Your Best Chance At Regulatory Compliance For Combination Products: Integrated Development
By Fran L. DeGrazio, Strategic Parenteral Solutions LLS
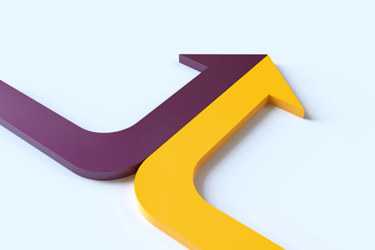
The near-term future of combination products continues to be the growth of prefillable syringe systems (PFS) and their use in autoinjectors (AI), especially due to the trend toward self-administration. Per Vantage Market Research, the global prefilled syringe market is projected to reach a value of $10.59 billion by 2030. This correlates to a CAGR of 8.70% from 2023 to 2030.
One recent example of this trend toward self-administration is the injectable monoclonal antibody belimumab, which is used to treat active autoantibody-positive systemic lupus erythematosus and active lupus nephritis in patients who are receiving lupus treatments. Originally approved by the FDA in 2011, the medicine is currently available in three forms: a vial/stopper/seal glass container system, a prefilled glass syringe, and an autoinjector (with prefilled syringe), with the autoinjector being approved by the FDA in 2017. Both the prefilled syringe and auto injector versions can be used in the home setting. This is only one example of many biologic drugs provided in similar formats.
The coming together of the drug with its packaging and its delivery system brings with it some of the greatest challenges for manufacturers from a technical and regulatory standpoint. As presented in 21 CFR Part 4, a combination product is composed of two or more different types of medical products. Several U.S. regulatory documents, including the FDA Guidance for Industry and FDA staff: Current Good Manufacturing Practice Requirements for Combination Products, published in January 2017, clearly present prefilled syringes and prefilled syringes in autoinjectors as combination products.
In Europe the regulatory framework for medical devices, Regulation (EU) 2017/745, explains that systems marketed as a single integral product intended exclusively for use in the given combination and that are not reusable are governed by the medicinal products framework. For PFS, this means the relevant general safety and performance requirements (GSPRs) of Annex 1 of the MDR (Medical Device Regulations) must be met.
Integrating Drug And Device cGMP
The FDA now defines a prefilled syringe, a product that was at one point considered “packaging” for a drug, as a constituent part of a combination product. The ultimate combination of the drug, its package, and its delivery device means that during development and manufacturing there is a need to combine both drug and device current good manufacturing practices (cGMPs) and quality approaches, even though prefillable syringes may be considered a “commodity” product by those who are less familiar (i.e., non-technical/non-regulatory professionals).
QbD And Design Controls
In the past, meeting the drug GMPs was the minimum needed for regulatory approval. Through the years, however, best practices that build on this foundation have been developed. A best practice expectation now is to develop a new drug from a risk-based perspective. The driver behind this was the release of documents such as ICH Q8 R2 (Pharmaceutical Development), ICH Q9 (Quality Risk Management), ICH Q10 (Pharmaceutical Quality System), ICH Q11 (Development & manufacture of drug substances), and ICH Q12 (Technical & Regulatory considerations for pharmaceutical product lifecycle management). These guidances form the foundation for quality by design (QbD) in drug development and commercialization. QbD employs a risk-based approach that improves product and process understanding through building knowledge via statistical and analytical approaches. Quality is built in from the beginning of the development process. It is, in essence, the drug version of design controls for medical devices.
Terminology is different between QbD and design controls, so this becomes part of the challenge in working to develop a combination product. You are truly bringing together science and engineering in a way that has not been done in the past.
Through QbD, you build a design space that is focused on robustness. A complete picture allows the understanding of the product and process so process analytical technology (PAT) can be leveraged within manufacturing. All this development and understanding should tie to a robust control strategy that applies to both the drug and the device portions of the combination product.
21 CFR Part 4 – Regulation of Combination Products does make it clear that the applicable parts of the drug and device regulations must be met. The translation from regulation to practice and how that applies to the total combination product are the issues.
The challenge in the recent past is that while QbD and design controls have been established for some time for drugs and devices, how they apply to the total combination product has not. Best practices and guidance continue to be developed in this space, with varying amounts of knowledge and experience across the industry.
Essential Performance Requirements
Since PFS is now deemed a combination product, the functional aspects of delivery are as important as the chemical aspects of the package itself. Essential performance requirements (EPRs) or primary functions (PF) become extremely important to characterize and identify during development. Prefilled syringes have the benefit of having a commonly accepted ISO standard used as a reference. This standard, ISO 11040-8: Prefilled Syringes, connects back to a series of normative references that allow you to best identify the testing needed for the specific drug product and patient application. The FDA is to release an EPR guidance by the end of 2023 that should provide more elucidation around the terminology and requirements. Of course, the guidance, coupled with the risk-based development process, should inform the choices made throughout the process.
Prefilled syringes in autoinjectors follow this same path of understanding. Currently, the FDA considers EPRs as attributes responsible for the clinical performance of the delivery system at point of dosing, including those required to administer the dose. This is very similar to the concept of “primary functions” as designed in ISO 11608-1:2022 Needle-based injection systems for medical use.
Although a platform approach may be taken by companies working on multiple drug products that are delivered by a prefilled syringe and an autoinjector, it is important to understand and characterize each piece of the platform while understanding that the requirements for the design inputs and target product profile should be unique and well understood for the specific therapeutic category, patient group, and user group.
The FDA Draft Guidance Bridging for Drug-Device and Biologic-Device Combination Products (published in December 2019) provides direction on how to leverage data that may have been generated in another development program to support a new application. Utilizing risk analysis to understand what data can be used is a key part of this process.
During development, when setting up the user needs and target product profile, form, fit, and function should be considered. This includes the typical requirements of a drug or biologic from a stability standpoint plus considerations around protection, compatibility, and performance of the device. Additionally, these pieces cannot be taken separately as the fit between the primary package and the device/delivery system can be a key source of potential problems if not understood and controlled effectively.
The proactive engagement of drug, packaging, and device subject matter experts during the chemistry, manufacturing & controls (CMC) process will help to minimize development or post-market problems.
Conclusion
This article only touches on the very significant challenge of delivering combination products to patients in an efficient manner. A deep dive is needed for anyone engaging in active development and commercialization of these products.
Innovation of syringes and autoinjectors continues. This means even more new challenges from a technical and regulatory perspective. Examples of this are the addition of digital/software capabilities, an increase in the volume that the systems can deliver, and the addition of new aspects such as gas-powered systems, to name a few. Optimization of an integrated development process that can be replicated and executed upon is the best way to assure success since combination products are the future of the industry.
About The Author:
Fran DeGrazio is a Kymanox executive advisor as well as president and principal consultant for Strategic Parenteral Solutions LLC. She has more than 35 years of experience in the pharmaceutical packaging and delivery industry, with extensive expertise in sterile drug product systems, including vial container closure systems and prefillable systems for combination products.