Test Method Development, Experimental Design And Positive Controls For Package Integrity
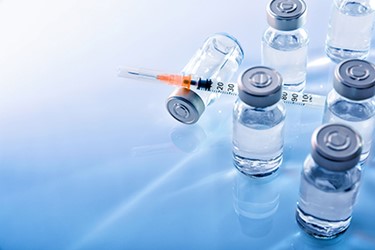
Package integrity can be defined as a package’s ability to prevent product loss, maintain product sterility, and in some cases, prevent oxygen ingress or maintain sub-atmosphere headspace pressures. The characterization of integrity separates packages into leaking and non-leaking samples and allows for the validation of a test method to be a very simple experiment. There are only two conditions, non-leaking and leaking. Samples representing both groups are subjected to a test and the results for each should be measurably different from the other. Samples with either a non-leaking circumstance or a known leak defect are introduced to the test and should be correctly identified as non-leaking or defective.
Given that the experimental design has only two conditions, leaking and non-leaking, this variable is extremely important to understand. Conventional thought is that non-leaking samples (or assumed non-leaking samples) are simply sealed packages in which no leak should be present. Realistically, all packages leak to some degree within the requirements of that package application. This inherent package leakage is referred to as the Maximum Allowable Leakage Limit (MALL). Creating leaking samples of known leak sizes is more complex and requires a thorough understanding of package, product, and leak dynamics. Proper use of positive controls and knowledge of how alternative approaches are applied to challenge a test method support the validity and reliability of the method.
Get unlimited access to:
Enter your credentials below to log in. Not yet a member of Med Device Online? Subscribe today.