Harnessing The Future Of Digital And Smart Manufacturing Of Medical Devices
By Arokia Pranesh Kanna Sorimuthu
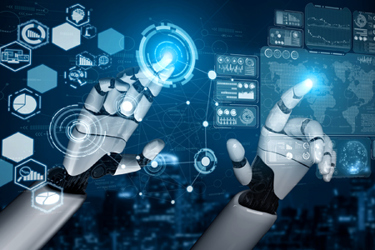
Digital transformation is rapidly evolving throughout the medical, pharmaceutical, and healthcare industries. In the medical device manufacturing segment, digital and smart manufacturing are essential to maximize efficiency, improve productivity, and exceed customer needs and expectations. Yet, many manufacturing processes are still performed manually. Reliance on outdated systems and processes negatively impacts corporate resources of time, money, and personnel. To eliminate this problem, systems, procedures, and processes need to continue to evolve, and advancements in automation can help accomplish these goals.
There are many benefits to medical device manufacturers that embrace digitalization and smart manufacturing. Not only does this transformation streamline work, which reduces errors and saves time and money on repetitive or mundane tasks, it also expedites the expansion of a company’s product portfolio and satisfies regulatory requirements. In the medtech industry, technical documentation is interconnected, so if paper content is revised, multiple documents must be updated to maintain accuracy. Converting these systems to digital makes updates and maintenance faster and simpler.
The digitalization of appropriate processes also improves end-user safety by removing risks associated with providing increased traceability of technical documentation. A design dossier, or a design history file, is one of the essential documents inspected by internal and external auditors. A comprehensive and fully traceable design dossier represents all the steps and evidence of the processes carried out during the design phase and enhances regulatory compliance, leading to smooth and transparent internal and external audits.
Inspecting these interconnected design elements when they are not digitalized is extremely difficult. This leads to longer turnaround times for medical manufacturers to fulfill the requirements and pulls valuable financial and employee resources from existing tasks. Increased traceability can be obtained only through digitalization.
Advanced Technologies And Industry 4.0
The movement toward mass digital and smart manufacturing has been dubbed the Fourth Industrial Revolution, or Industry 4.0, which includes:
- Implementation of artificial intelligence. Artificial intelligence (AI) in manufacturing can help with decision-making and creating countless data points that determine predictability, allowing manufacturers to take proactive steps to minimize errors and improve yield.
- Data analytics. New products improving patient safety are only possible when the manufacturers improve day-to-day operations by analyzing user response data points and leveraging insights.
- Machine learning. Machine learning algorithms can efficiently perform data collection and prediction of repeated tasks, improving accuracy and productivity. It can also assist with inventory management and compliance management.
- Reliance on the Internet of Things. The Internet of Things (IoT) has made remote monitoring possible by opening up opportunities for patient interactions with physicians, which is also cost-efficient. Wearables and home monitoring equipment allow physicians to keep track of a patient’s health more effectively and can be used to track medical equipment in real time.
To optimize the use of digitalization, it is essential to implement product life cycle management (PLM) systems. PLM manages the entire life cycle of a product from inception through engineering, manufacturing, and even servicing and disposal. Each part of the process that can be moved from manual to digital improves that individual step, and the more steps that are digitalized, the more impactful the overall outcome.
Smart manufacturing enhances digital manufacturing processes even further through the use of manufacturing execution systems (MESs). These are software solutions that connect live production information between multiple vendors and locations and integrate with a company’s existing equipment and business applications, creating smart connections. MESs deliver quality and efficiency, optimizing production and providing control over processes across the entire enterprise. An MES solution tailored to the medical device and diagnostic industry should generate a paperless manufacturing environment by eliminating much of the human element, reducing errors while increasing regulatory compliance.
R&D Versus Manufacturing
Connecting medical research and development (R&D) with manufacturing is critical to the success of digital and smart acceptance and implementation. For example, the role of an R&D team is to determine what product should be created and then proceed with the development of that item, adjusting and improving it along the way. Once a final decision is reached, the project shifts to manufacturing through a design transfer process, where the product is actually produced.
It is important for both the R&D and manufacturing teams to perform their duties as cleanly and efficiently as possible. This includes vital and continuous communication between the groups to facilitate informed decision-making. Without clear direction and specificity, the manufacturing team cannot satisfactorily complete the job. If the manufacturer runs into issues that tie back to the R&D team to resolve, it is vital to document these challenges and communicate appropriately so applicable revisions can be made. Without digitalization, this process would be slow and inefficient, potentially resulting in major delays and lost revenue.
Tips For Successful Implementation Of A Digital And Smart Manufacturing Plan
No new process is without its challenges, but it is possible to eliminate risks through awareness, careful planning, and mitigation. By doing the research before implementing a plan, an organization can be aware of potential issues. For example, companies can mitigate the problem of trying to move too much too fast by developing a plan to verify which systems are the most important to improve first and then identifying which processes can and can’t be easily digitalized. Not every process or product is upgradable, because some legacy products use older technology and documentation. For processes that can be upgraded, the implementation plan should be staggered. For legacy systems or products that cannot be upgraded, replacement is the only option, and this can be expensive. If multiple processes need to be upgraded, this also increases the cost.
To decrease expenses, companies must determine which systems are most important to upgrade and then compare those against the easily digitalized systems to see where they overlap. Then, companies can choose one solution to start with and proceed as finances permit.
For the successful implementation of a digital and smart manufacturing plan, follow these five steps:
- Run an end-to-end gap assessment of your business’ current conditions.
- Perform a feasibility analysis/risk assessment to evaluate the practicality of the plan before proceeding. Include stakeholders in this part of the process.
- Create a data configuration and transfer plan by performing remediation to migrate the current data and process to the digital environment, possibly with some modification.
- Once complete, validate, verify, process, and evaluate data in a training environment before launching the product.
- Go live with implementation and install a tracking system to verify effectiveness and opportunities for improvement through a formal control change process.
The Future Of Digitalization And Smart Manufacturing
One of the biggest lessons learned from the COVID-19 pandemic was that remote work and digitalization are the unavoidable future. By taking steps now to shift manual processes to a smart manufacturing system, organizations are better poised to meet ever-evolving consumer demands. To be successful, manufacturers need to designate or hire coordinators who take ownership of researching and implementing new digitalized systems. Even if an organization has upgraded some of its existing processes, new options regularly become available to replace or upgrade older technology. As such, vigilance and the willingness to change are essential to a company’s ongoing growth and success.
About the Author:
Arokia Pranesh Kanna Sorimuthu is a global delivery head and an associate general manager with over 20 years of experience in the medtech industry. He works with top medtech manufacturers to implement key projects in the R&D and manufacturing domains. He is pursuing an MBA from Jack Welch Management Institute (USA) and holds a bachelor’s degree in engineering from Karunya Institute of Technology and a diploma in mechanical engineering from St. Xavier’s Polytechnic in India. For more information, contact praneshkanna81@gmail.com.