Creating A Custom Spring Assembly For Medical Devices
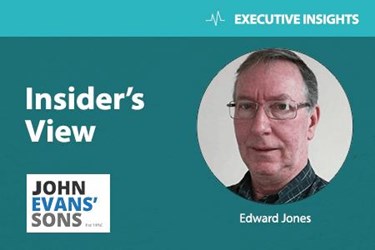
By Edward Jones, John Evans’ Sons
Technological advances in medical devices seem to be an everyday occurrence. As the industry continues to rapidly grow, these evolving devices will require distinct products that may or may not already exist, particularly as more devices require miniaturized components to achieve precision and accuracy.
Additionally, each component in the device needs to meet strict quality and safety standards. One often-overlooked piece of this complex puzzle is springs, whose mechanical function supports much of the innovation in the medical device industry — even as more products depend upon digital features.
For example, how can an OEM be confident that a spring’s estimated wire diameter will produce the optimal force for an auto injector to function smoothly, without too much force or the risk of incomplete drug delivery? Springs are integrated into device design for motion control and counterbalancing purposes, to assist or enhance articulated instruments. Constant force, spiral torsion, power, extension, and torsion springs are some of the most commonly used springs in medical devices. Your device may require many types of spring to complete an action, especially if there isn’t an existing spring specifically designed and produced for that function.
In such cases, a spring manufacturer with a knowledgeable design and engineering department can help you determine whether a spring sub-assembly is necessary. Here’s why you should consider a custom spring assembly when talking with your manufacturer.
Experimentation
Experimentation is crucial to a medical device developer. Such experimentation may lead engineers and developers to learn that the spring requires additional components.
It is much easier and more efficient to experiment with your spring manufacturer. Almost any project requires changes to critical components like motors and springs that are necessary to achieve optimal performance. It is much harder to test your product with a spring manufacturer if they don’t have the experience with developing custom spring assemblies.
Maintain open communication throughout the design and development process. Bring a spring manufacturer on board as early as possible so they can offer their insight.
Customization
Customization is an obvious, but important, benefit of an assembly. A manufacturer with component assembly capabilities can use a variety of materials such as machined metal, plastic, rubber, etc. This is especially great for medical devices, where a truly unique assembly is required.
Additionally, a quality spring manufacturer should be able to use your designated or supplied parts to create the sub-assembly. This is ideal when you might have a proprietary device that requires especially unique components.
Alternatively, your manufacturer likely has existing springs and other components on hand. Again, these materials can be used to create a custom assembly.
Cost And Lead Time
A medical device requires detailed precision. One of the major challenges facing the medtech industry is prolonged development phase, which is often a result of not having the right materials or components.
The longer it takes to get something on the market, the more stress it causes. A spring is a relatively inexpensive component, but failing to consider an assembly at the time of manufacturing can have costly effects.
If you create a spring without considering an assembly early in the design process, you may end up with a spring that’s the wrong size or unable to handle stress loads, for example. It is possible that your device needs a sub assembly or other components that simply do not already exist. It is best to know this sooner rather than later so you can design and manufacture the spring with an assembly in mind.
A knowledgeable manufacturer will be able to assess early enough when an assembly or sub-assembly is required for your spring before it is needed for a larger system. It is more cost-effective for manufacturers to consider this at the spring manufacturing stage rather than after. If you partner with a manufacturer who can design and produce a spring and an assembly, you’ll have a better chance to correct problems or adjust specifications in the early stages of product development.
Medical device manufacturing presents unique challenges; however, the opportunities for innovation are greatest through a multi-industry approach. Rely on your spring manufacturer to help you come up with a unique, competitive product that you can modify and build upon. To truly get a product that is durable and precise, choose a spring manufacturer that understands the medical device industry. Their knowledge and credibility will be imperative to achieve your desired product.
About The Author
Edward Jones is Marketing Manager of John Evans’ Sons. His 27 years with the company has included product development, industrial process implementation and software systems integration. Prior to that, he worked in prototype electronics development for the B-1 Bomber project, the space shuttle Columbia, and the Tomahawk cruise missile. When away from the office, he enjoys off-shore big game fishing, competitive road-racing and photography. You may contact him at ed.jones@springcompany.com