4 Tips For Medical Device Design Success
By Tom KraMer, Kablooe Design
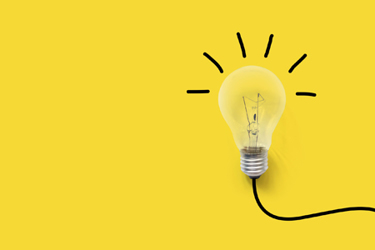
We are all eagerly anticipating what the new year will bring us, with hopes of improvements, prosperous endeavors, and positive outcomes. I have found that when developing a forward vision, it always helps to look back and see what we learned in the past. Sometimes we learn things the hard way, and sometimes it’s easier, but those lessons can help us take positive steps forward.
This season I thought it would be nice to look at some of the more “hands-on” type activities in design and development and reflect on some lessons that will help with future innovation projects this year. Using a surgical device project as a metaphorical springboard, here are some items worth reflection:
1. Building things in 3D CAD is not the same as building them in real life.
For instance, when you’re working on something really tiny — like an end effector for a surgical robotic device that’s going to enter a small space in the human tissue — you absolutely have to do a real-world comparison. If you rely too heavily on a CAD design, it might look like everything is moving, clicking, and rotating just fine, but in reality, the movement and actions will put too much force on the part, causing failure in some part of the device. When we get too much tunnel-vision in our CAD parts it becomes easy to lose sight of all of the physical factors that play into a functional mechanism’s success. Friction, wear, shear, tortional strength, cantilevering, moment arms, etc. can easily be bypassed while we are excited to get a new idea built. Considering these items and stepping into the empirical world of hands-on prototypes is a great way to see things that will spark the right side of your brain to begin to create more “what if” scenarios. This leads to more ideas and more innovation, so don’t be afraid to start prototyping in quick, simple, and easy ways as early as you can to bring your loftiest ideas down to reality.
2. Imitating the robustness of the human body is not a simple task.
If the surgical standard is a physician holding a scalpel, then your design certainly has an uphill battle. Human fingers can do a lot of things: they’re cushioned, they rotate easily, they’re durable, they can be moved into a large variety of unique positions, and they can give the user immediate feedback on how hard they’re pressing and on the characteristics of the surfaces they are touching. If you’re designing a tiny end effector for a robotic arm, every tolerance along the way needs to be just as small, nimble, and durable, which can be a daunting task. Try thinking about the feedback that the active parts of the human body are giving to the brain during the associated device’s tasks and begin to think about what the brain would have to do without that feedback and how your device can give similar or alternative feedback to the brain. This will put you in the shoes of the user and will lead to some innovative solutions.
3. Empowering the user with good design is not the same thing as designing a well-functioning device.
Surgeons need to be empowered to do their jobs better. We certainly don’t want the tools we design for them to take away their decision-making ability, their autonomy to change their minds and adapt on the fly. Rather, you need to figure out a way to enhance those abilities. Empowering a user to do their job better starts with understanding their needs in performing that job. If your device is there to help them do that job, then we need deep insight into the user’s needs. This doesn’t just come from quick, standard voice of customer data; it also comes from rich empathetic insights that only result from observations, ethnographies, and stories directly from the users’ experiences that give us insights into their world in relation to the device we are focusing on changing. Try spending time with users and instead of bombarding them with questions, get them to tell stories about usage experiences, and find out how they feel about them. This information can be boiled down into design requirements that will drive the creativity of your team to solve the problems your device is trying to solve.
4. Inspiration can come from outside the industry.
There are only so many insights to be gained from studying other medical devices, so why limit yourself to only one pool of knowledge? Broaden your research to include other less related industries such as agriculture, manufacturing, and military. You’d be surprised how much you can learn just from watching warehouse fulfillment robots work for an hour or two. I am always impressed with how many unique product solutions can come from the toys we designed so many years ago or the farming implements we developed ideas for.
We not only get inspiration from analogous devices, but we get it from nature, too. Nature provides a vast pool of intricately designed working systems with marvelous little parts that function in fantastically amazing ways. What better way to be inspired to innovate?
On your next project, try walking away from the specific industry your device is intended for and spend some time pondering other unique devices and systems. Then go back to your project with a set of fresh eyes and a flexed right-brain, and see what the innate innovator inside of you can come up with.
Conclusion
Taking a proactive approach to these lessons by incorporating the learnings into your innovation and development process will hopefully bring some new insight and color to your efforts this year. If you take action to understand the user, their needs, and the problem that has to be solved, then all you need to do after that is make sure your design is manufacturable, durable, and can function as intended. Keep on learning, and you’ll be on a very good path to creative innovation in surgical robotics design!
About The Author:
Tom KraMer, president and CEO of Kablooe Design, has been a product innovator for over 30 years. He holds a certificate in master of product development from Northwestern University and a bachelor’s degree in industrial design from the Minneapolis College of Art and Design (MCAD), as well as a certificate from Stanford University’s Cardiovascular System in Health and Disease program. KraMer has created revenue for countless customers by delivering innovative product solutions to their portfolios. He spearheaded the D3 Process (Design Driven Development), a vehicle to provide these results to customers, and he teaches this process by traveling as a lecturer and speaking about innovation and development processes.