Materials Innovation: Propelling A New Era For Medical Devices
By Jiadong Gong and Severine Valdant, QuesTek Innovations, LLC
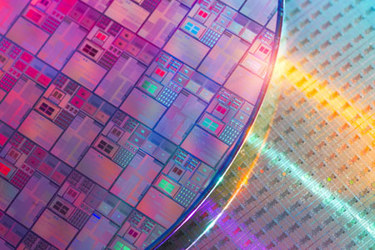
In many industries, including medical devices, the material has become the constraint. Following years of technological and engineering innovation, medical device designers are increasingly challenged by the limits of what the materials at their disposal can do.
It’s not surprising. The suite of materials used in medical devices hasn’t changed much in decades. When a material is proven to be biocompatible, safe, and effective, swapping it for a new material — and the qualification process that would require — is understandably daunting.
As device manufacturers look for ways to innovate and compete, novel materials present an underexplored avenue to unlock greater performance. And digital transformation in the materials sciences has reduced the time needed for qualification.
How can device manufacturers begin to consider what the alternatives to standard materials might allow for in a given medical application? And what would that process look like?
Materials Concurrency And The Corners Of The Design Space
In medical devices, there are some fairly rigid requirements with which to contend. Biocompatibility, for instance, is not negotiable for products that will be in direct contact with human tissues or fluids. Materials engineering is all about optimizing trade-offs between desirable properties.
Under traditional trial-and-error approaches to materials science, a requirement like biocompatibility proved extremely difficult. However, digital tools using computational physics can factor in biocompatibility as the baseline and explore all other variables while circumventing traditional materials science trial-and-error approaches.
How much can we increase one property without compromising other requirements? This is what we call the “corners of the design space.” These corners are where true innovation happens. The materials currently in use for medical devices are often not fully optimizing all of the properties that drive the performance of a product.
Novel materials are most effective at expanding the realm of possibility for medical devices when designers use a materials concurrency approach — in other words, designing a product and the material it is made of simultaneously. Uncovering the best possible elemental composition and manufacturing process for a given application is a competitive advantage for any medical device manufacturer.
Current Materials Engineering Challenges In Medical Devices
With a rapidly increasing number of people living past age 100, medical devices need to hold up longer. One way to increase strength and durability is size. A larger component can withstand more pressure and wear over time. But that’s not practical for items such as hip, knee, and spinal implants, which need to be sized precisely.
Designing a stronger material can increase both strength and durability while potentially allowing an implant to be smaller. Smaller implants have additional advantages because they’re often easier to install and remove, with less recovery time for the patient.
However, small or thin implants such as stents may lose radiopacity if they are downsized. The ability to view an implant on an X-ray is crucial to make sure it’s performing properly and hasn’t shifted.
For example, brain stents need to be much smaller than heart stents. Creating a radiopaque stent that is visible on an X-ray but small enough for use in the brain, while also durable enough to last the rest of the patient’s life, is exactly the kind of trade-off materials science is increasingly able to balance.
Another challenge is creating biodegradable or bioabsorbable implants that break down at just the right rate and get absorbed by the body or dissipate into the body when their function is no longer needed. Materials engineers can model the rate at which a material will degrade and how the body will process it in order to eliminate the need for removal. The biological process at which a material undergoes gradual degradation, as well as the composition of the material, can have additional benefits such as osseointegration and antibacterial properties.
Materially Advancing The Medical Device Field
Developing a novel material can often focus on modifying an existing material or process, rather than a clean sheet material design, particularly in a field with strict requirements such as medical devices. Small changes to a material or the manufacturing process can have a big impact.
Many stents are made of shape memory alloys, forming a mesh that expands when activated by the temperature of the body. This technology has existed for decades but continues to improve, allowing for more fatigue-resistant stents. Some medical device companies have patented shape memory alloys that differentiate their stents on the marketplace.
While steel is one of the oldest materials mankind has used to make things, it still has an excellent strength-to-weight ratio and it’s very well tolerated by the human body. New steels with properties that far exceed those of their predecessors are also commonly developed and patented in industries such as aerospace.
Another variable that can drive desirable properties in a material is processing, which can change the microstructure. A heat treatment, for example, has the potential to either enhance its performance or compromise requirements. This is another area where materials engineers use computational models to predict likely outcomes before verifying with tests.
Working Backward To Unlock Innovation
With materials engineering technology, it’s possible to start with the desired properties and work backward through a targeted microstructure and to the elemental composition and process needed to create them. Materials are a dimension that medical device designers can leverage to unlock new possibilities.
Materials science is a long game, but the rewards of advancing medical science are enormous. Realistically, a new material developed today for a medical device application would not be on the market by 2025, though it could be by 2035, and adopting that long-term mindset is key to the next wave of medical device breakthroughs.
Reframing the way we look at the materials challenge can help create solutions where they weren't obvious before. The aerospace industry is far ahead of the medical device industry in terms of using materials science to think long term and move the bounds of what is possible. Patients and shareholders alike are counting on medical device companies to adopt this mentality.
About The Authors:
Jiadong Gong is chief technology officer and Severine Valdant is chief commercial officer at QuesTek Innovations, LLC. QuesTek is a materials consulting firm based in Evanston, IL, with additional locations in Cambridge, MA; Solna, Sweden; and Tokyo, Japan.