The Design Controls + Risk Management Connection — Intended Use & User Needs
By Jon Speer, founder & VP of QA/RA, greenlight.guru
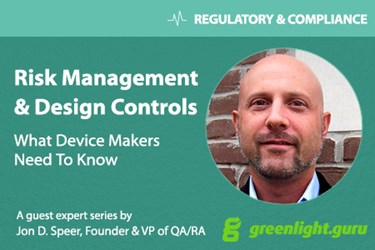
Medical devices are intended to save and improve quality of life.
I like the ISO 13485:2003 definition of a medical device: “Any instrument, apparatus, implement, machine, appliance, implant, in vitro reagent or calibrator, software, material or other similar or related article, intended by the manufacturer to be used, alone or in combination, for human beings for one or more of the specific purpose(s) of:
- diagnosis, prevention, monitoring, treatment or alleviation of disease
- diagnosis, monitoring, treatment, alleviation of or compensation for an injury
- investigation, replacement, modification, or support of the anatomy or of a physiological process
- supporting or sustaining life
- control of conception
- disinfection of medical devices
- providing information for medical purposes by means of in vitro examination of specimens derived from the human body”
A medical device should address a specific patient and clinical need, defined by manufacturers in an intended use statement. Intended use is key to your product development and risk management efforts, as well as critical to your regulatory strategy, helping to determine classification and go-to-market strategy.
This is really where a medical device’s journey begins. Design controls and risk management should flow and blend together, and it’s important to establish this flow early in product development. Intended use is a gateway to user needs, design & development plan, design inputs, risk management plan, hazards, hazardous situations, and foreseeable sequence of events.
Intended Use Helps Define User Needs
Intended use defines the purpose of a medical device. User needs are then derived and defined from the intended use to describe:
- Who will use this device?
- How will the user and patient interact with the device?
- What type of procedures will the device be used for?
- What type of environment will the device be used in?
- When will the device be used?
- Is the device used one time, or over and over?
- What other products will the device interact and interface with?
I’ve talked before about the importance of user needs in the design controls process. User needs start the “waterfall,” and design validation closes the process, cycling back to user needs.
Apply Intended Use To Your Design & Development Plan
Intended use and user needs define the scope of a project, and they are instrumental in establishing a design & development plan. Such a plan needs to define:
- Design & development stages and activities
- Who is responsible for design & development activities
- Resources required, such as project team members and key vendors
- Timing of design reviews
The plan is not a “one and done” and needs to be revisited and updated throughout the project.
Design Inputs Build On User Needs
To define design inputs for your medical device, you need to understand user needs. I’m guessing you can cite several projects where you were able to define design inputs, but there may not have been any defined user needs. Actually, there were user needs —they just might not have been documented, and this can be an issue.
User needs should always be defined and documented. Doing so helps to define design inputs. Otherwise, you might have to guess and fill in the blanks. When this latter approach is taken, you can progress far into product development before realizing your device has not addressed key aspects from the end-user and patient perspective. It’s even possible to launch a device into the market and discover later, through product complaints, that you overlooked some user needs.
Intended use usually comprises a few sentences that describe what a product is supposed to do. User needs are a series of statements that further describe the intended use. It is okay if your user needs are somewhat vague and ambiguous.
For example, a user need may state something like “the product should be easy to use.” This is where design inputs come into play. They describe and define “easy to use” in clear, objective terms. Think of the design inputs as a contract — a product developer should be able to reference this contract during design and development of the product.
Intended Use Guides Risk Management Planning
One of the first steps involved in medical device risk management is establishing a risk management plan, which describes risk management activities throughout the product lifecycle. Roles and responsibilities, as well as the risk management team, are defined. Intended use is important because it helps to establish the scope to which risk management activities will be necessary.
The risk management plan also includes criteria for your medical device’s risk acceptability, which should be commensurate with the intended use. Like the design & development plan, a risk management plan is continually evolving throughout the product lifecycle.
Hazards, Hazardous Situations, Foreseeable Sequence Of Events Based On Intended Use
Risk management also includes risk analysis and risk evaluation — described in Understanding ISO 14971 Medical Device Risk Management. Risk analysis and risk evaluation make up what is known as a risk assessment.
A risk assessment, based on a device’s intended use, determines the possible hazards, hazardous situations, and foreseeable sequence of events related to your medical device. A hazard is a potential source of harm, while a hazardous situation is a circumstance in which people, property, or the environment are exposed to one or more hazard(s). The foreseeable sequence of events lays out the steps required for a hazardous situation to result.
The Connection Between Design Controls And Risk Management
Just as intended use plays a vital role in design control and risk management, design control and risk management are vital to one another. Some companies treat design controls and risk management as related but separate processes, not realizing the close connection between user needs, design inputs, hazards, and hazardous situations.
Intended use leads to user needs, which lead to design inputs — the “contract” by which medical devices are designed and developed. Intended use also helps define the scope of a design & development plan, as well as the scope of a risk management plan. All of this information is used to determine hazards, hazardous situations, and foreseeable sequence of events.
As I stated at the beginning of this article, medical devices are intended to save and improve quality of life. Following sound design controls and risk management processes helps ensure that the devices you design, develop, manufacture, and sell are as safe and effective as possible.
About The Author
Jon D. Speer is the founder and VP of QA/RA at greenlight.guru, a software company that produces beautifully simple quality, compliance and risk management software exclusively for medical device companies. He is also the founder of Creo Quality, a consultancy that specializes in assisting startup medical device companies with product development, quality systems, regulatory compliance, and project management. Jon started his career in the medical device industry over 16 years ago as a product development engineer after receiving his BS in chemical engineering from Rose-Hulman Institute of Technology.