Material Evidence: Examining Mysterious Design Failures
By Jeffrey Ellis, Battelle
It’s every medical device manufacturer’s nightmare: an unexpected material failure leading to a product recall. Then, the investigation begins. Everything looked great in the lab — what happened to cause the device to fail in the field?
Material failures in medical devices are both common and costly. In 2013 and 2014, materials failures were implicated in 30-40 percent of FDA recalls. These recalls cost companies tens or hundreds of millions of dollars in direct expenses, stock devaluation, and lost sales. In addition, many companies found themselves facing late-stage design changes and product launch delays due to material problems found late in the development cycle.
Fortunately, most of these material failures are preventable. Understanding the most common causes of material failures in medical devices can help manufacturers make better design decisions up front and avoid surprises after product launch.
Types Of Medical Device Material Failures
Material performance is complicated but, generally speaking there are three main factors to consider: the structure-based intrinsic properties of the material itself, how the material is processed, and the environment in which it is used. Most material failures are caused by misunderstandings of how these factors work together to influence product performance and longevity.
Common causes of material failures include:
- Improper materials selection
- Problems with raw materials or reagents
- Manufacturing process incompatibility or inconsistency
- Degradation or deformation of materials due to aging
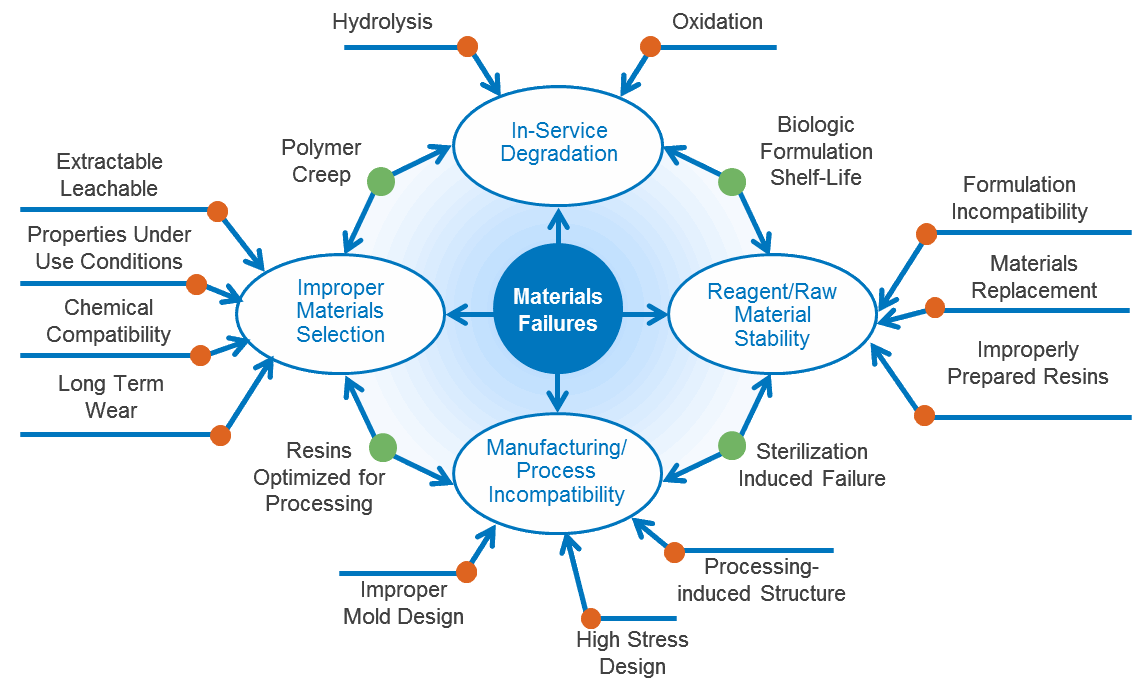
What the Data Sheet Can (And Can’t) Tell You
Materials selection is the first critical materials-related decision to be made, and the materials data sheet is a good place to start. The data sheet provides critical information including mechanical properties related to strain, stress, and impact strength. However, the data sheet alone is not adequate for final materials selection. All too often, this important qualifier is ignored: Data herein is typical and not to be construed as specifications. Unless otherwise specified, all data listed is for natural or black-colored materials. Pigments can affect properties.
