An Introduction To Lean For Medical Device Manufacturers
By Darren Dolcemascolo, senior partner and co-founder, EMS Consulting Group
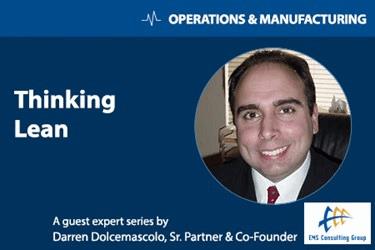
This is the first in a series of articles on the ways medical device manufacturers can transform their operations — and gain a competitive advantage in the market — by implementing lean strategies.
Lean manufacturing is the term most commonly used to describe the Toyota Production System (TPS). In 1990, a book called The Machine that Changed the World, written by James Womack, Daniel Jones, and Daniel Roos, introduced the world to the term “lean production.” This term was used to contrast Toyota’s system to other global auto producers. Toyota was able to build cars faster and with better quality. It took fewer hours to assemble one of their cars, and Toyota was able to develop their products much faster than the competition. Since then, the lean philosophy has been adopted in varying degrees by companies in many industries.
The figure below is a Toyota Production System (TPS) house diagram. The foundation is operational stability, which means creating consistency in methods and tasks, equipment, workplace organization, and output of work. There are two pillars that support the goals. The pillar on the left, Just In Time, is about providing the next downstream customer with what they need when they need it and in the right quantity. Quality at the Source (also known as Built in Quality), the second pillar, essentially is the idea of never knowingly passing defective product or information to the next downstream customer.
These concepts, combined with respect for people and a culture of continuous improvement, lead to the best quality, lowest cost, and shortest-lead-time products and services. In this article, I will talk about the framework for lean manufacturing and why it is particularly useful to those in the medical device industry.
An Introduction To Lean
Lean manufacturing includes a set of principles that lean thinkers use to achieve improvements in productivity, quality, and lead-time by eliminating waste through kaizen. Kaizen is a Japanese word that essentially means "change for the better" or "good change." Using a problem-solving process at every level of an organization, everyone works toward the goals identified by the organization. This means working toward providing the customer with a defect-free product or service when it is needed and in the right quantity.
The problem-solving process for lean involves:
- Problem description and definition
- Root cause analysis
- Countermeasures
- Implementation plan
- Results
- Follow up and future steps
This problem-solving process is the means by which executives identify goals and high-level plans to reach those goals. It also the means by which supervisors and engineers work with front-line personnel to improve processes. A problem is defined as the gap between the current condition and the target condition or standard. It is everyone’s job to solve problems by identifying problems, identifying the critical causes, and identifying and implementing countermeasures.
As lean organizations work to improve processes, they identify and eliminate waste and sources of waste. Wastes are activities that consume resources but do not add value in the eyes of the customer. Taichi Ohno, former Toyota chief engineer, identified seven wastes of manufacturing:
- Overproduction
- Transportation
- Unnecessary inventory
- Inappropriate processing
- Waiting
- Excess motion
- Defects
Applying Lean In Medical Device Companies
Within the medical device industry, an organization can use lean strategies to develop a competitive advantage in the following ways:
- It can use lean strategies for developing products faster. Most people think of lean as a manufacturing methodology only. However, it was also Toyota’s lean product development process that provided it with an advantage in the automobile market. This same thinking can provide medical device companies with the ability to beat its competitors to market with products that better meet the needs of its customers.
- It can utilize lean strategies for faster delivery times within its operations. If a medical device manufacturer can shorten its internal production lead times, two key benefits will result: 1) Without the need for excessive inventory, a company can invest more money into development or into acquisitions. 2) It can be much more agile in responding to customer needs by offering a wider variety of products and even the possibility of mass customization.
- Lean strategies can help a medical device company’s supply chain. Most medical device companies are not vertically integrated, but lean supply chain methodologies can be used to shorten supply chain lead times and ensure better quality. Rather than taking the traditional role of an adversary, lean organizations treat their suppliers as an extension of their companies. They do this by challenging them and providing them with assistance through lean supplier development programs.
- It can utilize lean strategies to develop a more reliable, higher-quality product. While most people don’t associate lean with quality, this is a misunderstanding. Lean is about improving quality as well as delivery/lead-time and cost. By creating a problem-solving mentality within an organization and developing strategies for improving product quality, an organization can produce high-quality products without the cost of added inspection. Instead of increasing the number of inspection stations, a lean medical device manufacturer would utilize true root cause analysis problem-solving to eliminate the causes of defects.
In summary, lean strategies enable companies to develop and deliver high-quality products and services faster and with less waste. Lean thinking can be effective in any industry. For the medical device field in particular, it can provide significant competitive advantages in the areas of development, production, and supply chain.
About The Author
Darren Dolcemascolo is an internationally recognized lecturer, author, and consultant. As senior partner and co-founder of EMS Consulting Group, he specializes in the application of lean strategies in medical device, biotech, healthcare, manufacturing, and technology environments. Some of the clients for whom he has worked include Covidien, Edwards Lifesciences, Hologic, and Zimmer. In addition to working directly with clients, Dolcemascolo teaches lean workshops and certification programs in Southern California. He has a BS in industrial engineering from Columbia University and an MBA from San Diego State University.