Industry 4.0 Technologies Address Challenges Of Class III Medical Device Manufacturing
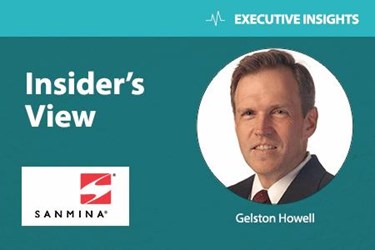
By Gelston Howell, Sanmina Corporation
Innovation in Class III medical devices — such as pacemakers, defibrillators, and implantable nerve stimulators — continues to accelerate at a rapid rate. Medical OEMs are designing more innovative and technically complex products in smaller form factors. In many cases, these OEMs partner with electronics manufacturing services (EMS) to produce such devices in high volumes.
For example, consider the complexity of manufacturing 20 million Class III devices a year, in an assembly and test process with 50 steps and using 80 components, some of which are too small to be handled by a human. These devices and the processes used for their manufacture must meet stringent FDA requirements for component traceability and verification, storage and access to device history records (DHR), and process compliance. The level of complexity involved in producing a Class III device in these volumes requires automated production line management. In addition, with thousands of kits of material required per week, inventory control on the production floor poses a significant challenge.
Industry 4.0 technologies — including machine-to-machine communication, cyber-physical systems, and cloud computing — are enabling the advanced automation required to overcome these production challenges. The increased connectivity and data-gathering provided by these technologies make it possible to build high-volume, regulation-compliant manufacturing processes with efficient inventory and production management. Consider the following examples of how Industry 4.0 technologies are being deployed to produce Class III devices in high volumes.
DHR, DMR, Medical Regulatory Compliance, And Machine-To-Cloud Communication
Recording a DHR for each Class III device is a regulatory requirement. The DHR demonstrates that the device has been manufactured according to the bill of materials, approved manufacturer list, procedures, and instructions in the Device Master Record (DMR). The DHR records device and component part numbers, unique serial numbers, date codes, date of manufacture, and the results of any tests or inspections. Not only is it a requirement to record the data and ensure that each device is manufactured in compliance with the DMR, the data must also be retrievable in a timely manner.
Scanners located in manufacturing machines communicate with Manufacturing Execution Systems (MES) in the cloud to ensure that only components specified in the DMR are assembled into products. The scanners upload the part number, serial number, and date code information to an electronic DHR. A device’s progress through the manufacturing and test process is recorded by machines and scanners. Results of optical inspections, pass/fail data, and parameters measured during test processes are uploaded from machines to the cloud MES system. All of this data in the electronic DHR is stored in the cloud MES and can be retrieved with a simple query.
Process Compliance, Forced Routing, And The Cyber Physical Factory
A Class III device being produced in high volumes can require as many as 50 process steps to build. Within those steps, 10-15 involve inspection, calibration, and testing required to complete production of each board. If the product fails an inspection or a test, it is routed out of the main process flow for diagnosis and repair. Following repair, products are reinserted in-line at the point just before the failure occurred. This practice ensures that each repaired product passes the test it originally failed.
Assuming, for this example, 20 million devices manufactured each year, the number of permutations of valid process paths that could occur as a result of pass/fail results at test and inspection is substantial. In such an environment, it is challenging to confirm that each product is manufactured using the defined process, but Industry 4.0 technologies and techniques can help manage that challenge. For example, the defined physical manufacturing and test process flow is replicated using a virtual factory in the cloud MES. Rules are established in the MES system for valid process flows. At every step of the manufacturing process, each product is scanned, and the MES forces it through the defined process flow, ensuring process compliance.
Miniature Components, Precision Tolerances, And Machine-To-Machine Communication
Some components are too small to be consistently handled by humans, and may need to be placed with an accuracy of less than 0.5 mm, with dimensional tolerances of 10 uM. High-definition vision systems inspect these components and confirm dimensions and orientation. The vision systems then communicate with specialized robotic equipment, which picks compliant components in the correct orientation and places them with the required accuracy. From a regulatory perspective, this process enables verifiable, repeatable component selection and placement.
Real-Time Inventory Control And Machine-to-Cloud Communication
On any given day, thousands of parts are transferred from the warehouse and placed on the factory floor in varying quantities. These components must be replenished from the warehouse, increasing component inventory on the production floor. As components are consumed and built into products, inventory is adjusted by reducing component inventory and increasing sub-assemblies or finished products.
In the past, managing inventory was manually transacted in an ERP system, such as Oracle or SAP. With the implementation of Industry 4.0 technologies and the use of machine-to-cloud communication, inventory management has moved from manual to automatic transactions, enabling real-time inventory control.
For example, an automatic optical inspection machine, having determined that an electronic PCBA is correctly assembled, communicates with the ERP system, directing it to consume the individual components, reducing the quantity located on the production floor while increasing the number of PCBAs available by one. This practice improves inventory accuracy in real-time and makes the process highly efficient.
In some markets, Industry 4.0 techniques we’ve discussed — including machine-to-machine communication, automation, and cyber-physical systems integrated to a cloud MES — are being applied to drive efficiencies and automate production. In the case of high-volume Class III medical device manufacturing, these techniques also are providing solutions to the challenges of regulatory compliance to record the DHR, ensure DMR compliance, and solve business problems like inventory management in high-volume manufacturing.
While the vision seems straight forward, the implementation does require advanced technology; the examples described here required machine-to-machine and machine-to-cloud interoperability among more than 20 different types of machines. In a high-volume manufacturing facility, connecting thousands of production and test systems with as many as 15 different protocols, all of which can talk to the cloud, is a daunting task. Industry 4.0 concepts and cloud technology are making such production feasible, though, and the results — in terms of compliance, efficiency, control, and manufacturing precision — are truly compelling.
About The Author
Gelson Howell is a Senior VP at Sanmina Corporation and has worked in the medical electronics and devices industry, as well as the computer and semiconductor industry, for 30 years. Gelston joined Sanmina in 2005 as Senior VP of the Medical Division. Prior to joining Sanmina, Gelston worked for Siemens Medical and Acuson in the medical ultrasound industry. Gelston began his career in the computer and semiconductor industry in a number of different positions, including IC and ASIC design, high performance multi-chip module development and manufacturing. Gelston graduated from Rensselaer Polytechnic Institute with bachelor’s and master’s degrees in electrical engineering, and holds two patents.