technology would require only one point of bodily entry rather than four, which is common in existing prototypes. Therefore, the new system, researchers say, would be much more comfortable for the patient.
The Juvenile Diabetes Research Foundation (JDRF) estimates that 3.1 million Americans are currently managing type 1 diabetes, and the condition accounts for $14.9 billion in U.S. healthcare costs.
According to Herman, the key to keeping costs down is creating less waste and taking advantage of advanced printing technology.
“The challenges of making these sensors on such thin plastic films were difficult to overcome, but we found that additive manufacturing approaches simplified the process and should lead to much lower costs,” said John Conley, an OSU professor of electrical engineering and co-author of the study.
“These are disposable devices that only last about a week and then need to be replaced," Herman added. "Some other approaches used to make them might waste up to 90 percent of the materials being used, and that’s a problem in a throw-away sensor. It’s also important to keep costs as low as possible and printing systems are inherently low-cost.”
According to the press release, the OSU engineers have already applied for a patent, and Pacific Diabetes Technologies has agreed to oversee commercialization for the product should it be approved for market.
Recent research in diabetic management has yielded a crop of promising artificial pancreas systems, and a recent report from the American Diabetes Association estimated that since 2010, there have been over 40 clinical trials testing different prototypes.
Image credit: Oregon State University