PTI Packaging and Inspection Systems
8 Skyline Drive
Hawthorne, NY 10532 US
914.337.2005
Hawthorne, NY 10532 US
914.337.2005
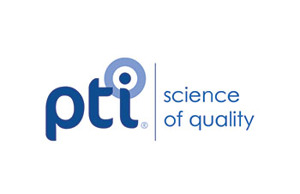
Company Overview
Packaging Technologies & Inspection (PTI) is a leading manufacturer of inspection technologies for the pharmaceutical industry that are non-destructive, non-invasive and require no sample preparation.