Polymer Processing
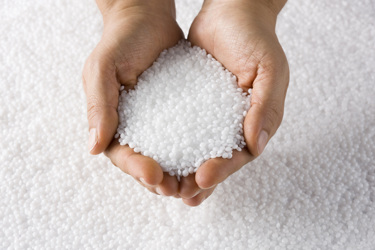
Polyzen is an innovative leader in the manufacturing and processing of components for a wide range of medical devices and is a preferred supplier to medical device OEMs worldwide. Extensive in-house processing capabilities and process technology experts enable us to manufacture an array of plastic components. These include medical grade polymer films and laminates, lay-flat tubing, balloons, bags, sleeves, stent and catheter coatings, and much more.
Medical Film Welding
Heat welding is commonly used to produce complex medical device shapes from polymer films. Film welding technology is ideal for low and high-volume production of products ranging from low-pressure balloons to bags, barrier sleeves, and sheathes for medical devices.
Welding Capabilities For Elastomeric Films
Using radio-frequency (RF), impulse, or ultrasonic welding techniques, Polyzen is able to produce weld seams as thin as 0.010 inches that retain mechanical strength similar to the film substrate. Polyzen’s in-house thin film welding capabilities includes experienced personnel and company-owned welding equipment needed to weld all types of polymer materials. This includes single and multi-layer elastomeric films.
Medical Thermoforming
Thermoforming involves the heating of medical polymer film above their softening point such that it conforms to a male or female mold cavity. Incorporation of vacuum pressure to the heated film, known as vacuum forming, ensures conformity to the mold configuration. In comparison to other processing methods, molds used for thermoforming and vacuum forming are economical due to the low pressure used in the process and limited mold complexity.
In-House Capabilities: Thermoforming And Vacuum Forming
Polyzen has in-house capabilities to produce films and molds used for thermoforming and vacuum forming. Our production equipment is capable of forming thermoplastic polyurethanes (TPUs), polyamides, ethylene-vinyl acetate (EVA), polyolefins, polyvinylidene fluoride (PVDF), polyvinyl chloride (PVC), engi- neering thermoplastics, and laminated films.
Medical Dip Molding, Coating, & Casting
Dip Molding, Coating, and Casting is a process using liquid resin solution and depositing the material on a mold or substrate, allowing the resin to cure and then demolding of the component. These processes are used to make products such as medical balloons or coating of stents, baskets, or catheters.
Dip Molding Capabilities For An Array Of Medical Needs
Dip molding is ideal for producing thin-walled, highly compliant balloons, coating stents and wires, casting specialty films, and more. Dip molding does not produce seams or mold parting lines on components, and it is ideal for fast prototyping and large-volume production runs. Dip and specialty coatings can provide soft grips or protective coatings to surgical instruments, containers, or components.
Polyzen has extensive experience and in-house capabilities to dip mold with thermoplastic polyurethanes (TPUs), thermoplastic elastomers (TPEs), silicone rubbers, and other polymer dispersions or solutions. In-house polymer solution formulation and mold development allows us to provide quick turnaround on dip molded, cast, and coated prototypes.