Advancing Medtech Development: Metal 3D Printing's Expanding Role
By Rob Bodor, VP and GM of the Americas, Proto Labs
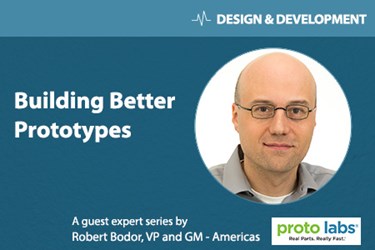
A post-surgical stroke patient needs a particularly large cranial implant, with permeability for liquids and the ability to dissipate heat from high exposure to sunshine.
A young cancer patient quickly needs a stable yet lightweight hip, with integrated joint replacement that precisely corresponds to the original.
A delicate surgical procedure calls for robotic-controlled forceps and retractors, with tips just a few millimeters in width.
Meeting patient needs in such challenging medical circumstances requires patient-specific implants and specialized surgical instruments. These implants and instruments can require parts so precise, so small and intricate — and often with features, geometries, or enclosed channels — that they would be impossible to produce without the industrial 3D-printing process of direct metal laser sintering (DMLS).
It has become common for medtech companies to use the additive manufacturing technology of DMLS for rapid prototyping of bone screws, joint replacement parts that need testing for fit and function, and small components for devices. DMLS produces fully dense metal parts, often with an accuracy and surface finish that allow the part to go directly into service, making it the 3D-printing process of choice for production or end-use parts across a variety of industries.
Time, cost, quality, and complexity of components are among the considerations driving both the global medical device development industry and the American aerospace industry to embrace additive manufacturing technologies, including DMLS. The design freedom DMLS offers enables engineers to iterate quickly, test multiple designs simultaneously, and drastically shorten their development cycles.
Hundreds of thousands of patients have 3D-printed hip joints or titanium jawbones, as well as other orthopedic implants and various prosthetics, according to a report from Wohlers Associates, which monitors the additive manufacturing industry. Overall, 3D printing could generate an economic impact of up to $550 billion a year to the broader economy by 2025, part of which would include the production of low-volume, high-value medical implants and tools, according to McKinsey Global Institute.
How DMLS Works
Understanding how DMLS works will help illustrate why manufacturers are adopting it, as well as its potential for dynamic growth. DMLS uses a laser to fuse powered metal (e.g., alloys of aluminum, cobalt chrome, Inconel, stainless steel, or titanium) into almost any geometry. The process begins with uploading a 3D CAD model, which is digitally sliced into very thin layers, roughly 0.001 in. thick. A high-powered laser beam passes over a bed of the atomized metal powder, melting and welding the metal to create a single layer of the CAD model. After each pass, a blade deposits a new coat of metal powder onto the bed, ready for the laser to fuse the next layer to the one beneath it. The part is built in layers, like a cake, but from the bottom up. The printed part often is ready in a matter of hours.
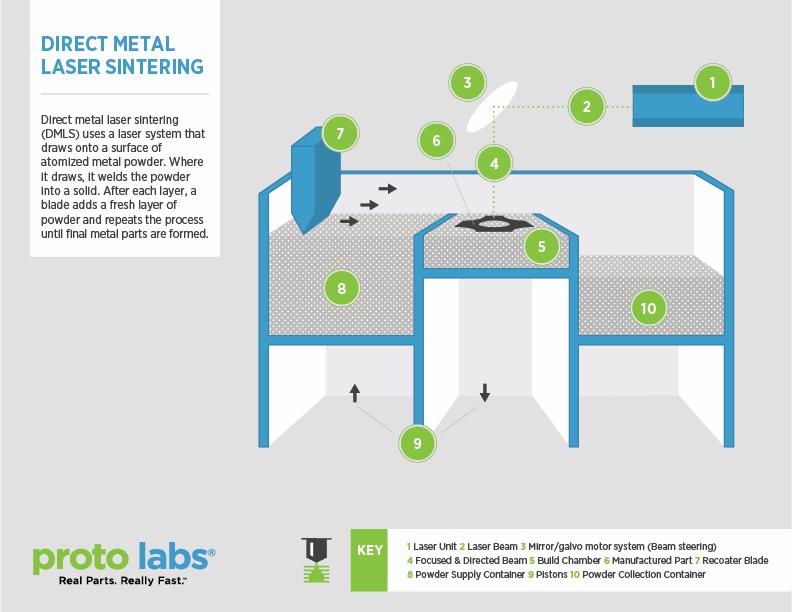
With its ability to "draw" one layer of a part at a time, DMLS offers the flexibility to create designs with internal features and passages that would be impossible to build with traditional casting or machining. Translating X-ray, MRI, or CT scans into digital 3D-print files makes possible production of implants and prostheses "in nearly any imaginable geometry," matching each patient’s needs, according to the National Center for Biotechnology Information.
DMLS also works well for producing lightweight parts or implants by incorporating cavities or recesses in complex shapes in ways that would be difficult to cast or machine.
DMLS Implants And Tools Meet Critical Medical Needs
Using DMLS to produce the cranial implant mentioned above, made of a biocompatible titanium alloy, enabled the design of a porous, lattice-structured part that allowed fluids to pass through the implant, facilitated its fusion with the bone tissue of the skull, and provided an insulation effect to minimize heat dissipation into the cranial cavity from high sun exposure. Preparing the data for the implant and constructing it took just two-and-a-half days.
Furthermore, DMLS is the only way to produce instruments like the very small, intricately detailed forceps, needle drivers, and retractors that surgeons use in robotic surgeries.
Patient-Centric Shift, Demographics Favor DMLS
The growth of patient-centric care and the shift toward value-based payment, a move accelerated under the Affordable Care Act (ACA), will lead to more customization of devices and greater variation, or to more versions of the same product. The DMLS process is an ideal solution to these market changes, giving manufacturers the ability to print a low volume of parts, tailor-made for individual patients, quickly and cost-effectively — avoiding the expense or lead times of machine tooling.
As my previous post noted, the size and growth of the aging population (the bulk of baby boomers are now aged 70 or older), along with the rising incidence of diabetes and other chronic diseases, will add to demand for improved and new medical devices, which DMLS can help manufacturers meet.
DMLS works with almost any alloy, with stainless steel, titanium, and cobalt chrome alloys the most common choices for medical applications. Stainless steel, often used for medical instruments, combines high strength and corrosion resistance. Cobalt chrome offers superb wear resistance and human biocompatibility, making it ideal for dental implants, hip and knee replacements, and arterial stents. Titanium, alloyed with aluminum and vanadium, also is biocompatible and is used extensively for bone screws, pins and plates, and implants.
When time and cost savings, design freedom, and the ability to manufacture highly organic shapes are among the requirements for your next product or surgical tool, DMLS deserves your consideration.
About The Author
Rob Bodor is currently VP and GM of the Americas at Proto Labs, a leading online and technology-enabled quick-turn manufacturer of custom prototypes and low-volume production. At Proto Labs, he has also held roles as CTO and director of business development. Prior to joining Proto Labs, Bodor held leadership roles at Honeywell and McKinsey & Company, and has been on the executive team of two early-stage software companies in the Twin Cities. Robert holds B.S., M.S., and Ph.D. degrees in engineering and computer science.