Can Drug Device Manufacturers Achieve Operational Excellence Through A Digital Facility?
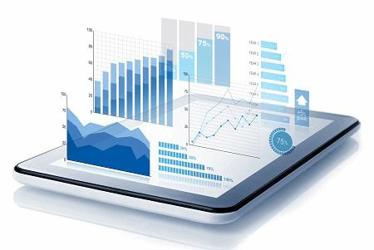
By Mark McElfresh, West Contract Manufacturing
Today’s technology, particularly smartphones, has changed both the way we receive data and the way we communicate. In what is referred to as the Internet of Things (IoT), this instantaneous procurement of data makes life simpler and allows people to connect in ways that used to be impossible. In manufacturing, the connectivity between equipment, devices, and people via sensors offers the same ability to gather data faster and easier. However, instead of receiving the latest news or being notified of someone’s birthday, the information gathered in a manufacturing environment equips a facility with the tools to react to issues in real time and respond more quickly to customer requests. This fundamental shift in how manufacturers can react to manufacturing issues offers tremendous value to operations, and in the drug delivery device industry, provides patients with safe and effective medical devices.
Transform Reactive Manufacturing
In a traditional manufacturing environment, processes are monitored periodically with samples collected every one to three hours. Data is then analyzed and decisions on product quality are made, and inspections for faulty products are completed at the end of the day. Unfortunately, this method does not provide any visibility into what is happening between these sample periods. While this traditional approach has been relied upon for years, efficiency, productivity, and quality can all be improved through the implementation of a digital facility.
For example, a drug device manufacturing facility running hundreds of injection molding machines at multiple facilities can be monitored through sensors 24 hours a day, 7 days a week. With every cycle run, numerous data points are collected and analyzed in a manufacturing execution system (MES), which collects and reports production status i.e., amount of scrap, actual parts produced, productivity. If there are any unanticipated variations in the machine or processes that indicate potential issues, the parts from that cycle are discarded. If a machine experiences multiple cycles with unanticipated variations, it shuts itself down and sends a text or a PA announcement to the associates on the plant floor. By catching problems early and preventing product defects, resources are not wasted investigating why a product does not pass inspection. Reaction time to production issues is then reduced from hours and days to just minutes.
By using the connectivity of the sensors on all of the machines, product sampling is still completed, but now manufacturers can see what is happening with every cycle.
Drive Supply Chain Accountability
In every industry, customers have specific expectations. Many of these expectations are being driven by the ability to order exactly what a customer wants, such as through online shopping, and to receive those orders quickly and correctly. This certainly applies to drug device manufacturing as well. With a digital facility, there is a much higher degree of certainty that what is delivered to customers is right the first time.
In addition, the use of machine sensors also offers manufacturers the capability to adjust to changing demands and schedules more easily. The machine sensors feed data to the MES, which is rolled into an overall enterprise resources planning (ERP) system, so production planners can dynamically adjust production schedules to maximize uptime. The result is shorter lead times and higher on-time, in-full delivery percentages. This connectivity from machine to ERP also allows a quicker and more accurate response to changes in demand the client is receiving from its customers.
Empower And Engage Employees
The machine-to-machine communication of the IoT offers multiple benefits and possibilities. However, new technology can also present challenges, especially to employees who are used to working in a traditional manufacturing environment. This is a challenge manufacturers in a digital facility may face, as installing sensors does not change manufacturing in relation to people. Employees on the plant floor are still ultimately the ones who determine the quality and efficiency of the product. Therefore, a manufacturer must keep pace by training its employees on any new system.
With the implementation of sensors, employees are no longer tasked with the mundane job of writing down numbers every hour on paper and entering them into a computer. The connectivity of the devices via the sensors gives employees the time to analyze data and make important decisions about product quality. A popular approach to improving quality through the analysis of data is the method introduced by Bill Smith while working at Motorola in 1986— Six Sigma. On GE’s site, it explains that “the central idea behind Six Sigma is that if you can measure how many ‘defects’ you have in a process, you can systematically figure out how to eliminate them and get as close to ‘zero defects’ as possible.” By implementing this approach in a digital facility, employees not only have access to extensive data, but they also know how to use it to improve operations.
Nonetheless, the power of data is only as effective as the processes behind it. Updates will need to be made to a company’s business processes and procedures to provide the framework around the decisions its employees can and cannot make. Key stakeholders should be brought in to create standardized business processes that are documented and shared across multiple sites. Training is then required to properly execute any changes. Once this is accomplished, there is potential for employee engagement to increase because new ideas that have been demonstrated and proven can be shared across the company. This gives employees the recognition that they can improve the way they do their jobs and hopefully motivates them to offer more solutions.
Conclusion
According to a new report from the research firm Gartner, Inc., IoT devices will encompass more than 20 billion connected objects by 2020. This digital boom that is changing the way data is collected and used across the world is coming to manufacturing. Drug device manufacturers have a choice of either sitting back and doing nothing or joining the journey to operational excellence. While the ultimate goal of a digital facility is to improve operations, the benefits it offers to patient safety are the undeniable reward.