Plastics Selection For Medical Wearables: An Overview
By Eric Larson, Art of Mass Production
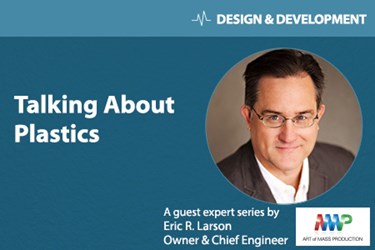
Earlier in this series, we talked about plastic material selection, and some of the unique challenges involved in medical device design. We also discussed the importance of feel in medical device design, with feel referring not just to tactile perception, but to the entire user experience. Our next articles will explore plastic material selection for medical devices, primarily wearables. First, we will discuss the use of rigid materials, followed by a discussion covering the use of elastomeric materials.
What Are Medical Wearables?
The term wearable is used to describe something that can be worn on the body or attached to our clothing. Thus, a medical wearable is a device worn on the body or clothing that provides diagnosis, treatment, or alleviation of disease, compensation for an injury or handicap, etc.
Medical wearables have been with us for a long time, starting with bandages, thousands of years ago. Eyeglasses were invented in the late 13th century. The ubiquitous Band-Aid was invented in 1920. The difference is that, when we speak of medical wearables today, we usually are usually referring to devices with embedded electronics, including sensors, processors, and data storage capability. Most often, the term wearable technology also connotes some level of wireless connectivity, via Bluetooth, Wi-Fi, or cellular networks. So, when we use the term medical wearable, we most often mean a device worn on the body or clothing, used for a diagnostic and/or therapeutic purpose, and embedded with electronics and wireless connectivity.
Standards Organizations
Most wearable technology in use today has its origins in the communications industry. We have wireless headsets for our phones, wireless microphones for speaking and performing, and wireless cameras for security. As use of wearable technology rapidly expands for communications applications, it also has seen significant growth in applications for health and wellness, especially fitness. These devices typically are categorized as consumer devices, and their use often is regulated by safety standards from organizations such as UL (formerly known as Underwriter Laboratories) or the Consumer Product Safety Commission. The use of wireless technology itself is regulated by a division of the Federal Communications Commission (FCC).
There are only a few wearable devices that can truly be considered medical wearables. Some notable examples include BioTelemetry Healthcare (formely Cardionet), which provides wearable devices for cardiac monitoring, and Dexcom, which provides wearable continuous glucose monitors (CGMs). However, the intersection of personal communications, wireless connectivity, and medical technology is a fertile field for innovation. It also is a complex intersection, presenting unique challenges. Both the FDA and the FCC have recognized this, and both organizations have made substantial commitments to regulate the manufacture and use of these devices.
The purpose of this article is not to debate the proper methodology for regulating these devices. Rather, it is to discuss the effective use of plastic materials in these devices, and to provide some guidance to designers, engineers and manufacturers on proper material selection.
Mechanical Requirements
In wearable devices, rigid plastic materials typically are used in parts that have structural requirements, such as housings, fittings, fasteners, and connectors. In all of these applications, the strength and stiffness of the base material is important, but the strength and stiffness of a given structure also is heavily dependent on part design. Selecting a material purely on the basis of its tensile strength or flexural modulus is not a recommended practice. Instead, the material should be selected in conjunction with a specific part design. As the design evolves, the material selected often evolves, as well.
However, toughness often is a critical material property. In engineering terms, toughness is used to describe the ability of a material to withstand impact. In practical terms, toughness also describes the ability of a material to withstand long-term use and abuse. This includes not just impact (at high and/or low speeds), but also what might be described as durability - resistance to scratching, marring, and abrasion, as well as to cracking or crack propagation from impact (either single or multiple). While specific tests can be used to quantify various aspects of material toughness, actual real-life performance of a given device can be difficult to predict. Testing that simulates actual end-use conditions is often the best way to evaluate material candidates.
Temperature Requirements
Wearable devices typically operate in a moderate range of temperatures. Since they are worn by human beings, they are typically in use at temperatures in which humans can survive, ranging from slightly below freezing (0° C / 32° F) to desert-like temperatures (50° C / 122° F).
While it is rare that a wearable device will be used outside of this temperature range, one needs to account for the possibility of device transportation and/or storage under extreme temperatures.
Chemical Resistance
In day-to-day use, most wearable devices will encounter a variety of chemicals, primarily common household ones. This includes mild chemicals, such as hand soap, shampoo, laundry detergent, and even toothpaste, but also some stronger chemicals, such as hand sanitizers, household cleaners, and bleach. In most situations, the device will be exposed to these chemicals intermittently, and only for short durations. However, for safety considerations, it often is prudent to design for longer-term exposure.
