Value Stream Mapping For Medical Device Companies, Part 2
By Darren Dolcemascolo, senior partner and co-founder, EMS Consulting Group
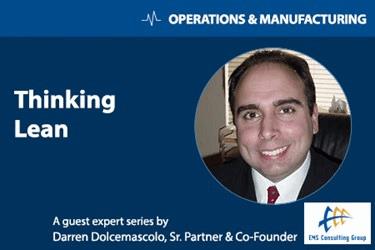
In this edition of Thinking Lean, we are going to complete our two-part series on value stream mapping. In the part one of the series, we addressed the concepts of value stream identification and current state mapping. In this article, we will talk about mapping the future state and creating a value stream plan.
After creating a current state map, a company will have gained an understanding of how they do things today, including the non-value added wastes. Recall from our first article that the seven wastes include:
- Overproduction
- Transportation
- Unnecessary inventory
- Inappropriate processing
- Waiting
- Excess motion
- Defects
It is with these wastes in mind that value stream mappers pursue the design of a future state with less waste. The future state goals might include company goals identified through strategy deployment, the process by which the management team works with all levels of the organization to identify specific goals and metrics to be achieved over time. Value stream mapping can provide a layer of analysis to better refine both these goals and the path to practically reach them.
There are basic principles that the value stream mapping team would want to address to design a future state that works. These principles, sometimes formulated as questions, can be the basis of a brainstorming activity:
- What is the rate of customer demand and/or the takt time?
Takt time is calculated by dividing the available working time in a period by the average number of units demanded in a period.
- What is an appropriate inventory storage strategy?
Consider whether or not finished goods are needed for some or all products, whether the product line lends itself to make-to-order, and whether other forms of inventory are needed (e.g., sub-assemblies, semi-finished goods, etc.).
- Which process should be the pacesetter/pacemaker, and how will we create a level schedule?
In other words, which process should be scheduled? In lean thinking, only one process should be scheduled, and the other processes should be tied to that product utilizing pull systems. When we schedule a process, how will we ensure that we have a level schedule in terms of volume and mix? We would like to produce evenly, rather than in a choppy manner. If we have “evenness” to our scheduling, our entire value stream can be level. Conversely, an uneven schedule will produce chaos in our value stream.
- How will the processes be connected?
A lean thinker would see three major possibilities here:
- One Piece Flow / Continuous Flow – This is the ideal method for connecting flow between processes, because it has the fastest lead time and the smallest amount of inventory.
- FIFO Flow / Sequenced Pull – Using this method, there is a small sequenced amount of inventory (using first-in-first-out) between processes. The downstream process pulls from the FIFO lane, and the upstream process produces into the FIFO lane until it is full. A full FIFO lane is a visual control and limits inventory.
- Replenishment Pull System – This is the most common type of pull system, in which we have inventory stored in a supermarket (organized by part number). As inventory is pulled from the supermarket into the downstream process, a kanban, or signal, is used to instruct the upstream process to produce and replenish the supermarket.
- Which process improvements are necessary to make the process work?
These improvements would include things like improving equipment uptime, cross-training people, creating standard work for a process, reducing variation or defects, error proofing, reducing changeover time on a machine, etc. As a team creates their future state, they might identify additional process improvements that need to be made.
At this point in a value stream mapping workshop, the facilitator would lead the value stream team through a brainstorming session, in which the team would brainstorm ideas for the future state based on these questions. After gaining consensus on and mapping a future state, the team would develop a high-level plan of action, called a value stream plan. Let us illustrate this process using the medical diagnostic equipment manufacturer case example from our last article. Here is the current state map:
Let’s begin by looking at the answers to the questions.
- What are the customer requirements for this company?
Total customer demand per day for A, B, and C products is 330 units. Working time is 8 hours, minus the two 15-minute breaks. We do not consider lunch, since it is unpaid and outside of the 8 hours. Thus, takt time is 450 minutes working time divided by 330 units per day, which equals 1.36 minutes, or 81 seconds. This means that, ideally, each point in the value stream would produce one unit every 81 seconds. It also means that we must design the value stream so that it can meet this level of demand.
- What is an appropriate inventory strategy for this company?
This diagnostic equipment manufacturer is going to build everything to-order since the promised lead-time to their customer is two weeks, and they are planning on a significantly shorter internal lead-time. When a customer places an order, the company has two weeks to build and ship the product, and its future state will be designed such that the actual internal production lead time will be much shorter than this.
- Which process should be the pacesetter/pacemaker, and how will they create a level schedule?
The assembly process will be the pacesetter (scheduling point), because a product becomes a specific part number for a customer during assembly. It would not make sense for customer orders to go to metal stamping, since this is a “batch” process by nature. Assembly will actually make product per customer order, and then pass it on to test. They will level production internally based on a short internal lead-time; customer order quantities will vary each day, but they will be able to build about the same number of products each day.
- How will the processes be connected?
There are three connection points:
- Assembly to Test — Since assembly will be the scheduling point, assembly and test will be connected via a FIFO lane. Assembly will build product to-order, based on customer order sequence, and Test will pull assembled product from the FIFO lane in the same sequence.
- Metal Stamping to Assembly — Metal Stamping will replenish a supermarket based on assembly pulling product from the supermarket. This is a replenishment pull system.
- Supplier to Metal Stamping — They will implement a replenishment pull system with their metal supplier and increase delivery frequency, since this supplier is local.
- Which process improvements are necessary to make the process work?
In order for this manufacturer to make the future state work, they need three key process improvements or kaizen bursts:
- Reduce metal stamping changeover. The intent is to twice daily build batch sizes equal to a half-day of assembly’s production.
- Improve uptime on test equipment.
- Reduce rework at test (by determining and eliminating root causes of the rework).
In the future state map, we now see these improvements represented graphically. We haven’t changed the information flow, but the company has made the following changes: Beginning with the supplier icon, we see that the company has gone to weekly deliveries on all items, and will hold up to 7.5 business days of purchased parts and raw material inventory — down from 30 days. Next, we see that twice daily builds in metal stamping will result in a supermarket of less than one day worth of metal stamped parts. Assembly will produce to a FIFO lane that will hold, at most, one day worth of material, and test will build directly to shipping.
This results in a lead time of 9.5 days, and an internal production lead time of only two days if we subtract the 7.5 days of purchased product. The company will easily be able to level their schedule, since they have a two-week promised lead time to the customer. In summary, the lead time improvement is a change from a range of 43 to 58 days in the current state, to only 9.5 days in the future state. The internal lead-time improvement goes from a range of 13 to 28 days in the current state, to only two days in the future state.
Below is the company’s plan to implement its future state. The entire program is planned for completion in 4 months, with a start date of April 15th and a completion date of August 15th.
In summary, value stream mapping is a high-level, strategic methodology for developing an improvement plan. Through the use of this medical diagnostic company case study, we hope that you will see the value in this methodology and will consider utilizing it to work toward breakthrough improvement in your value streams.