FEATURED EDITORIAL
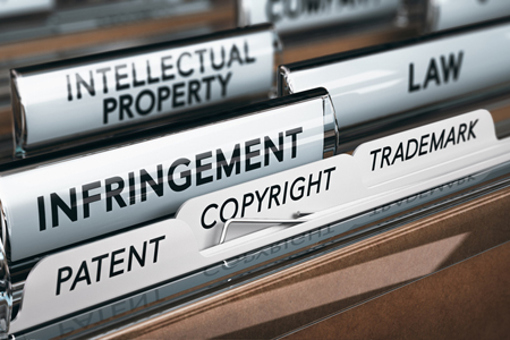
As the medical device industry continues to expand, intellectual property (IP) considerations — especially those concerning patents — are critical for medical device innovators and manufacturers.
-
There’s a distinct need to create wearables that interweave seamlessly into an individual’s lifestyle, encouraging adherence and gathering long-term, accurate diagnostic data.
-
Brazil is experiencing a regulatory revolution that is fundamentally transforming its medical device clinical trial landscape.
-
Process validation is often viewed as a costly regulatory formality. However, it is actually a strategic investment that, when integrated into business planning, delivers measurable outcomes in productivity, compliance, speed-to-market, and profitability.
INDUSTRY INSIGHTS
-
Your Guide To Selecting Safety Capacitors For EMI Filtering In The PFC Stage Of An AC/DC Converter
Selecting the right safety capacitor requires careful analysis of EMI data, voltage levels, circuit configuration, performance specs, certifications, and real-world testing for effective PFC filtering.
Thermoplastics revolutionized medical technology by replacing glass with flexible PVC. Learn how their versatility supports advanced healthcare applications, from wound care to life-saving devices.
Discover how medical device manufacturers are leveraging advanced techniques like thermoforming and dip molding to create customizable low-pressure balloons that enhance reliability and compliance.
Enhancing catheter visibility under fluoroscopy, custom radiopaque filler blends improve imaging clarity without compromising polymer strength. Learn how this is crucial for accurate device placement.
Thin film extrusion technologies are transforming medical device innovation by enabling flexible and durable components. Discover how you can meet growing demands for advanced healthcare solutions.
MED DEVICE ONLINE CONTENT COLLECTIONS
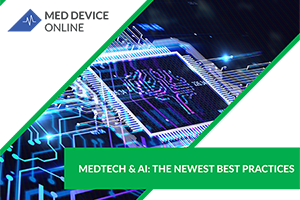
Artificial Intelligence and Machine Learning are taking the life sciences world by storm. Do you know how to harness its power for your medical device? Check out our latest e-book which examines the opportunities AI and ML offer to both complement and supplement human intelligence in the medical device industry.
More Content CollectionsLATEST HEADLINES
- Cutting-Edge Innovation Steals Spotlight On London Biotechnology Show 2025 Exhibition Floor
- How Micro Molding At Accumold Is Driving Sustainability From The Inside Out
- Accumold Harnesses AI To Empower People, Enhance Precision, And Strengthen Customer Partnerships
- Discover Medbio's Medical Molding Expertise At MD&M East
- Knowles Extends Custom Miniaturization Capabilities To MedTech OEMs
- Visit Medbio At MD&M West In Anaheim, CA
- Accumold Brings Micro-Optics Expertise To Photonics West 2025
- Nordson MEDICAL, Boyle Receives MedAccred Accreditation