Stop Inspecting For Quality — Start Building It.
By Nero Haralalka, TBM Consulting
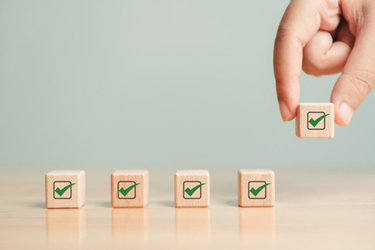
As medical device manufacturers, it is crucial to ensure that devices remain safe, effective, and in compliance with regulatory standards. Alarmingly, more than 70,000 adverse events — incidents leading to hospitalization, disability, or death — are reported to the FDA each month, highlighting the importance of your role across the medical device supply chain.
While most manufacturers in life sciences and other strictly regulated sectors prioritize quality control within their processes, the approach is often insufficient and delayed. Quality control and assurance activities that occur too late in the production process or rely excessively on a designated team of inspectors can lead to significant waste, rework, and increased labor costs, all of which erode profitability. Many manufacturers suffer the consequences of having a narrow focus on where quality management should start. It’s essential for medical device manufacturers, like those in other areas of life sciences, to integrate quality from the very start of the design phase, by specifying critical to quality (CTQ) requirements and maintaining rigorous quality assurance throughout the entire production process. To truly advance quality management, manufacturers must incorporate quality controls at that design phase, assess supplier risk in the planning stage, and instill a quality-centric mindset throughout the organizational culture, rather than just during final product inspection.
Embedding Quality Starting At The Design Stage
Quality cannot simply be inspected or tested into existence within products; it must be inherently established from the design phase and maintained through stringent control over the manufacturing process. This principle is particularly vital for medical device manufacturers as it is crucial not only for meeting compliance and operational standards but also for safeguarding the health and safety of end users.
Quality should be intentionally designed into products by implementing robust quality systems. A comprehensive quality management approach involves several key steps:
- Identify the processes and assign responsibilities that are essential to achieving quality objectives.
- Make sure that quality performance requirements are cascaded from the design phase to the production phase with proper risk assessment and mitigation before product launch.
- Mistake-proof risky production steps and find ways to prevent defects and eliminate the root causes of nonconformities.
Define clear quality objectives in the design phase and detail the necessary operational processes, resources, and suppliers required to achieve these goals. This includes specifying precise requirements that a product or process must meet, which could range from process or test specifications to product-specific requirements, such as performance specifications and technical drawings.
Quality management encompasses all tasks that need to be addressed throughout the product life cycle. This includes developing and applying quality planning, quality assurance, and quality control measures and addressing any deficiencies through quality improvement. At its essence, quality management is about ensuring that products not only meet but exceed the needs of hospitals, physicians, and patients, thereby fostering customer loyalty and achieving long-term success.
Cultivating A Quality-Centric Culture
I recently worked with a medical device manufacturer seeking to enhance its quality systems. Like many manufacturers, this company relied heavily on a large team of inspectors to conduct product testing at the end of the production line. The inspectors were proficient, effectively identifying and removing defects, which is exactly what they were tasked and compensated to do. However, this scenario prompted a critical question: What if these defects could have been prevented in the process? By reevaluating its approach to quality, this manufacturer was able to decrease its reliance on full-time quality control personnel by up to 55% in some facilities, simultaneously reducing rework and significantly improving financial performance. This success prompted an effort to embed a quality mindset within the company culture earlier in the product life cycle.
5 Focus Areas To Transform Quality Culture Successfully
1. Leadership Commitment to Quality
It starts with leadership; company leaders must fully embrace the importance of quality and recognize its potential impact on the bottom line. Introducing processes and validation methods that engage teams and foster a commitment to quality as a core component of daily operations is crucial.
A practical approach is to ensure discussions around production emphasize not only speed to market but also key quality metrics like first time yield (FTY) and rolled throughput yield (RTI), which gauge the quality of units produced on the first attempt. These discussions help set the expectation that products are not only launched on time and within budget but also meet high-quality standards.
2. Integrating Quality in Design and Development
Companies genuinely dedicated to a quality culture invest the necessary time and effort to design and develop products and processes that reflect this commitment. Instead of replicating existing processes or maintaining the status quo, embracing thorough analysis during design helps prevent high failure rates at final testing, which are often traced back to early development stages. Employing tools like design failure mode effects analysis (DFMEA) and process failure mode effects analysis (PFMEA) with a cross-functional team is crucial in systematically identifying and mitigating potential failures in systems, products, or processes.
3. Quality as Everyone's Responsibility
Using DFMEA and PFMEA not only demonstrates that quality is everyone's job but also provides a structure to address quality gaps across the business — from the production floor to the executive level — with clear actions and measurable outcomes. For example, introducing in-process inspections can detect defects early in high-risk areas, which is more cost-effective and less complex than addressing them later in the process.
4. Proactive Supplier Selection
Quality management should be initiated before raw materials even arrive. Engage with procurement early in the planning process to establish up-front supplier selection criteria and a certification program based on supplier scorecards. This approach ensures that materials meeting these criteria will require less inspection upon arrival, reducing inspection time by 20%–30%, decreasing the frequency of quality issues, and eliminating the need to return defective materials. It’s important to not only focus on first-tier suppliers but to also consider second- and third-tier suppliers.
Additionally, it’s crucial to identify potential risks associated with the components sourced from suppliers. This includes determining whether parts are custom-built or off-the-shelf, as well as understanding their manufacturing complexities. For critical components, conducting a design failure mode and effects analysis (FMEA) and assessing the severity of potential failure impacts on end users are essential steps.
Identified risks, including those related to regulatory compliance, must be thoroughly assessed to establish the necessary types and extents of control measures. These measures should be clearly defined, documented, and cover all required quality standards.
Examples of Possible Control Measures:
- Conducting supplier audits: Ensuring environmental compatibility
- Performing testing and verification: Verifying reliability
- Issuing Certificates of Analysis: Assessing process capability and capacity
- Defining measurement criteria and methods: Validating processes
- Analyzing measurement systems: Monitoring response times
More information on supplier qualification measures can be found here.
5. Establishing a Problem-Solving Culture
In environments where a quality culture thrives, efforts extend beyond mere risk mitigation to include proactive problem-solving across the organization. Empowering operators to address issues as they arise and supporting them with processes to explore and rectify the root causes of defects not only enhances quality but also improves operational efficiency.
Rethinking Quality For Better Outcomes
The medical device industry's commitment to quality cannot be overstated. By embedding quality control measures early in the design and development processes, and by fostering a culture that views quality as everyone’s responsibility, manufacturers can reduce costs, minimize risk, and, most importantly, improve patient safety. The transformation from quality inspection to quality integration is not merely a shift in operations but a strategic move toward achieving greater efficiency, reliability, and trust in medical device manufacturing. This proactive approach promises not only to meet but exceed the expectations of hospitals, physicians, and patients, thereby securing a competitive edge in a rapidly evolving marketplace.
About The Author:
Nero Haralalka is director, US Consulting, at TBM Consulting Group. He is a Lean Sigma Master Black Belt with 35 years of experience in the areas of operational excellence, product development, statistical modeling (including the use of AI), and root cause problem solving. Haralalka has a master’s degree in mechanical engineering from the Illinois Institute of Technology in Chicago and a B.S. in mechanical engineering from the Birla Institute of Technology in Ranchi, India. He also has AAMI QSR Certification.