Inexpensive Resorbable Polymer Could Advance MedTech
By Chuck Seegert, Ph.D.
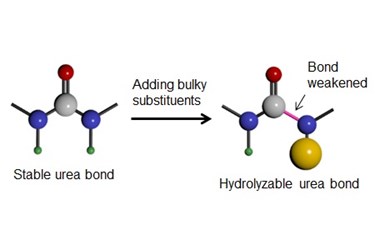
A new resorbable polymer may have the potential to replace existing materials used in medical device manufacturing. Cheaply made, the material can be tailored to degrade over wide range of timeframes, which may make it suitable for many applications.
Resorbable polymers, or plastics that break down in the body’s aqueous environment, have been in use for some time. Their value has been demonstrated in a number of applications, including tissue-engineered scaffolds, suture materials, and other wound closure devices. These materials generally break down as water hydrolyzes the bonds that form the plastic until they are eventually completely absorbed.
Recently, a relatively commonplace material has been adapted to fit into the hydrolyzable family of polymers, according to a recent press release from the University of Illinois at Urbana-Champaign. Polyurea are a type of material commonly found in paints, caulking, and certain glues. Interestingly, their current uses are often a result of their stability in the aqueous environment and their resistance to being broken down. New research, however, by University of Illinois engineers has changed how these polymers may be used.
The newly developed form of polyurea material is different because it contains hindered urea bonds, according to a recent study published by the team in the Journal of the American Chemical Society. The bonds are composed of 1-tert-butyl-1-ethylurea, and they are highly dynamic, which means that water can access and attack the bonds. The material can be configured into linear polymers or cross-linked gels, both of which are resorbable over time.
The simplicity of the reaction process makes the manufacture of these materials very low in cost, because synthesis only consists of mixing bulky multifunctional amines and isocyanates, according to the press release. The precursor materials are very cheap and easily obtained, and the reactions can be performed at ambient conditions. There are no harmful byproducts created during the processing, and the copolymer composition, which affects the degradation rate, can be easily changed. Additionally, the polymer, once it is synthesized, can be broken down in as little as a few days.
While resorbable materials are not a recent addition to the medical device landscape, their uses continue to increase. Recently, in an article on Med Device Online, a 3D printed resorbable technology was introduced.
Image Credit: Catherine Yao.