Writing Compliant IQ/OQ/PQ Protocols — Meeting FDA Expectations
By Joy McElroy
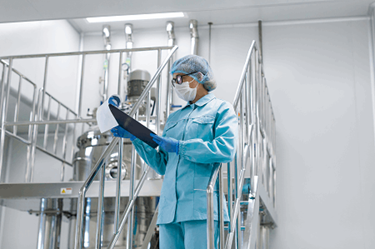
Regulations require equipment, systems, and utilities used for GMP manufacture or services to demonstrate suitability for the intended use and to operate according to their design and functional specifications. In order to meet these requirements, qualification protocols must be written for installation, operational, and performance verification. These protocols have to verify proper installation, adequate support utilities, operation over its entire range, and acceptable performance according to established SOPs and operational set points. Protocols must be in place, be based on user and functional specifications, and be approved prior to execution. Many times, companies fail to execute appropriate protocols, or protocols are found to lack necessary information and often fall short of providing the necessary tests for suitability and functional design specifications.
FDA Requirements
The FDA requires verification that equipment specifications have been met. Verification is the confirmation by examination and provision of objective evidence that specified requirements have been fulfilled. Validation is the confirmation by examination and provision of objective evidence that the particular requirements for a specific intended use can be consistently fulfilled. Whenever the results cannot be fully verified by subsequent verification and tests, the equipment has to be validated with a high degree of assurance and approved according to facilities’ established procedures.
Manufacturing and analytical equipment is validated by performing equipment qualifications. Qualifications are the actions of proving through documented evidence that any premise, system, and items of equipment work correctly and lead to expected results. Therefore, installation qualifications (IQs), operational qualifications (OQs), and performance qualifications (PQs) have to be written properly and effectively.
Installation Qualifications
IQs demonstrate that the process or equipment meets all specifications, is installed correctly, and all required components and documentation needed for continued operation are installed and in place.
The installation qualification ensures the equipment/system and its components are installed correctly according to the original manufacturer’s specifications. All calibrations of major and accessory equipment must be performed during the IQ as well. Other things to consider are equipment design features, safety features, environmental conditions, and supplier documentation for preventive maintenance.
Design features included in an IQ include equipment, process piping, environment, valves, lubricants, safety devices, alarms, instrumentation, and utilities.
IQ sections and requirements are as follows:
- Purpose: This section should state the qualification needs of the equipment. The statement must be direct and to the point. The purpose should not be more than one or two sentences.
- Scope: The scope should state whether the qualification is for a new piece of equipment or for modifying previously qualified equipment. Like the purpose, this statement must be direct and to the point and should not be more than one or two sentences.
- Equipment System/Description: This section is a paragraph describing what the equipment does, how it is used, what process/products use it, and its basic design features.
- Supplier: The supplier section will include vendor certification and safety feature verification.
- Equipment Components: Identify and briefly describe each major component of the subject equipment in this section. Define all system and equipment boundaries with other systems or equipment. It is necessary to list all ancillary equipment used in conjunction with the equipment being qualified as appropriate.
- Utilities: Identify all utilities required to operate the equipment.
- Construction, Installation, and Requirements: In this section, the cleaning procedures that must be executed after the equipment is installed are recorded. Document that the cleaning procedures have been successfully executed and completed. A common pitfall here is that SOPs are not effective at the time the IQ is executed. It is important to make sure all SOPs are in effect at the completion of the installation qualification. Therefore, cleaning SOPs may be added as attachments to the protocol.
- Supporting Documentation: List supporting documentation that may be used to identify or operate the equipment such as engineering turnover packages, purchase orders, or equipment manuals.
- Maintenance Programs: This should include established maintenance procedures and a listing of any preventive maintenance activities.
- Spare/Change Parts: Provide a list of spare parts and change parts that are required for system operation, including a description of the part and part number of reference for tracking throughout the facility.
- Drawings: List and include in the system drawings used to support the IQ. Drawings must be labeled with a title, a drawing number, and the date of the drawing. Drawings may be redlined to reflect current changes; however, they must be redrawn and put into effect within the document management system before implementation of the performance qualification (PQ).
- Testing and Acceptance Criteria: Acceptance criteria must be approved by quality assurance prior to executing any IQ. Define the test procedure. IQ testing must be designed to confirm that the equipment is installed in accordance with manufacturer’s recommendation and to document justification for exceptions. Defined acceptance criteria are a pass/fail result.
- Discrepancies: This section will discuss and justify events per required deviation procedure.
- Summary and Conclusion: Summarize the IQ test results, demonstrating that the equipment was installed correctly. Provide a conclusion on whether the equipment installation is acceptable.
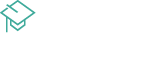
Learn more about applying Good Manufacturing Practices (GMP) concepts to Quality Control and Quality Assurance when implementing your QMS in Joy's course:
FDA Compliant QC and QA Practices: Creating a Perfect, Audit-Ready QMS
Operational Qualification (OQ)
The OQ is the documentation of objective evidence showing that the equipment operates according to manufacturer’s specifications. In the OQ, tests are performed on the critical parameters of the system/process. These are usually the independent and/or manipulated variables associated with the system/equipment. All tests’ data and measurements must be documented in order to set a baseline for the system/equipment.
