Look, Ma! How I Solved These Disposable Diagnostic Device Challenges
By Zach Hayman, Accumold
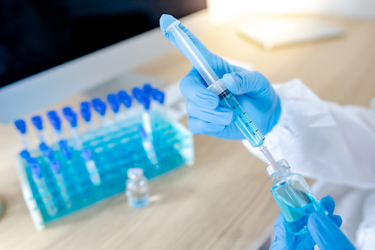
Disposable diagnostics fill a unique niche in the realm of medical devices. They are subject to many of the same regulations and design challenges as their non-disposable brethren, but include additional layers of difficulty, such as the need for production in significantly higher volumes and concerns surrounding disposables’ environmental impact.
Navigating this minefield of potential issues requires manufacturers to take an in-depth look at scalability, business strategy, and supplier capability and sustainability, as well as scrutinize their vendors’ methods to overcoming possible roadblocks. However, when one of those vendors is a micro molder, manufacturer opinions about costs, capabilities, and component performance may be erroneously based on their experiences with traditional molders. Clearing up these misconceptions can change the whole arc of a disposable diagnostic product by enlightening a manufacturer’s R&D and management teams to what might be possible.
Scalability Was Always The Plan!
Typical medical device component volumes usually don’t reach stratospheric levels, perhaps 50,000 to 150,000 units per year, depending on the device. However, disposable diagnostics often require consumer product-level component volumes: for example, one current Accumold project in this field ships approximately 100,000,000 components a year.
Get unlimited access to:
Enter your credentials below to log in. Not yet a member of Med Device Online? Subscribe today.