HACCP Inspectional Approach: Should the Industry Be Accepting?
Well, leave it to FDA to come up with a new approach for inspecting medical device manufacturers (new to the medical device industry, that is). The HACCP inspectional approach was initially instituted by FDA for the food industry in the early 1970s. Most recently, FDA adopted this approach for the seafood industry, making it a regulation similar to the GMPs. This was done to provide some assurance for a safe supply of seafood products.
So why is FDA now looking to implement a food-industry policy for the medical device industry? If I am correct, these industries have nothing in common. But, as you will see, the use of the HACCP approach could easily be applied to the manufacture of medical devices.
FDA has been looking into the use of this inspectional approach for the medical device industry for over two years now. To do this, the agency has been trying to get volunteer companies to implement the HACCP principals and then work with these companies by inspecting their HACCP plan. At this time, four companies have presented completed plans to the agency for review. FDA also reported that there are several other companies that have implemented the plan, but they have decided not to be part of the study and share data with the agency at this time. The size of companies who have submitted plans range from 12 to 2000 employees. But over 800 people have attended the 30 HACCP courses that the agency has given thus far.
Before going into the reasons behind FDA's evaluation of this inspectional approach, having an understanding of HACCP would be appropriate.
What is HACCP?
HACCP is an acronym for Hazard Analysis and Critical Control Points. When used properly, the HACCP approach of evaluating your medical products and the production processes could provide you some assurance that you have determined the hazards associated with the device and its processes. It also shows that you have determined the critical control points and that you are able to control them.
HACCP is a preventive, not a reactive, management tool used to assure that the manufacturing process addresses all potential hazards of the device. HACCP is not a zero-risk system but is designed to minimize the risk of potential hazards.
There are seven principles to HACCP:
- Identify critical control points (CCP) in the process.
- Establish critical limits for preventive measures associated with each CCP identified.
- Monitor each CCP. (Establish procedures for using monitoring results to adjust the process and maintain control.)
- Establish corrective actions to be taken when a critical limit deviation occurs.
- Establish a record-keeping system.
- Establish verification procedures that the HACCP system is working correctly.
Applying These Principles to the Device Industry
The basic use of this approach is to evaluate each step of your manufacturing processfrom your receipt of components through product distributionand to determine if that process poses a potential hazard to the finished device related to any one of these three areas: biological, chemical, or physical.
The HACCP guidewhich was written for the seafood industry but is presently being applied to the medical device industryhas forms used to perform the Hazard Analysis. Once you have determined your Critical Control Points (CCPs), you then use the HACCP plan form to look at each CCP, come up with the Critical Limits for each preventive measure, outline "What – How – Frequency and Who" will monitor these CCPs, define your Corrective Actions in the event that the Critical Limits are deviated from, how the information will be recorded, and, finally, how the CCP will be verified.
If you think about it, any good medical device manufacturer has already performed this exercise in some form.
When this program was starting out, FDA's HACCP training for the medical industry required device company representatives to attend a seafood HACCP course and try to apply HACCP to their products and processes. It was an interesting session. With several companies successfully being part of this program, FDA has now set up HACCP training courses directed towards the medical device industry.
During the course, participants conduct a Hazard Analysis and outline a HACCP plan. One example used was a manufacturer of low-protein, nonsterile, latex examination gloves. Once the plan was completed, it was determined that there were only three CCPs for this operation. One could surmise from this exercise that if a company that made this type of gloves and if the operations were already in GMP compliance, it would not change the operations or record-keeping system.
The Cons
So what are the drawbacks to this system? If you decide to use this system, it would provide FDA with a clear detailed map of your operation's Critical Control Points. It would also pinpoint what your company was doing to assure that these points were being monitored and what would be done in the event that these points were deviated from. This may not sound too different from what the new GMPs require, but more requirements may not sound too appealing.
Whether that could be considered good or bad will have to be determined by each company.
Basically, FDA feels that if a company were to use this approach of conducting a Hazard Analysis and come up with a HACCP plan on how they will control their Critical Control Points, then FDA will key in on these points during future inspections. When the FDA investigator feels that the company is controlling these critical areas, the inspection will be over. If done correctly and FDA sticks to this policy of reviewing the CCPs only, the inspectional time at the facilities could be reduced by more than half. That is the main reason for FDA to look into this approach: to reduce the inspectional time and thus be able to use their staff more efficiently.
One has to remember that this system is not a stand-alone system. In order to assure its success, HACCP must be built on a strong Quality System Regulation program. If violations are found, FDA will fall back on the QSR to take action. There is no regulatory requirement to use the HACCP approach. But the main reason for this approach is that it will be used by the agency to focus their attention on the parts of the process that are most likely to affect the safety of the product. By being allowed to do this, FDA would be able to forego all the unnecessary learning process involved with each inspection and key into the plan that would be supplied by the company.
Many questions were brought up by the medical device company representatives attending the courses. Some of the more pertinent ones were:
- What is a Critical Control Point for a medical device?
- What would be the difference between a CCP and a Control Point?
- What would be the value to the company?
- Will HACCP be accepted by the EU now that many of the medical device companies are also ISO certified?
