World's First 3D-Printed Titanium Rib Cage Successfully Implanted
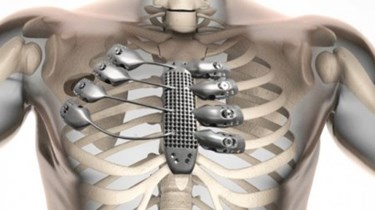
A cancer patient in Spain has been successfully implanted with the world’s first titanium sternum and partial rib cage, specially designed to fit the patient’s body and to meet the unique geometrical and mechanical requirements of a human rib cage. The surgical team who implanted the device believes that this new design approach will pose less risk to the patient and will be less likely to require re-operation over time.
Biocompatible titanium alloys have all the strength of stainless steel but are considerably lighter in weight, less likely to corrode, and offer greater flexibility, which makes them a popular choice for orthopedic implants. However, previous titanium rib and sternum implants have used flat plates and screws that do not integrate organically with the surrounding bones.
“Flat and plate implants rely on screws for rigid fixation that may become loose over time,” explained José Arnada, a member of the Salamanca University Hospital (SUH) surgical team, in a press release. “This can increase the risk of complications and the possibility of reoperation. We wanted to provide a safer option for our patient, and improve their recovery post-surgery.”
For a design that would more closely resemble the natural structure of the human rib cage and ensure a more seamless fit, the SUH team enlisted the help of Australia-based Anatomics. Their design used high-resolution CT images to map exactly how much of the patient’s rib cage had been affected by the chest wall sarcoma, and to recreate the portion to be excised.
Their completed design, described in a YouTube video uploaded by the Commonwealth Scientific and Industrial Research Organization (CSIRO), is a titanium sternum fitted with thin shafts that mimic the curvature of the existing ribs, with sockets on the ends that fit over the remaining bone. Screws drilled through the socket and into the bone hold the implant in place.
Anatomics then took their design to CSIRO’s Lab 22, where the implant was printed with the highly sophisticated Arcam 3D printer, which uses an electron beam to melt and mold titanium powder into the customized shape. Lab 22 recently made headlines when it printed the world’s first titanium heel.
In June, Gizmag reported that Australia was sitting on the second-largest titanium reserve in the world, but the supply would soon be depleted if they continued sending the unrefined metal overseas. Instead, CSIRO has been investing in industrial applications, particularly the biomedical industry, in order to become a world-leader in titanium technology.
Ian Macfarlane, Minister of Industry and Science in Australia, credited the scientists for collaborating on an innovation that crossed disciplines and international borders to address an unmet medical need.
“This breakthrough is an impressive example of what can be achieved when industry and science come together,” said Macfarlane in the press release.
The SUH surgical team published details of their design and surgical methods in The European Journal of Cardio-Thoracic Surgery, and reported that the patient recovered well and was released from the hospital after 12 days.