3D Printed Facial Implant System Cleared By FDA
By Chuck Seegert, Ph.D.
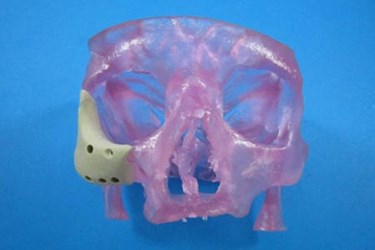
The craniofacial anatomy is highly varied between individuals, and each reconstructive surgery requires a custom implant, which are expensive and difficult to manufacture. Now, however, thanks to 3D printing technology, a lower cost and potentially more customizable implant system will be available to meet these needs.
For hip or knee surgery, a series of general implants can be created to service the needs of a wide range of patients. In craniofacial applications, however, each patient’s anatomy is unique, which prevents the use of general implants. Because of these unique anatomical aspects, custom implants are required to achieve satisfactory craniofacial reconstruction.
Historically, custom craniofacial implants have been machined out of biocompatible plastics — a process that can take many weeks. In addition to being extremely expensive, many of the smaller, intricate features may not be captured due to limitations of the machining process.
Oxford Performance Materials, Inc. (OPM), an advanced materials and additive manufacturing (3D printing) company, recently announced in a press release that it has received 510(k) clearance from the FDA for its 3D printed OsteoFab Patient-Specific Facial Device (OPSFD) — a device that addresses those issues.
"There has been a substantial unmet need in personalized medicine for truly individualized — yet economical — solutions for facial reconstruction, and the FDA’s clearance of OPM’s latest orthopedic implant marks a new era in the standard of care for facial reconstruction,” said Scott DeFelice, CEO and chairman of OPM, in the press release.
When custom implants are machined, increased complexity leads to increased production times. Along with this comes a greater price tag, but OPM’s process is insensitive to these kinds of changes.
“An exciting aspect of our technology is that additional complexity does not increase manufacturing cost, and having both cranial and facial devices cleared now enables us to answer ever more complex cases where upper facial structures can be incorporated with cranial implants as a single device,” said Severine Zygmont, president of OPM Biomedical, in the press release.
Each implant will be manufactured by OPM Biomedical via the company’s proprietary OsteoFab process. The 3D printing process uses a laser sintering approach with OPM’s OXPEKK powder formulation for orthopedic and neurological implants. The OXPEKK implants are biocompatible and have mechanical properties that closely match the bone they will be adjacent to. The adjoining bone may even attach to the implanted device, since the material is osteoconductive.
Biomet, Inc., a leading distributor of advanced technologies for the treatment of arthritis, joint and spine related injuries, and facial reconstruction, will be the exclusive global distributor of OPM’s OPSFD. Biomet is also the exclusive global distributor of OPM’s OsteoFab Patient-Specific Cranial Device, according to the press release.
The potential for 3D printing continues to accelerate, and this innovative, cost-effective, and time-saving technology is now being studied by the FDA as a technology of the future.
Image Credit: OPM