Adhesive Helps Wheelchair Manufacturer Keep it All Together
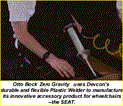
Provided good adhesion as well as durability and flexibility
Finding the Right Adhesive
Developing the Solution
Improving the Production Process
Oftentimes the integrity of a medical device depends on the integrity of the adhesive used to bond its components. If the bonds fail, then the product certainly can't function as it was intended. Such product failures can lead to injury or even death, so it's not surprising that manufacturers consider adhesives to be one of the most critical components of a device.
One company that understands the importance of choosing the right adhesive is Otto Bock Zero Gravity Medical (Draper, UT), a wholly-owned subsidiary of Otto Bock Orthopedic Industry. Zero Gravity is the first company to manufacture wheelchairs and accessories using the innovative thermoplastic injection molding technology.
According to Ted Andersen, production manager, "Thermoplastic technology has allowed us to design products with improved features and added benefits for our customers. By using this technology, we can guarantee the functionality of every part on the wheelchair."
Although the new technology had been successful in other areas, the technicians at Zero Gravity conducted numerous tests before they started production of the wheelchairs and accessories.
The new technology uses a polyurethane as opposed to the traditional nylon thermoplastic base. Zero Gravity needed to find a product that would adhere to the polyurethane base as well as provide strength and durability.
"It was imperative that the product not only provide great adhesion but also durability and flexibility," says Andersen. "Finding a product with both characteristics was not an easy task."
After investigating several adhesive manufacturers, Zero Gravity turned to Devcon (Danvers, MA), a manufacturer of maintenance, repair, and adhesive bonding technology.
Devcon worked with Zero Gravity to develop a solution that would be used in the production of its accessory product, the SEAT. The product is designed to provide superior support and flexibility. It can be used with Zero Gravity's wheelchairs as well as most other wheelchairs on the market. The products are structural components of the wheelchair and must be durable and adjustable.
With the help of Devcon, Zero Gravity found the solution they were looking for. Devcon recommended Plastic Welder, a tough structural adhesive that is specially formulated to bond to dissimilar substrates and to provide high shear strength.

According to Andersen, "Plastic Welder provides the strength and durability we require. It is easy to use and offers a fast cure time."
Zero Gravity uses the Plastic Welder to bond critical components to their products. These components are essential for attaching the SEAT to the wheelchairs.
Andersen adds, "The components are designed to allow the products to be highly adjustable. Because the products are adjustable, the adhesive material must provide tremendous strength and flexibility. We found these traits with Devcon's Plastic Welder."
Improving the Production Process
Along with the Plastic Welder's durability and strength, its cure time was also an important characteristic to Zero Gravity. "The product's fast cure time has greatly enhanced the production process. In fact, we can produce twice as many products with the Devcon solution," Andersen says. "We can complete each step in half the time, because we're not waiting for the material to dry before moving on to the next process. The product's cure time is critical," he adds.
In the future, Zero Gravity plans to work with Devcon to develop a special formula of Plastic Welder to use throughout manufacture of the wheelchair. According to Andersen, "By using Plastic Welder in the manufacture of the chairs, we will be able to reduce labor time and improve the aesthetics of the chair."
"Not only have we been able to save time and money, but also we have been able to produce a better product," Anderson concludes. "We plan to have a long relationship with Devcon. They have met and exceeded all of our expectations."
Devcon Corp., 30 Endicott St., Danvers, MA 01923. Tel: (978) 777-1100; Fax (978) 774-0516.