This disclaimer is a critical one. The properties listed on the data sheet only define the material’s properties under controlled lab conditions. The data sheet will not tell you how the material will perform:
- after adding pigments or undergoing other processing during manufacturing;
- when exposed to different environmental conditions (e.g., temperature, moisture, or exposure to other materials or chemicals); or
- after long-term aging.
How Processing Affects Material Properties
Material properties can be impacted significantly by processing. Changes or inconsistencies in the processing method can result in unanticipated changes in the physical properties of the final material. Processing variables can include:
- the addition of pigments or other additives;
- conditions during mixing (e.g., temperature, moisture, mixing speed, etc.); and
- the timing, sequence, or number of process steps.
In one case that Battelle investigated, a PVC component was exhibiting discoloration and cracking when exposed to high moisture conditions. The problem turned out to be improper control of temperature during mixing, which resulted in a two-phase melt and a weak, inhomogeneous material. Tightening up the processing window resolved the issue by creating a one-phase melt and a strong, homogeneous material.
In another case, the addition of pigment during a separate pellet-processing step caused a drop in molecular weight, which caused the material to crack after aging. Changing the procedure so that coloring was added during injection molding, thus eliminating a processing step, improved material performance.
The Impact Of Use Environment
The environment in which a medical device is stored or used will impact material performance and aging. Medical device manufacturers should carefully consider the environmental conditions the device will be exposed to during the material selection process. Questions to consider include:
- Will the device be exposed to extreme temperature variations during shipping, storage or use?
- Will the device be stored in a refrigerator or freezer?
- What other materials does the material in question come into contact with, either in the form of another device component or during normal use?
- What chemicals will the device come into contact with (e.g., drugs or cleaning chemicals)?
- Will the device need to undergo sterilization processes?
- Will the device be exposed to moisture?
- Will the device be exposed to vibration during storage or use?
Proper materials selection must include testing of the material under the conditions in which it will be shipped, stored, and used. Environmental conditions can change stress and strain curves for a material, causing it to become more brittle or more easily deformed. For example, one company’s medical device used a silicone cover to dampen the sound of a vibrating component. Unfortunately, the vibration increased the brittleness of the silicone, causing it to be prone to shattering, even at room temperature.
Understanding Aging
Most materials data sheets do not include long-term properties. Accelerated aging tests can uncover risks related to changes in material performance over time.
These tests are especially important for components that are under continual stress or strain, such as spring-loaded mechanisms or parts designed with interference. Over time, creep can cause these components to deform and slip, impacting device performance or causing the device to behave in unexpected ways. For example, a spring-driven drug delivery device might fire on its own after a long time in storage. Finite element analysis, combined with time-temperature superposition creep data, can be used to quantify the risk of material creep under different stress conditions.
Reducing The Risk Of Material Failures
Many material failures are due to a combination of issues. One manufacturer experienced an issue wherein storage containers for an expensive drug started failing. The drug was stored in an ultra-low temperature freezer, which, as expected, made the material more brittle. However, only some of the containers failed, seemingly at random. The ultimate cause was traced to a problem with the extrusion blow molding process. Inconsistent processing led to variations in the thickness of the walls at the pinch-off point, increasing the risk of fracture under extreme cold conditions for containers with thinner than normal walls. In this case, there was no single cause of the failure, but rather a combination of high-stress design, processes with low reproducibility, and extreme temperatures.
This complexity can make finding the root cause of a material failure a real detective job. Materials scientists with experience in root cause analysis and accelerated aging can help medical device manufacturers get to the bottom of device failures. If you do not have this expertise on staff, it is wise to engage a third party with materials science expertise.
Paying attention to structure, process, and environment for your materials can substantially reduce the risk of material failures in the field. Time spent up front on materials issues will pay dividends in reduced risk, fewer recalls, and improved customer satisfaction.
About The Author
Dr. Ellis received his Ph.D. in Chemical Engineering from The Ohio State University where his focus was supercritical fluid polymer processing of diagnostic medical devices at the nano-scale. He has worked at Battelle for the last seven years and held the position of lead scientist on a number of programs with specialization in polymer processing, selection, failure analysis, testing, degradation, and aging. His work has produced a number of publications and patents.