How To Utilize Extrusion To Optimize Processing And Supply Of High-Quality Tubes For Use With Stents, Scaffolds, And Other Medical Devices
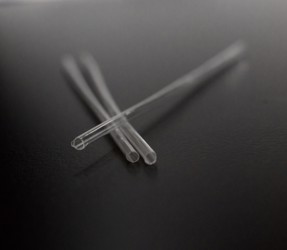
An interview with Dr. Thiago Borges.
The safety and performance of cardiovascular stents, as well as other medical devices used for vascular and general surgical procedures, can be optimized through the proper selection, fabrication and use of bioresorbable polymers with established extrusion processes. However, the development of high-quality standard or customized tubes can be complex, with extensive technical knowhow required. In this interview, Dr. Thiago Borges - Manager for customer projects at Evonik’s Medical Device Competence Center in Birmingham, Alabama, shares his tips on how to select the right materials, address specific structural and application requirements and then streamline the path to market. He also discusses a new service available from Evonik to provide customers with standard and custom tubes that can meet precise specifications.
Why is extrusion such a popular thermal process to help make device components?
Most bioresorbable medical devices use some type of thermal processing system such as single screw extrusion, compounding, injection molding or compression molding during the manufacturing process. The decision on what type of thermal process you use is typically depending on what type of final component you are planning to make. The safety history and easy to tailor properties of RESOMER® polymers make them attractive for use by device companies to create a variety of device parts for use across a range of cardiovascular, ENT, gastrointestinal and general surgery applications. For example, the laser-cutting of an extruded tube made of RESOMER develop biodegradable stents or vascular scaffolds. Likewise, extruded filaments can then be braided into stents, mesh or sutures, or used in FFF-based 3D printing systems to create more complex parts such as CMFs, spinal devices or fracture plates.
What are some of the key factors that need to be taken into account for the successful extrusion of bioresorbable polymers?
A holistic approach needs is required, as there are multiple variables that can affect the overall quality of the process, the selection of the best polymer and extrusion system, and the geometry and performance of the final product. Success requires extensive technical knowhow across an interconnected range of areas such as material handling, tooling design, the extrusion system itself, downstream equipment, and an analysis of the properties that you're trying to achieve for the final product. Take processing as just one example. Before the material even goes into the extrusion equipment, moisture needs to be controlled within an extremely well-defined range. If not, this can lead to degradation of the materials. Such adverse degradation can also be caused by the process temperature being too high, the residence time being too long, as well as the size and type of extrusion system that’s being used. You need to understand how all these factors are inter-related, or it will be hard to address the resulting drops in molecular weight, increases in residual monomer, part discoloring, or inconsistent flow during processing.
Why is Evonik now expanding its services to provide tubes that are made to order?
We’ve had an influx of medical device customers coming to us in recent years to receive material selection and application support that complements their own inhouse knowledge. With the technical expertise, extrusion and 3D printing equipment and other capabilities that are now available at our Medical Device Competence Center in the U.S., it makes sense to make the development and supply of customized tubes as a new service offering. We can now help customers to select the right material, development and optimize the process for GMP and technical batches, and then produce high-quality tubes in ISO 1345 certified cleanrooms. We can also offer additional analytical, mechanical, or degradation testing, and support manufacturing scale-up and the supply of regulatory documentation.
Why is the development of custom tubes so important?
It's important to be able to customize tubes according to the composition, dimension, additives, and properties that are required to optimize the performance of the target application and best match the product specifications. Because we offer such a wide selection of RESOMER polymers, it’s easy for us to tailor the composition, molecular weight and degradation time to match the geometry and performance requirements of the target application. When you combine this portfolio flexibility with our development services, we can rapidly develop and supply feasibility samples for testing and continuous improvement.
You mentioned geometry before. How can the geometry of a device component affect the extrusion process?
Each customer will have specific requirements for the shape, tolerance, precision, and accuracy of the tube. Our RESOMER® tubes can be offered on a diameter range going from 0.5 to 10 millimeters, with wall thickness from around 100 microns to one millimeter in size. We can also offer post-processing to further enhance those mechanical properties. In order to guarantee the quality of your tubes, we can provide 100% inspection. So, customers can be confident that our tubes will have tight tolerance and high concentricity. We can also offer the tubes in technical and GMP grade using this with the same high tolerance and high concentricity as well.
Why would a medical device customer want to outsource the extrusion of tubes?
Recent clinical trials for devices such as bioresorbable vascular scaffolds have shown how important it is to ensure that the mechanical and chemical properties of the final device reliably conform to specifications. For example, these devices must have excellent biocompatibility and good degradation profiles. But this can only be achieved from the chemistry side by selecting the right material or sterilization methods. It's also very important that such devices are fracture-resistant and have thin struts. But these outcomes are achieved through processing rather than chemistry. Thinner, stronger tubes can be attained by optimizing processing conditions and taking into account design considerations such as biaxial orientation.
For more information on Evonik’s custom tube services with RESOMER®, send the Company an email via resomer@evonik.com