3D Printed Graphene Shows Potential For Tissue Engineering
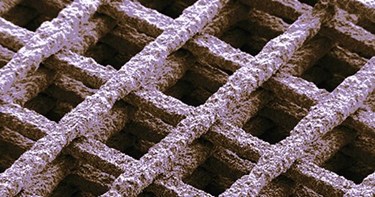
A Northwestern University team has developed a formula for bioink that contains more graphene per volume than had previously been achieved. The graphene-based bioink can be used to 3D print structures for a variety of biomedical applications including biosensors, implants, and even tissue engineering. And, because the formula is between 60 and 70 percent graphene, the structures can take advantage of the material’s robust electrical conductivity, flexibility and strength.
Single-layer graphene is a million times thinner than paper, but research shows that, despite its extraordinary thinness, graphene is 100 times stronger than steel and is an effective conductor of heat and electricity. In the 11 years since graphene’s discovery, researchers have been hard at work incorporating it into the next generation of electronics and medical devices.
“People have tried to print graphene before. But it’s been mostly polymer composite with graphene making up less than 20 percent of the volume,” said Ramille Shah, assistant professor of materials science and engineering at Northwestern's McCormick School of Engineering, in the McCormick News.
At smaller volumes, previously formulated graphene-based bioinks were not able to retain the material’s unique properties, and attempts to add more graphene to the mix often made the printed objects fragile and brittle, Shah said.
To overcome these limitations, Shah’s team adapted previous research, used to develop 3-D printable hydrogels, and was able to develop a bioink that was over 60 percent graphene and strong enough to print larger structures.
The key to their success was mixing graphene nano-flakes with the biocompatible elastomer polylactide-co-glycolide (PLGA), and solvents that quickly evaporated during the printing process. Once the solvents evaporated, the structure solidified immediately and held its shape.
“The presence of the other solvents and the interaction with the specific polymer binder chosen also has a significant contribution to its resulting flexibility and properties. Because it holds its shape, we are able to build larger, well-defined objects,” Shah said.
Authors of a study published in ACS Nano reported that the printed structures were “mechanically robust and flexible while retaining electrical conductivities greater than 800 S/m, an order of magnitude increase over previously reported 3D-printed carbon materials.”
Further experiments showed that 3D printed graphene could serve as a substrate for stem cell growth, viability, proliferation and neurogenic differentiation, without the addition of growth factors or signaling that are common in tissue engineering.
By using one material, alone, without the addition of other more expensive and complex agents, researchers could print tissue more easily and more cost-effectively, Shah told McCormick News.
Tissue engineering is a rapidly growing global market, and 3D printing offers a fast and efficient way to build scaffolding specific to each patient’s needs. Recently, a team of scientists in Michigan 3D printed a cellulose nanocrystal substrate and demonstrated its potential for growing nerve cells.
“There are many different tissue types, so we need many types of inks,” said Shah. “We’ve expanded that biomaterial tool box to be able to optimize more mimetic engineered tissue constructs using 3D printing.”