- Will the GMPs be put aside during a HACCP inspection, and if we take this approach, how would we be sure that it would be followed by the agency?
- In that HACCP is safety-related only, will FDA inspect our changes for intended use also?
- Will complaints still be reviewed?
- Will the Hazard Analysis worksheet have to be shown to FDA?
- Will a CCP disagreement with the agency result in an FDA 483 point?
- Will this approach be mandatory or voluntary?
- How costly will it be to set up the HACCP plan?
- Does the plan work to assure device safety?
- Who is on the FDA HACCP evaluation team?
- Will there be a written structure to the HACCP inspection, i.e. the Design Control requirements?
Why Should We Do This?
Not all these question could be answered. FDA is still in an evaluation mode trying to get volunteers from the industry to try this process. Companies that want to be part of this experiment would have to prepare a HACCP plan and send that plan to FDA, who will then audit the company to see how the plan worked. Once FDA learns more about this process, how hard it would be for companies to address this program, and the problems associated with conducting the inspections, the agency will then determine if they will make this a mandatory inspectional strategy or keep it voluntary.
Meanwhile, as FDA was looking for ways to reduce inspectional time (HACCP being one way), the agency was also evaluating their new QSIT (Quality System Inspection Technique) approach. Initially this was a big battle to see which approach would win out. Well, The QSIT approach won out. So where does this leave HACCP?
If things work out the way they have in the past, if a company lacks a HACCP plan it will be noted on an FDA 483 in the future. FDA wants this HACCP approach to become part of the medical device QSR. Just as validation was never actually part of the original GMPs in 1978, and HACCP is not mentioned as part of the QSR, it will be interpreted as being a part of the QSR not long from now. To this end, FDA has prepared a chart showing where each part of the HACCP plan can be interpreted as being required in the QSR (see chart below).
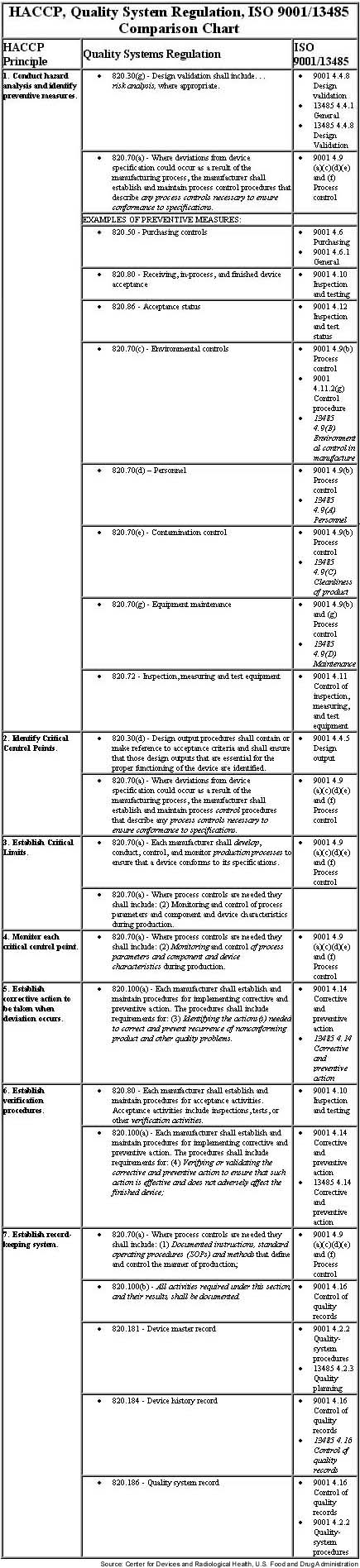
Will it or could it work? That depends on several factors:
- Will the industry see a real benefit to going through this exercise and using it?
- Will FDA keep their part of the bargain and actually reduce on-site inspectional time?
- Will providing FDA with a detailed road map of your areas of concern be a potential time bomb?
- Since you are already doing most of this in controlling your operations, what is the real concern of providing FDA a road map if they will be able to travel it faster and stick to the designated routes?
On the whole, the HACCP approach is one that could be of great value to any company and should be used whether a plan is provided to FDA or not. It makes you take a critical look at your operations and determine what you will have to control and what will be done in the event of a failure. But can an industry that just went through the traumatic experience of dealing with the new Quality System Regulation and Design Control requirements now be expected to deal with a new FDA inspectional approach? I am not sure that this is a good time for FDA come up with more changes, especially for the small medical device manufacturer.
If you are interested in trying this approach for controlling your operations, please contact me for more information. Or visit FDA's website at http://www.fda.gov/cdrh/gmp/haccp.html to learn more about HACCP as well as the Seven Sub-System approach.
Alan P. Schwartz is senior partner of mdi Consultants, Inc., a management consulting firm that helps medical product manufacturers meet FDA requirements. Since 1978, mdi has provided such services as 510(k) submissions, GMP compliance, FDA strategic planning, ISO assistance, as well as market evaluations and strategic partnering. With more than 28 years in the device industry, Schwartz has authored many articles and been a guest speaker both nationally and internationally. He can be reached at alan@mdiconsultants.com or through his website at http://www.mdiconsultants.com. Or visit the firm's storefront on Medical Design Online.