The Importance Of Liquid Silicone Rubber In Medical Device Development
By Rob Bodor, VP and GM of the Americas, Proto Labs
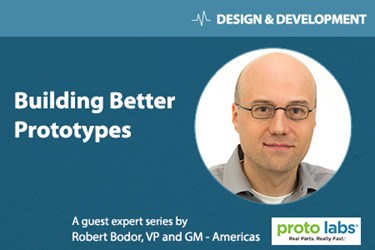
Every product places demands on materials, but demands in the medical industry can be particularly stringent. When medical products and devices don’t perform as they should, the consequences can be serious, immediate, and costly. The strict regulations on medical products can help prevent those problems, but they also pose a set of development challenges in getting a product to market. In a growing number of instances, the material to help answer these challenges — in terms of both performance and meeting regulatory requirements — is thermosetting liquid silicone rubber (LSR).
One of the major obstacles facing medical products is contact with living tissue, either externally (skin contact) or internally (e.g., with implantable devices). It’s a two-way challenge: The product must not irritate or otherwise affect the tissue, and the material itself cannot be adversely affected by contact with that tissue.
Another requirement is sterilization. Whether designed for one-time or repeated use, medical products must be sterile, which typically entails exposure to high heat. Many thermoplastics by their very nature cannot stand up to heat.
Cleaning and disinfection can require the use of chemicals, so depending on the application, the material may also have to withstand often-harsh chemical exposure. Some applications may expose a material to UV radiation, which can break down or discolor materials, while others can expose a product to extreme cold that can make materials brittle and subject to breakage.
Finally there are cosmetic considerations. A product or device may perform flawlessly, but if it appears old, worn, or otherwise compromised, it can raise questions regarding its functionality.
For all these reasons, LSR can be an ideal material for medical applications. Nearly every grade of LSR is biocompatible, and the material is available in grades specifically developed and approved for implants* and similar medical applications. LSR is extremely stable and can withstand high levels of heat and exposure to cleaning and disinfecting chemicals. Its heat resistance also makes it suitable for heat-related treatment applications such as cauterization, in which it can be used as safety shields on cauterizing tools.
On the opposite side of extreme temperature, the material is also suitable for applications that expose it to cold — freezing for removal of warts and similar procedures, for instance. Unlike other materials that are flexible at room temperature, LSR will not become brittle under cold conditions. (Of course, LSR is not the only flexible material available for medical applications. Thermoplastics elastomers, or TPEs, are less expensive and may be perfectly suitable for room temperature applications.)
Another reason to potentially use LSR components on medical devices is purely cosmetic. In the medical world, perceived quality can be critical, and anything that appears to be a flaw may be interpreted as an actual defect, even if it has no impact on function. For example, a transparent part that yellows due to UV exposure may continue to perform perfectly fine, but the discoloration may be misinterpreted by patients and doctors alike. This is another area in which LSR excels, remaining virtually unaffected by environmental factors. It is also highly scratch resistant, so in addition to resisting wear and retaining its functionality, LSR remains cosmetically attractive throughout its life.
In addition to meeting the stringent demands of medical applications, LSR has several unique and useful characteristics:
- In its liquid form, and before being solidified by heat in the mold, LSR has very low viscosity. This allows it to fill very small features and thin walls without risk of voids or porosity. Of course, low viscosity can lead to flash due to leakage where mold halves meet, but this can be minimized with careful mold design.
- Transparent, optical LSR is a newer material available to developers. It’s ideal for applications like light covers, lenses, and light pipes. Its light transmission exceeds that of other plastics and is second only to glass; its stability prevents damage due to heat from light sources; and because of its flexibility, light pipes can be molded straight and then bent for assembly, simplifying manufacturing.
- Due to its flexibility, LSR can be molded in shapes that would otherwise be trapped in molds. LSR parts with undercuts, no draft, or even negative draft can be manually peeled out of molds without damage. This can eliminate the need for costly side-action cams and provides great flexibility for the designer. Multiple parts — a lens, protective cover, and waterproof seal, for example — could be combined into one part, simplifying the bill of materials and reducing both molding and assembly costs.
- LSR is available in multiple durometers (degrees of hardness), allowing the designer to match the material to the function of the part. A soft, relatively tacky LSR might be used as feet or a base for a device to keep it from sliding when in use. That same tackiness might make the surface of a device hard to clean if stored in a dusty environment. A material between those two in hardness might be the ideal choice for a gasket designed to seal liquid in or moisture out. Of course, when multiple functions are combined in a single part, the designer will have to consider whether a single material can support all the necessary functions (but that is what prototyping is for).
- Since LSR cannot be machined, creation of functional LSR prototypes requires molding. Traditional molding has not been affordable at low volumes, but automated generation of toolpaths for milling aluminum molds (by providers like Proto Labs) has greatly reduced that cost. LSR molding can now be affordable at volumes as low as 25 pieces for prototyping, low-volume production, or bridge tooling.
- LSR is also ideal for overmolding, in which a molded or assembled part is inserted into another mold, which is then injected with LSR to create a second layer of material over the first. Overmolding works extremely well for devices with handles, for example, that need to be biocompatible, heat- and chemical-resistant, and just plain comfortable to grip.
In short, LSR is the ideal material for a variety of medical applications. While soft thermoplastics like TPE duplicate some of its characteristics, nothing else offers LSR’s combination of biocompatibility; resistance to heat, cold, chemicals and UV light; durability; design flexibility; and moldability. For some (though not all) applications, final manufacturing will require facilities with medical ISO 13485 certification. Non-certified facilities can be used for production of parts that don’t require the certification and for development and verification — form, fit, and functional testing — of those that do.
To learn more about LSR, download the Proto Labs tech brief Liquid Silicone Rubber Takes The Heat.
About The Author
Rob Bodor is currently VP and GM of the Americas at Proto Labs, a leading online and technology-enabled quick-turn manufacturer of custom parts for prototyping and low- to mid-volume production. At Proto Labs, he has also held roles as CTO and director of business development. Prior to joining Proto Labs, Bodor held leadership roles at Honeywell and McKinsey & Company, and has been on the executive team of two early-stage software companies in the Twin Cities. Robert holds B.S., M.S., and Ph.D. degrees in engineering and computer science.
* Proto Labs does not currently offer LSR grades specifically developed and approved for implants at this time.