Putting It All Together: Lean Daily Management
By Darren Dolcemascolo, senior partner and co-founder, EMS Consulting Group
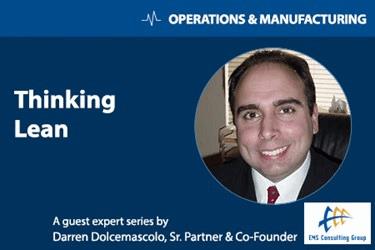
In the last several editions of Thinking Lean, we introduced tools and methods to support continuous flow and pull systems. We are shifting gears in this article to discuss Lean Daily Management. Daily Management is a key methodology for making lean thinking part of daily work, rather than thinking of it as a special project or add-on to “normal” work.
In 2015, when the Thinking Lean series began, we discussed A3 problem-solving and walked through the general lean problem-solving process, which follows the PDCA cycle. In this article, I would like to lay out the glue that holds all of the concepts together including the problem-solving process and tools we have discussed in past articles.
A Lean Daily Management process accomplishes the following:
- Ensures that the people, materials, and processes are flowing according to standard work.
- Identifies problems/abnormalities, top contributing causes, and countermeasures.
- Monitors performance and sustains results.
Daily Management can be accomplished in a number of ways, but visual management is key. The following elements usually are included:
- Performance-Tracking Board (pictured below) — A performance-tracking board covers broad areas of focus based on the Toyota Production System, and usually includes Quality, Safety, Delivery, and Cost. The board typically includes daily and monthly tracking of results of Key Process Indicators (KPIs). The daily charts are updated each day, and typically include one month of data. The monthly charts record trends month-to-month over the year. All charts include a goal or target, and when the target is missed (for example, if a daily production output goal is not met), team members track the reasons on a pareto chart. This helps to identify the vital causes that must be addressed. The countermeasures are identified and tracked on an action item list, sometimes called a kaizen newspaper.
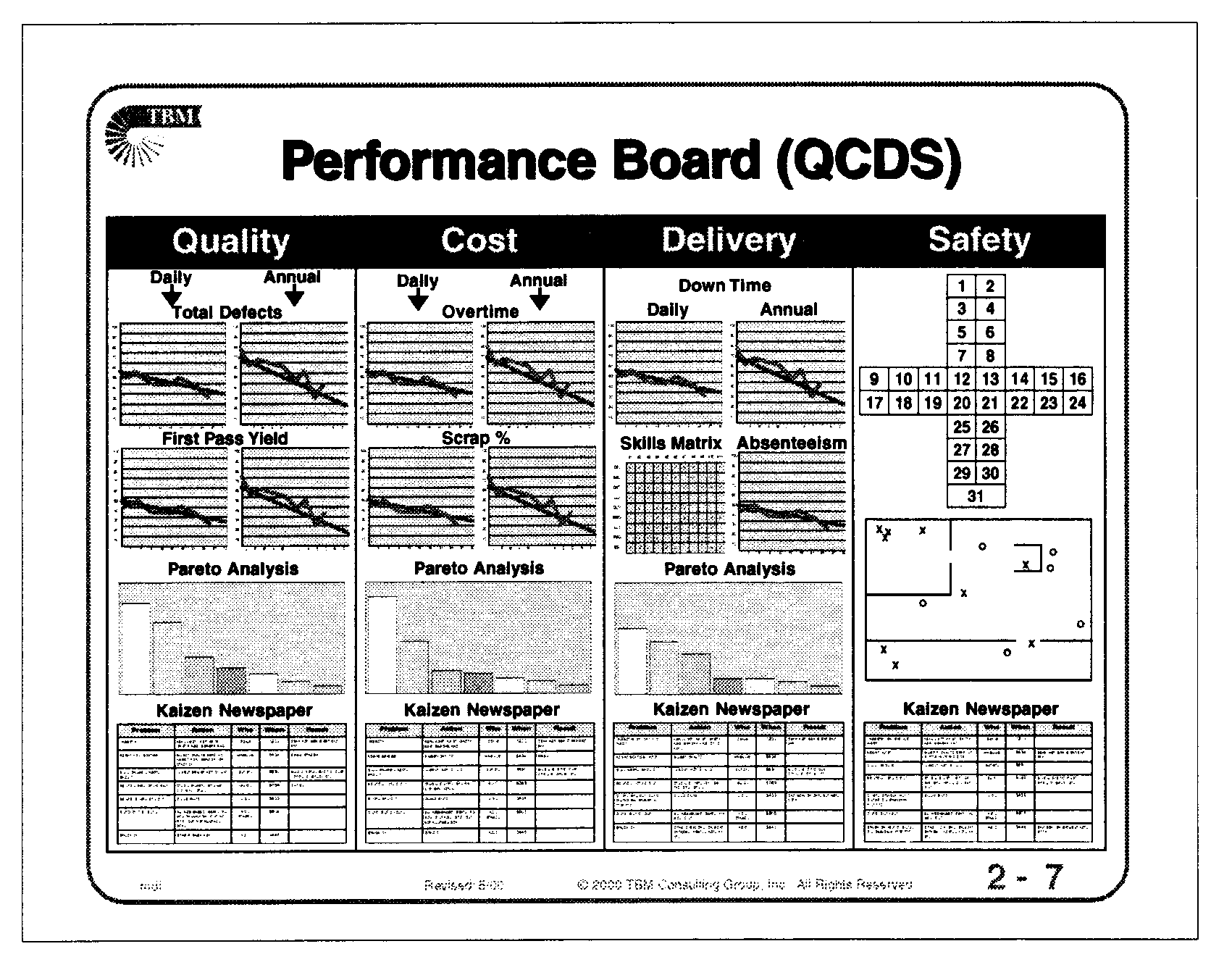
- Process Control Board — Another key element of daily management is tracking within the production areas or cells themselves, accomplished on a process control board. Hourly tracking of performance and identification of issues (such as defects), as well as quality performance tracking, are part of this task. For example, we might include a day-by-the-hour chart (planned versus actual production chart), as seen below. This allows us to identify the top causes for our performance tracking board.
