Your Guide To Selecting Safety Capacitors For EMI Filtering In The PFC Stage Of An AC/DC Converter
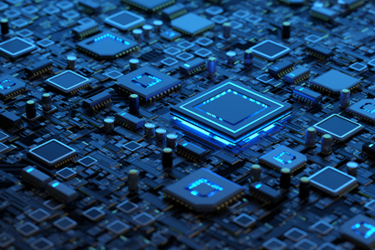
Choosing the right safety capacitor for a power factor correction (PFC) circuit involves a systematic, multi-step process to ensure effective EMI filtering and long-term reliability. It begins with analyzing your conducted emissions test data to pinpoint problematic frequency bands. For example, if your design exceeds noise limits by 25 dB at 500 kHz, you'll need a capacitor filter that provides at least 30 dB attenuation at that frequency to maintain a safety margin.
Next, match the capacitor’s voltage rating to your actual circuit conditions, accounting for nominal and surge voltages. Avoid mixing AC and DC ratings, and select components capable of handling transient events common in industrial environments. Then, evaluate your circuit configuration—single or multi-element—based on impedance, required filtering, and available space.
Once your basic needs are defined, assess the electrical characteristics of potential capacitors. Key parameters include capacitance value, ESR (Equivalent Series Resistance), dissipation factor, and Q factor, all of which influence filtering effectiveness and thermal stability.
Physical considerations—such as mounting method, size, and environmental ratings (temperature, humidity, vibration)—also play a critical role in selection. Ensure capacitors are properly certified (e.g., UL, VDE, ENEC) and meet safety standards: Class X capacitors must fail short; Class Y must fail open.
Finally, test the chosen capacitors in real-world conditions to validate EMI performance and compliance. Even with careful selection, tuning may be required. The right capacitor ensures not only regulatory compliance but also the reliable, safe operation of your AC/DC converter’s PFC stage.
Get unlimited access to:
Enter your credentials below to log in. Not yet a member of Med Device Online? Subscribe today.