For most devices, there is some requirement for cleaning, whether it involves basic soap and water or a more aggressive procedure. Rarely are wearable devices intended to be sterilized, though some devices are intended for use by multiple users. The procedure for cleaning and disinfection (and the disinfectant used) should be clearly identified in the design phase, as this can affect material selection.
Finally, there is another chemical that often is overlooked: water. Most of us think of water as an inert material, but for some materials (such as raw iron) exposure to water causes a chemical reaction. Fortunately, most thermoplastics do not chemically react with water. But there are some thermoplastics, such as nylon (and, to a lesser extent ABS, acetal, and polycarbonate), that absorb water. This absorption process, which usually is reversible, causes the material to swell, and also acts as a plasticizer, making the material tougher, more flexible, and more ductile, though it also reduces the material’s strength.
Also, we often forget that water is a polar solvent (often known as the universal solvent), and can act as a solvent for other chemicals. Thus, while exposure to water may not be an issue, the chemical(s) contained in the water could be problematic. Understanding the water source — be it rainfall, a well, a river, a stream, a lake, an ocean, or even human sweat — will provide insight into what chemicals and minerals the water may contain.
Biocompatibility
For contact with human skin, we want a material that is benign. In the medical world, we use the term biocompatibility to describe a material’s capability to coexist with living tissue without causing harm, be it rashes, toxicity, or physical damage of any other kind. This is a demanding requirement, but it is absolute. Many thermoplastic materials are biocompatible in their neat form — a neat resin, also known as a pure resin, is one that has not been modified in any way from its original as-polymerized condition. However, most commercially available plastic materials have been modified in some way, usually via additives (UV stabilizers, processing aids, colorants, plasticizers, etc.). So, biocompatibility must be determined based not just on the base resin, but on the specific grade and version being used.
Processing Requirements
Rigid materials used in a wearable device typically are applied to parts with a high degree of complexity (i.e., we are not just using them as a spacer, or a gasket, or a thin membrane). Most of the time, the preferred processing method for these parts is injection molding. On occasion, we may also use parts machined from a stock shape (e.g., a bar, sheet, or slab). This processing technology is best suited for lower production volumes.
In addition, the parts typically will be subject to some type of assembly method, involving either ultrasonic welding, adhesive bonding, threaded fasteners, or some type of snap fit. While almost all thermoplastics can be welded, amorphous materials (such as ABS, ASA, and polycarbonate) generally are more receptive to adhesive bonding than semi-crystalline materials (such as acetal, polyamide, and polyester).
Molded parts also may be subject to handling prior to, during, and after assembly. Thus, the parts’ durability may be considered both a mechanical requirement and a processing requirement. Material toughness is a factor, as is material hardness and lubricity, all of which play a role in marring and abrasion. Proper material selection can reduce scrap due to handling-related damage, effectively reducing overall processing costs.
Material selection based on processing requirements also involves consideration of the additives used in the resin, especially colorants and processing agents.
The requirements we have discussed thus far are, in many ways, similar to the requirements for tools, household goods, and consumer electronics. We’ll discuss some of the requirements unique to wearable devices in the next part of this series.
Read part two of this three-part series here. Part three is available here.
About The Author
Eric R. Larson is a mechanical engineer with over 30 years' experience in plastics. He has helped develop products ranging from boogie boards, water basketball games and SCUBA diving equipment to disposable lighters, cell phones and handheld medical devices. Eric is owner of Art of Mass Production (AMP), an engineering consulting company based in San Diego, CA. AMP provides services to manufacturing companies in the consumer electronics, wireless, and medical device industries. Eric is also moderator of the blog site plasticsguy.com, where he writes about plastics technology and its effect on people and the planet.
References: Industry Standards
- IEC 60601-1-2 - General requirements for basic safety and essential performance - Collateral standard: Electromagnetic compatibility - Requirements and tests.
- 60601-1-11 - Requirements for Medical Electrical Equipment and Medical Electrical Systems Used in Home Care Applications.
- ISO 10993 - Biological evaluation of medical devices for the safety of skin contact applications. (Note: ISO 10993 currently has 20 parts; Part 10 Tests for irritation and skin sensitization.)
- Design Considerations for Devices Intended for Home Use. (Guidance document, issued Nov 2014, updated Aug 2016). Food and Drug Administration.
- Applying Human Factors and Usability Engineering to Medical Devices. (Guidance document, issued Feb 2016). Food and Drug Administration.
- Radio Frequency Wireless Technology in Medical Devices. (Guidance document, issued Aug 2013). Food and Drug Administration.
- Biological Reactivity Tests, In Vivo. U.S. Pharmacopeia standards. USP 88.
- Medical Device Regulations: Global overview and guiding principles. (2003). The World Health Organization.