3D Printed Hydrogels With Cartilage-Like Toughness
By Chuck Seegert, Ph.D.
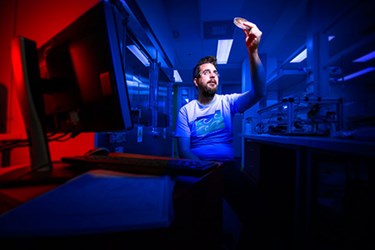
Replicating the robust performance characteristics of cartilage has proven elusive to tissue engineers. Researchers at the University of Wollongong in Australia may have come close, however, with the development of hydrogel materials that are both strong and easy-to-manufacture.
Hydrogels are polymer materials that when hydrated are composed mostly of water, like many soft tissues. These polymers are soft and more amenable to surrounding tissues than hard materials when implanted. Unfortunately, synthetic hydrogels do not possess the mechanical strength required to bear physiologic loads that natural hydrogels, like cartilage, can.
By taking a novel approach, University of Wollongong (UOW) researchers have found a way to improve the properties of hydrogels, according to a recent press release. They did this with a 3D printing process that uses two different polymer materials as inks. Hydrogels form the body of each device, but the body is also reinforced by stiffer fibers, forming a classic composite structure.
“The printed fibres give strength to the hydrogel in the same way fibre glass gives strength to a surfboard,” said Shannon Bakarich, a Ph.D. candidate at UOW, in the press release.
Shannon’s research study was published in ACS Applied Materials and Interfaces. Both alginate hydrogel and an epoxy adhesive for the fibers were laid down simultaneously in a single step. By varying the quantity and spatial distribution of the two materials, he was able to develop a series of materials with various swelling behaviors and mechanical properties. The prototypes ranged from soft and wet to hard and dry.
“Using computer aided design software, I can make a digital model of the fibres and hydrogel matrix, tuning the mechanical properties by carefully controlling the distribution of the fibres within our structures,” Bakarich said in the press release.
A prototype meniscus was created using the new process, according to the study. This prototype illustrates the ability to make custom 3D objects with properties that can be tailored to specific applications.
3D printing continues to gain momentum as a method for implantable devices. Recently the FDA announced the clearance of a facial implant system that is manufactured via 3D printing. Additive manufacturing is also being looked at as a method of fabricating implants that release bioactive agents or drugs.
Image Credit: University of Wollongong