OQ sections and requirements include the following:
- Purpose: This section should state the qualification needs of the equipment. The statement must be direct and to the point and should not be more than one or two sentences.
- Scope: The scope should state whether the qualification is for a new piece of equipment or for modifying previously qualified equipment. Like the purpose, this statement must be direct and to the point and should not be more than one or two sentences.
- Equipment System/ Description: This section is a paragraph describing what the equipment does, how it is used, what process/products use it, and its basic design features.
- Operational Qualification Prerequisites: Verify all IQ tests have been completed prior to execution of OQ.
- Test Equipment Calibration Verification: A completed record of qualified test equipment and approved materials that is used during protocol execution is included in this section of the OQ. List all calibration dates and the next due date for calibration.
- Standard Operating Procedures: Establish operating, maintenance, setup, and/or cleaning procedures for the equipment. Procedure(s) shall be approved by management and quality assurance and effective before or by end of OQ completion. These SOPs may be added to the protocol as attachments.
- Alarm/Control Challenges: This test section should identify and challenge critical alarms associated with the equipment/system.
- Operating Parameters: Verify the key and critical operating parameters as stated by the manufacturer. Be sure to verify the operating ranges and acceptance criteria for each parameter.
- Rationale and Sampling Locations: Provide rationale for the qualification approach, the sample size, selected test conditions, and the critical testing parameters.
- Testing and Acceptance Criteria: Define the test range for each critical operating parameter for verification. The testing range will bracket the operating range to ensure equipment is qualified within the manufacturer’s suggested range for optimal operation. The number of test runs needed is traditionally three; however, it should be statistically justified, and it may be dependent on the complexity of the equipment.
- Test Result Documentation: Summarize test results and confirm the acceptance criteria in this section.
- Discrepancies: This section will discuss and justify events per required deviation procedure.
- Summary and Conclusion: Summarize equipment OQ results and provide a conclusion on whether the OQ is acceptable and the equipment is validated.
Performance Qualification (PQ)
The PQ is the third and final phase of equipment qualification. This phase tests the ability of the equipment to perform consistently over long periods of time within tolerance deemed acceptable by the manufacturing process as a whole. This phase may be performed in conjunction with the process validation. During the PQ stage of process validation, the process design is evaluated to determine if it is capable of reproducible consistent commercial manufacture.
The PQ involves verifying that utility systems and equipment operate in accordance with the process requirements in all anticipated operating ranges. This should include challenging the equipment or system functions while under load comparable to that expected during routine production. It should also include the performance of interventions, stoppage, and start-up as is expected during routine production. Operating ranges should be shown capable of being held as long as would be necessary during routine production.
The PQ combines the actual facility, utilities, equipment, and the trained personnel with the commercial manufacturing process, control procedures, and components to produce commercial batches. A successful PQ will confirm the process design and demonstrate that the commercial manufacturing process performs as expected. The approach to PQ should be based on sound science and the manufacturer’s overall level of product and process understanding and demonstrable control. The cumulative data from all relevant studies (designed experiments; laboratory, pilot, and commercial batches) should be used to establish the manufacturing conditions in the PQ. To understand the commercial process sufficiently, the manufacturer will need to consider the effects of scale. It is not typically necessary to explore the entire operating range at commercial scale if assurance can be provided by process design data. Previous credible experience with sufficiently similar products and processes can also be helpful. Firms should employ objective measures (e.g., statistical metrics) wherever feasible and meaningful to achieve adequate assurance. In most cases, PQ will have a higher level of sampling, additional testing, and greater scrutiny of process performance than would be typical of routine commercial production.
The level of monitoring and testing should be sufficient to confirm uniform product quality throughout the batch. The increased level of scrutiny, testing, and sampling is to establish levels and frequency of routine sampling and monitoring for the particular product and process as the facility moves into actual manufacturing.
Considerations for the duration of the heightened sampling and monitoring period could include, but are not limited to: volume of production, process complexity, level of process understanding, and experience with similar products and processes.
Conclusion
Writing effective IQ/OQ/PQ protocols is a must for following the regulations required by the FDA for equipment, systems, and utilities to demonstrate suitability for the intended use and to operate according to their design and functional specifications. In order to prove the requirements are met, qualification protocols have to be written and followed. These protocols are documented evidence that manufacturing firms are in compliance with cGMPs. Following these guidelines, your facility’s IQ/OQ/PQ protocols will be effective and provide adequate proof of compliance.
About The Author:
Joy McElroy is the founder and principal consultant at Maynard Consulting Company, which provides services in validation engineering, process engineering, quality control, and quality assurance. McElroy began her career in the pharmaceutical industry performing environmental monitoring and sterility testing, and then moved into a supervisory role overseeing quality control. From there, she moved into quality assurance, and then into equipment qualification and process validation. In addition to consulting, she also develops and delivers webinars, on-site training, and seminars in areas such as technical writing, equipment qualification, cleaning validation, FDA audit preparation, and more.
McElroy earned her B.S. in zoology from North Carolina State University. You can reach her at joy@maynardconsultingcompany.com or connect with her on LinkedIn.