Mastering FDA Inspections: The Prep Work For Regulatory Success
By Jacob Foster, principal consultant, Medical Device Consulting, NSF
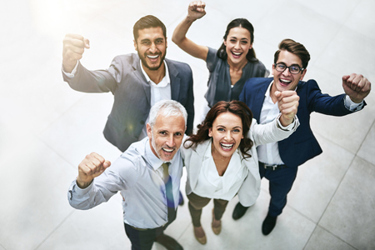
In the medical device industry, the stakes of an FDA inspection are high. Non-compliance can lead to delayed market access, product recalls, or regulatory actions that can jeopardize a company’s entire product line. Alternatively, inspections create opportunities for companies to refine their processes, strengthen their quality management systems, and mitigate risk. For seasoned professionals, the challenge lies in going beyond mere compliance to leverage inspections as a tool for long-term success.
Next-generation leaders in the medical device manufacturing industry should seek to push beyond basic compliance to explore expert-level strategies that master FDA inspections, streamline responses to Form 483 observations, and avoid common regulatory pitfalls. In our work advising medical device manufacturers, we highlight how integrating these insights into corrective and preventive action (CAPA) systems, documentation practices, and post-market surveillance can elevate compliance efforts.
Inspections Are Not Just Evaluations: They Are Strategic Opportunities
One of the key takeaways from navigating FDA inspections is understanding they aren’t simply evaluations — they’re opportunities to improve internal systems. Inspections offer an external lens to identify vulnerabilities that internal audits may miss.
Rather than viewing an inspection as a one-time event, treat it as part of a continuous improvement loop. Use the FDA’s feedback, even when minor, to revisit and enhance your quality management systems. Proactively addressing small inefficiencies can prevent larger, more systemic issues from arising.
For example, CAPA systems, often highlighted in inspections, provide a framework to dig deeper into root causes of issues. Instead of merely resolving surface-level problems, CAPA can drive company-wide improvements in product quality, risk management, and overall compliance.
CAPA Systems: Going Beyond Corrective Actions
FDA inspections focus heavily on how well companies implement their CAPA systems. During inspections, investigators often weigh whether corrective actions have been followed up with preventive strategies to avoid recurrence. The FDA’s Quality System Inspection Technique (QSIT) prioritizes CAPA as a critical subsystem to ensure long-term compliance.
An expert strategy would include building a dynamic CAPA system that doesn’t just react to problems but anticipates them. During the QSIT process, investigators scrutinize how CAPA systems are integrated with broader post-market surveillance efforts. To stay ahead, ensure that your CAPA reports are continuously revisited and assessed for long-term effectiveness and that preventive measures are woven into regular operational reviews.
As noted in FDA guidance, CAPA audits should be linked directly to post-market data to identify trends or issues early in the product life cycle. This proactive approach signals that your company is committed to quality and continuous improvement.
Post-Market Surveillance: From Compliance To Strategy
Many companies treat post-market surveillance as a checkbox activity, focused purely on reporting adverse events. However, robust post-market surveillance can serve as a strategic asset for product development and life cycle management.
Use real-world evidence (RWE) to enhance your post-market surveillance system. Integrating RWE allows for a broader analysis of how products perform in real-world settings and can help identify potential risks or improvements before they become significant issues. The FDA has been increasingly open to considering RWE in regulatory submissions, meaning that companies with robust post-market systems can accelerate time-to-market for product updates or new indications.
The current conversations regarding staffing of federal programs, including at the FDA, has created some uncertainty regarding the agency’s capacity to return to inspection activities at pre-pandemic levels. This may mean fewer standard surveillance inspections, and may result in actions by the FDA only “for cause,” creating recalls or warning letters due to post-market reporting. In essence, this makes the safety and effectiveness of devices and therapeutics, and the management of quality systems, more self-regulated by device manufacturers themselves.
Additionally, integrating surveillance feedback with your risk management strategy helps ensure that risks are continually reassessed and managed throughout the product life cycle, from design to post-market follow-up.
Documentation: A Competitive Asset
Documentation is consistently one of the most cited areas of non-compliance during FDA inspections. This includes incomplete records, outdated documents, or a failure to follow procedures. However, documentation can be more than a compliance requirement — it can be a powerful tool for competitive advantage.
Advanced tip: Move beyond traditional document management systems and invest in fully digital, cloud-based systems that allow for real-time updates and easy collaboration. FDA inspections often highlight issues in documentation as it pertains to post-market surveillance and design controls. By having a digital system that aligns all departments — research, development, compliance, and manufacturing — your company can demonstrate a commitment to quality that goes beyond regulatory minimums.
As outlined in the QSIT Manual, FDA investigators expect that manufacturers can retrieve any required documentation immediately during an inspection. Having a streamlined system in place not only reduces inspection risk but also improves overall operational efficiency.
External Audits: Leveraging Third-Party Expertise
While internal audits are critical, an external audit can provide an unbiased perspective on your quality management system’s compliance. External auditors bring experience from across the industry and can spot potential issues that might go unnoticed internally.
Regular third-party audits can serve as mock FDA inspections, identifying areas for improvement before the FDA does. These audits often reveal non-compliances or inefficiencies that internal teams may overlook due to familiarity or blind spots.
Use Compliance To Drive Innovation
FDA inspections are not a regulatory hurdle — they are a powerful tool for improving product quality, operational efficiency, and patient safety. By shifting from a reactive to a proactive mindset, companies can transform compliance into a strategic asset that drives innovation and long-term success.
Leverage the insights gained from inspections to continuously refine your CAPA processes, enhance your post-market surveillance efforts, and streamline documentation practices. When used effectively, these strategies ensure compliance and position your company as a leader in quality and regulatory excellence.
References
- FDA, “Quality System Inspection Technique (QSIT),” FDA.gov. Guide-to-Inspections-of-Quality-Systems.pdf