7 Plastics-Related Challenges During Medical Device Manufacture (And How To Overcome Them)
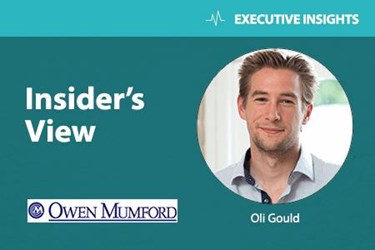
By Oli Gould, Owen Mumford
Plastic is a great material for use in the design and manufacture of a medical device. It is flexible, easy to use, cost-effective, and well-known by many engineers. But, as with any great success, there are a number of challenges that must be overcome.
When considering the use of plastic in a medical device design, one can only know so much about how the material will perform. Plastic has been commercially available for around a century now and is fairly well-understood, but it also is a highly sensitive material, prone to various changes in its properties in response to a great number of influencing factors.
These factors arise during manufacture of the raw material, conversion of the material into its required form, storage and, ultimately, end use. As such, these challenges are best managed early in the design process, before core commitments are made, and before the costs spiral out of control.
With this in mind, the following tips could prove useful in the successful development of a polymer- or plastic-based medical device:
1. Always Check The Datasheet In "Real-World" Conditions
A material datasheet touts attractive material properties, measured in favorable conditions. Objectively, the datasheet is accurate, but it is highly unlikely that an engineer will see the same properties, reacting in the same ways, when creating an actual component and testing in “real-world” conditions.
The reason for this disparity could be a manufacturing variation of the polymer, which can result in significant variation in properties like stiffness and strength, even with high-quality manufacturers and so-called “engineering” polymers. Similarly, test conditions rarely reflect desired use: If you are interested in the stiffness of a part, you are probably expecting some flexing of the part (the deflection). The standard test method, ISO 527-1, recommends 0.05 percent to 0.25 percent deflection, whereas a deflection ten times this size is common, and can compromise stiffness by 40 percent.
Engineers should be aware of the differences and set appropriate safety factors, or obtain more detailed material or test data early in the design process.
2. Beware The Color Change
Adding colorant to a polymer during part manufacture, or changing from one color to another, may change more than the polymer’s physical appearance. This two-to-three-percent change in the material’s chemical makeup can significantly affect mechanical properties.
Much of the time, changing or adding color has a negligible or manageable effect on a part’s performance. However, engineers need to be mindful of the risks and develop an appropriate mitigation strategy.
3. The Hotter The Temperature, The Greater The Expansion
The makeup of thermoplastics (which form the bulk of polymer types in the medical industry) makes these susceptible to expansion under elevated temperatures. This can be up to around ten times that of steel. The rate that a material expands with changing temperature is not a great deal on the face of it, but when you’re expecting to achieve a tolerance of less than 0.5 percent on a 100 mm part, a moderate shift of 10 degrees in temperature is significant. This can influence real world fit and function as well the measured size of the part.
The factor which is often most important when it comes to device performance is not the absolute expansion, but the differential expansion. Design engineers need to accommodate differential thermal expansion in addition to manufacturing variation and understand the temperature at which parts will be validated compared to that in use. Metrology engineers need to beware of the effects of temperature including, for example, handling components.
4. Understand Moisture Absorption And Linear Expansion
In a similar way, atmospheric humidity also can have a significant impact on a part size due to moisture absorption. In fact, in addition to polyamide (one of the worst offenders), polymers prone to moisture absorption can exhibit significant linear expansion within the range of 20-to-80 percent relative humidity. It is often the differential expansion that is of most concern. Design engineers and metrology engineers need to be aware of, and account for, the impact of varying humidity.
5. Accept Defects
Due to the manufacturing processes involved and the nature of the material, a deviation of the component’s geometry from the designer’s intent should be expected. It’s reasonable to expect deviations such as flash, sink, warp, weld lines, ejection pin marks, and injection point scars to some degree.
Developing a component that doesn’t rely on controlling these deviations should be an engineer’s first position. The second position is a determination whether, and how, to include each deviation in the device specifications, depending on the product’s required functional performance. For example, would it be appropriate to include flash (a sliver of material, present where two molded parts join) in a diameter measurement if a good deal of force (normal to the surface) will be applied to the product during use? An understanding during the design phase of the likely deviations and their relationship to functional performance is crucial in developing a part that is easy to manufacture.
6. Avoid Relying On Friction
During device development, it is notoriously difficult to predict a coefficient of friction when a polymer is involved. The surface properties of injection-molded components rely heavily on the tool finish, the material’s flow path, cooling rate, and packing pressure, just to name a few. So, before one has production-equivalent components in-hand, little confidence can be granted to estimates of friction.
The friction coefficient also is sensitive to ambient temperature, loading, time spent in a static condition, wear, and running velocity. Where higher surface pressures are relevant, microscopic deflections in the surface also affect the resultant frictional resistance. This occurs because the relevant angle of the normal force changes a few degrees with deflection of the mating surface.
Design engineers should target, where possible, a design which does not rely heavily on achieving a specific frictional resistance.
7. Know Your Additives
Plasticizing additives in PVC cables are known to significantly degrade the mechanical performance of some other polymers, notably polycarbonate. Particularly evident in areas where cables are slightly stressed, the plasticizer in PVC cables can be absorbed by surrounding materials, potentially causing the cables to become weaker and fail. This holds true for other additives, as well. In fact, some polymers can be surprisingly sensitive even to everyday contaminants, including natural aromatherapy oils on a user’s skin.
Understanding sensitivities to contaminants up front, and conducting appropriate environmental testing, is prudent before committing to any particular grade or polymer type.
Polymers are a tricky material to manage, particularly in a medical environment, but a prudent and well-informed design engineer can effectively manage the nuances of engineering with polymers, and the successful implementation brings great rewards.
About The Author
Oli Gould is a design engineering team manager at Owen Mumford. He holds a BSc in product design. He has worked in the medical device industry for three and a half years in his current role at Owen Mumford. Oli also has five years of industry experience at Dyson and P&G. His current role manages the development and performance of a team of design engineers and the engineering rigor, innovation, and development-related compliance associated with the delivery of a variety of medical products. His role also focuses on intra- and inter-departmental (R&D) best practice and process improvement.
About Owen Mumford
Owen Mumford develops medical devices for its own Owen Mumford brand and custom device solutions for the world’s major pharmaceutical and diagnostic companies. To learn more, visit Owen Mumford on Facebook, Twitter, and LinkedIn.