Continuous Microbial Air Monitoring In Clean Room Environments
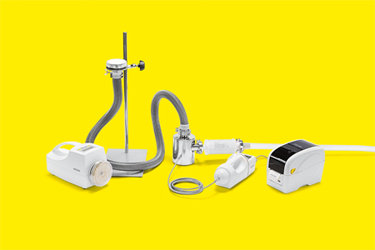
Environmental monitoring is an important part of quality assurance for the production environments of sterile pharmaceutical products. Especially for aseptic filling lines where products are filled without a terminal sterilization step, it is of utmost importance for product safety and thus an essential part of the quality control strategy. Such ISO 5 graded manufacturing environments are required to have < 1 colony-forming unit (CFU) per m³ of air.
A typical method for monitoring contamination of air is to actively draw air and filter it through special gelatin filters.
According to Annex 1 to the EU GMP guide, a minimum sample volume of 1 m³ of air should be taken per sample location. Considering, an 8 hours work shift 1 m3 is a too low sample volume to reliably judge the air quality of the manufacturing environment. One approach to improve product safety would be the implementation of a continuous air monitoring covering the complete production process (at multiple sampling points).
Unlike agar plates, which would dry out during long-term sampling, the Gelatin membrane filters can be used for the whole 8 h period. Human intervention, such as change of agar plates, could then be avoided, thus lowering the risk of secondary contaminations to nearly zero.
Explore results from a study aimed to establish whether a continuous sampling (and multisampling point assay) provides effective monitoring for the entire production process (8 h) by determining whether trapped organisms can withstand long-term drying stress with unaltered recovery.
Get unlimited access to:
Enter your credentials below to log in. Not yet a member of Med Device Online? Subscribe today.