Medical Device Manufacturer Implements A Next-Gen MES At A Third Of The Cost
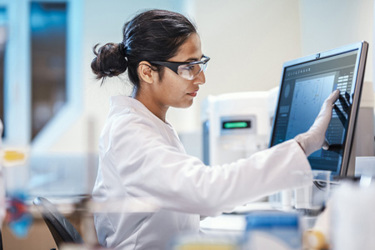
A leading medical device manufacturer faced the critical task of launching a new product introduction (NPI) for an innovative medical device within a newly established greenfield assembly facility. With a tight six-month deadline to begin large-scale production, the company needed to rapidly transition from low-volume, engineer-led builds to high-volume manufacturing performed by frontline workers. This required not only scaling up production capacity but also implementing robust Design for Assembly (DFA) and Design for Manufacturing (DFM) practices to ensure efficiency and quality. As the team began designing the production processes, they anticipated significant challenges. Chief among them was the risk of overwhelming new staff with frequently changing instructions and the complexity of accurately recording assembly data. The traditional approach of using paper-based Standard Operating Procedures (SOPs) and manual history records was quickly ruled out. It was deemed inefficient and impractical for onboarding a completely new workforce, especially in a fast-paced, high-compliance environment.
Instead, the team recognized the need for a more dynamic, digital solution that could support real-time updates, streamline training, and ensure consistent, compliant production at scale.
Get unlimited access to:
Enter your credentials below to log in. Not yet a member of Med Device Online? Subscribe today.