The Role Of Micro Molding In The Making Of Optics For Augmented Reality Applications
Brett Saddoris, Technical Marketing Manager, Accumold
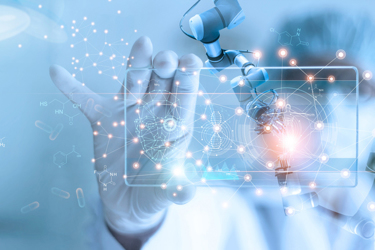
Augmented reality (AR) devices rely heavily on precise optical components, such as lenses, light guides, and diffractive optical elements (DOEs), to ensure seamless digital overlays and clear images. Micro molding has become essential for producing these intricate parts with micron-level accuracy, meeting the stringent demands of AR systems. Since even slight deviations in the shape or alignment of these components can cause image distortion, micro molding ensures precision to maintain optical clarity.
AR applications require lightweight and compact components, especially for devices like smart glasses, where user comfort is crucial. Micro molding enables the production of tiny parts—ranging from 20 microns to 1 mm—while maintaining tight tolerances and high surface quality to reduce light scattering. This process ensures that optical components function flawlessly and align accurately in short optical paths, essential for AR displays.
The development of AR optics also involves collaboration between micro molders and product designers, optimizing manufacturability through Design for Micro Molding (DfMM) principles. Custom molding machines are often required to replicate intricate features like surface relief patterns in DOEs or micro lens arrays with nanometer precision.
Applications of micro molding in AR include head-up displays (HUDs) in automotive and aviation, AR smart glasses, and medical imaging systems. Each application demands reliability, precision, and high-performance optics. As AR adoption grows, the importance of micro molding in delivering scalable, high-quality optical components will continue to rise, ensuring these technologies meet evolving industry demands.
Get unlimited access to:
Enter your credentials below to log in. Not yet a member of Med Device Online? Subscribe today.