Leveling The Workload
By Darren Dolcemascolo, senior partner and co-founder, EMS Consulting Group
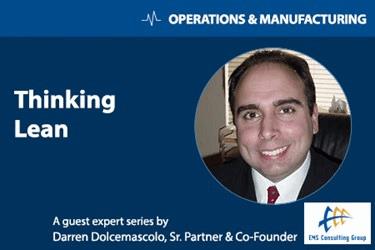
In the last edition of Thinking Lean, we discussed quick changeover, a system for reducing setup time on equipment and allowing for smaller batches. In this edition, we will cover a more generally applicable concept known as leveling production.
What Is Leveling?
Leveling work, a concept known as heijunka in Japanese, is one of those concepts from the Toyota Production System that is either ignored or misunderstood by many lean implementers. However, whether one is working to improve material flow, information flow, or other flow (such as patient flow in a hospital or surgery center), leveling the workload is a key to success.
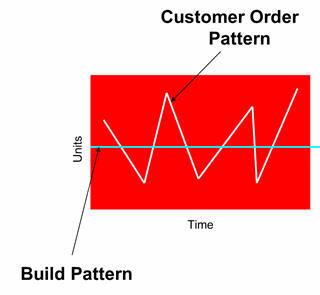
There are two major factors that allow us to buffer against demand: inventory, and production lead-time, or response time to the customer. Utilizing inventory to buffer against demand, we can hold finished goods inventory, ship to customer order, and replenish the inventory while building to a level schedule. Or, we can hold semi-finished inventory, and then complete or customize to customer order. This is dependent on the type of product we manufacture.
This second strategy works well for firms that have a standard base product that can be easily customized with particular software, packaging, or accessories. The second factor is lead-time. Some businesses can hold zero finished goods if their internal production lead-time is sufficiently shorter than the promised lead-time to the customer. For example, you might have a two-week promised lead-time and a three-day build cycle, or production lead-time. In this case, you would be able to build on a level schedule by adding customer orders to the schedule each day. The “backlog” of orders would change daily, but the build-rate per day would remain the same.
In order to level-load in a production environment, we divide products into families/categories of products. Break down products into A, B, and C unit volume categories within the families: A is top 60 percent of the volume, B is next 20 percent, and C is bottom 20 percent. Then, we make A products in very small batches, equal to one-day’s worth of demand. We make B products in batches ranging from daily to weekly. Finally, we allow a portion of time each day (or week) to run very low volume products (C items). This allows us to turn over our high-volume inventory much faster while maintaining a consistency in production. This consistency translates into value for our upstream processes and, potentially, our suppliers' production patterns.
Case Example: Leveling Work At A Medical Device Manufacturer
The following is a case from a medical device manufacturer producing implantable devices that are machined and assembled in-house. The company developed a pull system concept for various levels of production, both to reduce inventory and to reduce stock-outs. The company manufactures more than 100 stock-keeping units (SKUs) of implantable devices on CNC machines. These metal devices then are cleaned, assembled, and packaged into a variety of products.
For the machining operation, the manufacturer focuses on 20 key part numbers that make up 75 percent of demand. These key parts are manufactured in daily lots on a small number of machines; utilizing quick changeover, the company is able to make multiple changeovers per day efficiently. It stores these 20 part numbers in a supermarket of machined parts. The company also has storage for the remaining parts, but these are produced in weekly or — in cases for which the volumes are extremely low— monthly lots.
The assembly and packaging operations downstream have about 500 finished-good SKUs made from the 100 internally produced parts, plus other purchased components. Using a similar leveling strategy, about 70 key finished goods, making up 60 percent of all sales, are assembled in daily quantities and sent to a finished goods supermarket. Another 20 percent of the part numbers are assembled in weekly quantities, while the final 20 percent of the volume is made-to-order. This final 20 percent represents about 200 SKUs, but they are extremely low-volume productions, some of which are ordered only once per year.
This leveling scheme helps facilitate flow of product to the customer. The finished goods supermarket is designed to handle customer variability from day to day, which allows the assembly and packaging department to produce utilizing the leveling pattern discussed above. This level pattern of production ensures that the “pulls” from the machined parts supermarket will be even. There will be little variation from hour to hour or day to day. This allows the machining operation to produce in a level fashion, as well.
Leveling workload certainly needs to be a part of any lean transformation. It builds stability and allows concepts like standard work, one-piece flow, and pull systems to operate properly.