3 Keys To Developing A Successful DFM Process
By Todd Owens, Vice President of Engineering for Donatelle
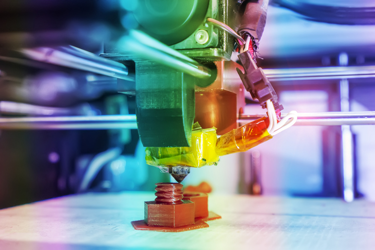
The manufacturing processes used to produce a new product are as important as the product characteristics that define and constrain it. Taking product development shortcuts up front to save cost or time on medical devices – deliberately or accidentally – often blows up on the back end with costly quality risks and manufacturing issues, and even product delays. Even a product with seemingly simple part geometry can be extremely challenging to manufacture.
That’s because many factors – including the materials used, required tolerances, part geometry, process control limitations, and more – influence how effectively and efficiently a product can be produced.
To ensure the value, quality and reliability of a new product at scale, implementing a robust design for manufacturability (DFM) process is one of the most important elements in designing, developing and manufacturing. When done well, a DFM process aligns product requirements with the capabilities of the manufacturing processes.
Here are three keys to implementing a successful DFM program
Get unlimited access to:
Enter your credentials below to log in. Not yet a member of Med Device Online? Subscribe today.