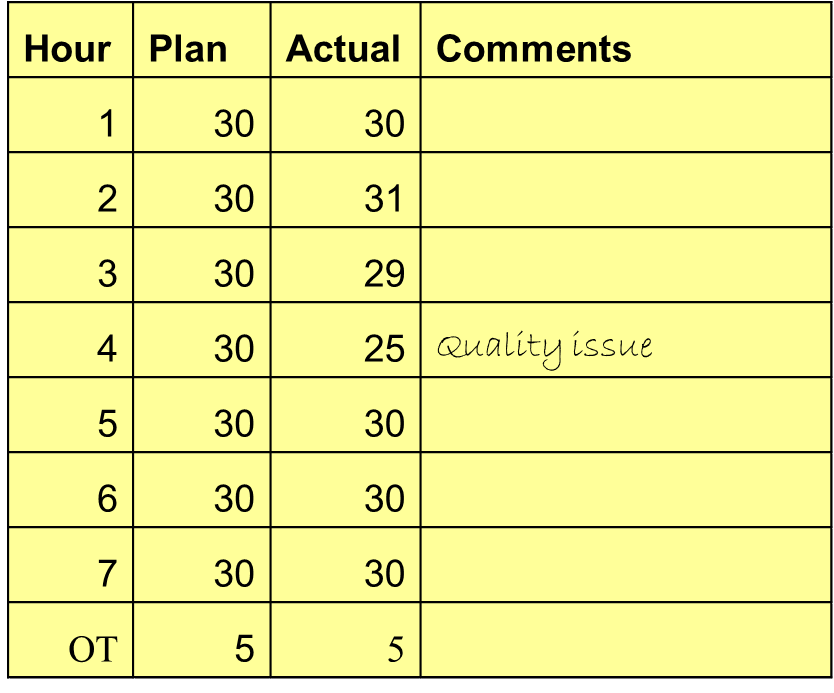
- Kaizen / Idea Board. Visual management needs to include a method for employees to identify problems, causes, and ideas for improvement. Rather than having a suggestion box, which encourages the wrong kinds of suggestions and results in frustration, we recommend a visual system for capturing ideas. Below is an example of this type of system.
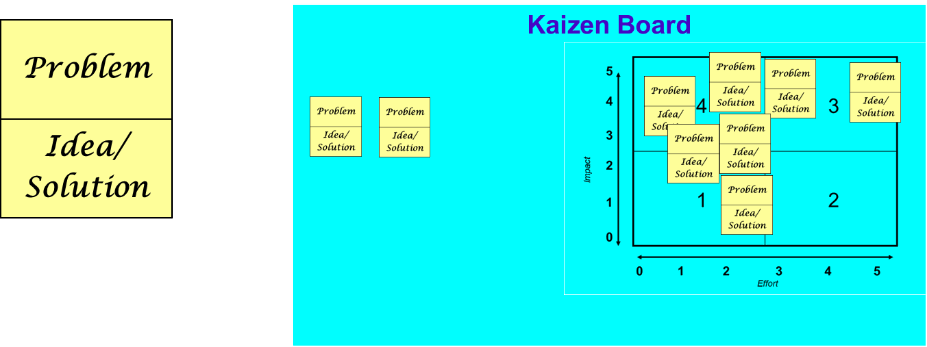
Employees identify problems, potential causes, and potential ideas for solution. The ideas are discussed daily or weekly at stand-up meetings (huddles) around the visual boards, and then are tracked utilizing an Impact-Effort Matrix (PICK Chart). Ideas then move from the PICK chart to implementation based on resourcing and prioritization. PICK Charts include the following four quadrants:
- Possible: Low Effort, Low Impact
- Implement: Low Effort, High Impact (highest priority)
- Challenge: High Effort, High Impact
- Kill: High Effort, Low Impact
Other visuals that might be included in the overall visual management system are:’
- Skills Matrix — This is a visual representation of each team member’s training and level of skill. It can be used for managing/scheduling, as well as to encourage growth and development by creating individualized development plans.
- Standard Work Charts and Standard Work Auditing — Standard work should be audited daily by various levels of management to identify gaps and opportunities for improvement. The purpose is not to blame those who might not be following the standard work, but to find out why.
- 5S and/or TPM Audits — The results of 5S and TPM audits, along with improvement plans, can be included on the visual management boards.
- Current A3 Problem-Solving Effort — An A3 currently being addressed by the team might also be included on the visual management board for discussion.
Creating the boards is only the beginning. I have seen many well-intentioned organizations create tracking centers that do not drive actual improvement activity.
In order to drive improvement, the tracking boards need to become the basis for daily huddles. At these meetings, the area team members discuss each of key element of the boards, with emphasis on the areas that are ”red,” meaning that the goal or target has not been met. This allows the team to adjust in real time, rather than waiting until the end of the month to discover that goals have not been met.
The boards also are used during gemba walks. Gemba is a Japanese word that translates to “the actual place.” It is best understood as “where the work happens.” A gemba walk is intended for managers to “go and see” the status and obtain the pulse of the operations, as well as the improvement efforts. By walking out to the boards and talking with the front-line supervision, managers can learn whether goals are being met, and what specifically is being done to address the gaps. This brings the lean problem-solving process and tools into daily work, which is exactly the condition medical device manufacturers and all lean-thinking companies need to be lean for the long term.