MIT Device Produces On-Demand Biopharmaceuticals In Less Than 24 Hours
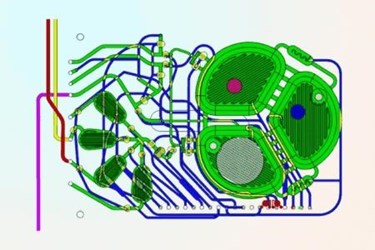
A new project led by MIT scientists and partially funded by the Defense Advanced Research Projects Agency (DARPA) has developed a microfluidic device that uses programmable yeast to manufacture biopharmaceutical drugs on demand. Researchers say that this portable device may be the key to delivering perishable biologic drugs, such as vaccines, to remote locations with limited medical resources.
Last March, a team of MIT scientists introduced a system that could produce small batches of pharmaceuticals on demand, to serve as an alternative to traditional manufacturing in special situations. With funding from DARPA and Novartis, the MIT team, led by Allan Myerson, produced a portable system that can be transported anywhere and produce pharmaceuticals, provided there is access to the appropriate chemicals.
Now, a separate team has turned its attention toward the portable production of biologic medications. Their solution was to cultivate programmable yeast called Pichia pastoris, which was chosen based on the density of its growth and its ability to express large amounts of protein. The yeast was genetically modified, the researchers told MIT News, to allow for the production of multiple medications.
Their bioreactor device — which is described in Nature Communications — is approximately the size of a laptop and contains a microfluidic chip. Liquid laced with chemical triggers is fed into the device and mixed with the yeast, and the device monitors temperature, oxygen, and pH levels to ensure the perfect environment for protein production.
In less than 24 hours, the researchers can produce a near single dose of biopharmaceuticals, and then the process can start over with a different liquid trigger — using the same yeast, once the previous fluid has been flushed out. In the study, researchers commented that additional improvements to the platform could lead to a “small-scale, portable, and fully integrated personal biomanufacturing platform that could advance disease treatment at point-of-care.”
“Imagine you were on Mars or in a remote desert without access to a full formulary, you could program the yeast to produce drugs on demand locally,” said Tim Lu, an associate professor of biological and electrical engineering at MIT. Lu added that the ability to produce single or multiple strain biologics or antibodies could be “a very powerful way of producing these drugs at a reasonable cost.”
“This sets the foundation for a new paradigm in terms of the way we manufacture pharmaceuticals and distribute them to patients,” said John Lewin, the division director of critical care and surgery pharmacy at Johns Hopkins, who was not involved in the MIT project. “Such a device could really meet a lot of the supply chain challenges here in the U.S. and around the world.”
The molecules that make up biopharmaceutical medications are large and prone to degrade more quickly than their chemical counterparts, requiring transport that is both time and temperature sensitive.
“It can often take weeks to months to manufacture and airlift organic pharmaceuticals and protein therapeutics to battlefield frontlines, meaning that critical medical supplies often do not arrive in time where they are needed most,” said Tyler McQuade, a program manager at DARPA, in a statement.
Last year, DARPA launched two programs challenging researchers to develop a portable device capable of producing pharmaceuticals — both chemical and biological — in less than 24 hours. Similar projects are underway at Ohio State University and University of Maryland.