The Non-Negotiable Need For Quality In Micro Molding
By Brett Saddoris, Technical Marketing Manager, Accumold
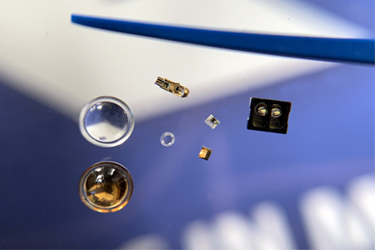
Micro molding is a highly specialized and demanding field of precision manufacturing, critical for industries requiring ultra-small, intricate components. As parts shrink and tolerances tighten, quality becomes not just important, but essential. This article highlights Accumold’s approach to ensuring top-tier quality in micro molding, emphasizing that success depends on integrating precision, metrology, and validation from the earliest design stages.
Accumold’s process embeds quality control across the entire production cycle, using advanced non-contact metrology tools such as Zygo’s NewView 8300 Optical Profiler and multi-sensor Optical Gaging Products (OGP) systems. These enable sub-micron accuracy in measuring features that are often invisible to the naked eye. Additionally, Accumold custom-builds fixtures to ensure repeatable and reliable measurements and applies white light interferometry to evaluate surface roughness without damaging delicate parts.
The article stresses that being able to mold a part does not guarantee the ability to measure it accurately. Metrology must be considered during product development, including Gage R&R studies and DFM/DfMM collaboration. For complex projects, in-process metrology is also used to ensure real-time quality control.
Continuous improvement is core to Accumold’s quality assurance strategy. The company actively evaluates new metrology technologies and uses automated vision inspection systems to maintain accuracy at high production volumes.
Ultimately, quality defines the success of micro molding. Manufacturers must prioritize quality capabilities—especially metrology—when choosing a partner. With its dedicated focus on precision and innovation, Accumold sets the standard for high-quality micro molding in global markets.
Get unlimited access to:
Enter your credentials below to log in. Not yet a member of Med Device Online? Subscribe today.